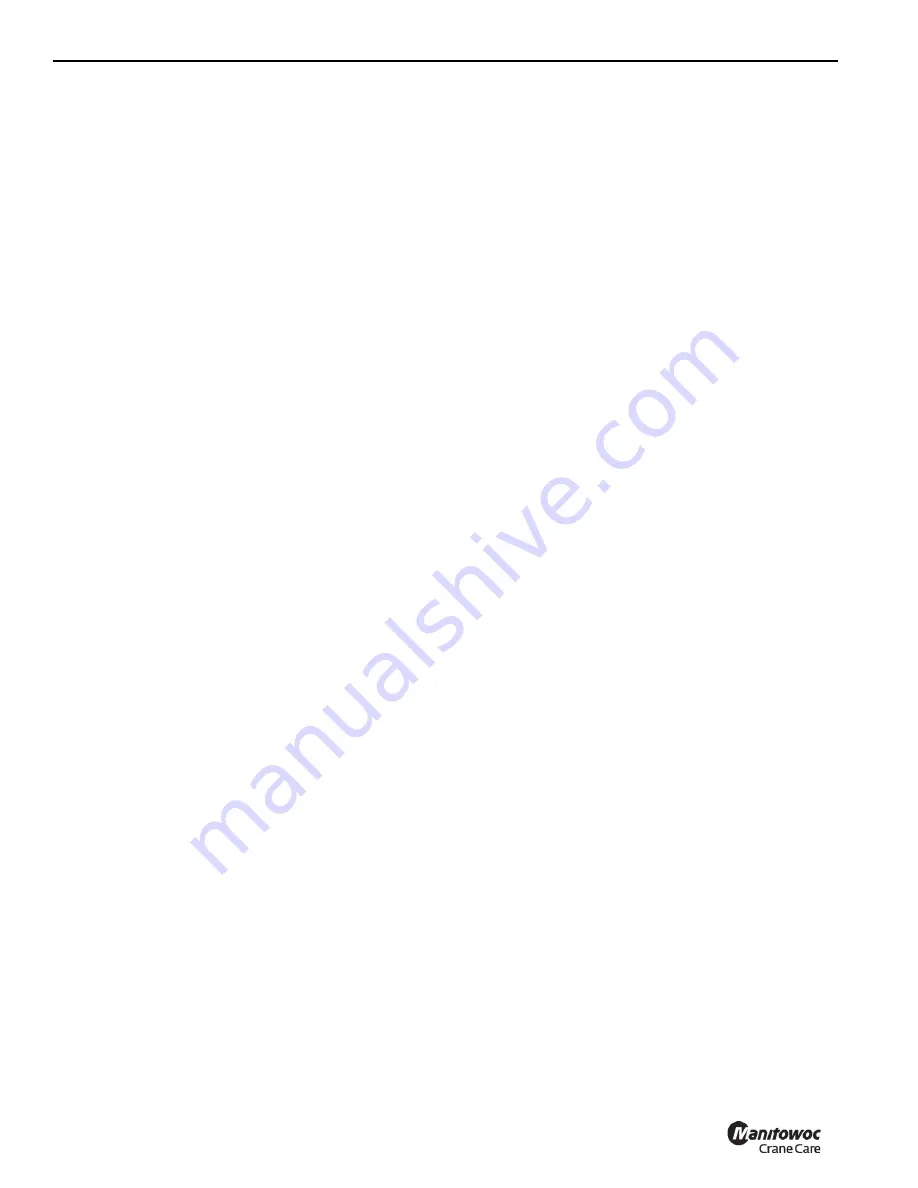
INSTALLATION
800D
9-16
Published 5-27-2018 Control # 039-06
TRUCK PREPARATION
Plan installation completely before any work is done. Plan
the location of the crane for the final front and rear axle
weights and boom overhang. Check final weight (see
Counterweighting Section to verify that final truck weight with
crane, reinforcement, counterweight and options such as jib,
etc. complies with the appropriate laws).
Welding Precautions
Sensitive truck computer system and crane’s RCL computer
system components may be damaged by welding on the
truck or crane. The following precautions should be taken:
•
Disconnect truck battery cables (positive and negative)
•
Attach welding ground lead as close as possible to area
to be welded.
Positioning Crane on Truck
The final user of the crane must be aware of all state axle
and length laws in force at the time of crane mounting and
position the crane on the truck accordingly. Following are
items which must be considered.
1.
Overall Length:
Most states have a maximum straight
truck length limit of 40 ft (12.19 m). Using too long a WB
truck could cause the unit to exceed this limit.
2.
Axle Weights:
All states allow 20,000 lb (9072 kg)
single axle weight and 34,000 lb (15 422 kg) tandem
axle weights on primary roads, however, some states
restrict axle weight to less on secondary roads or at
certain times throughout the year. Be aware of your
state’s axle laws and the roads the machine will operate
on for weight restrictions due to secondary roads,
bridges, winter driving conditions, etc.
3.
Overhang:
The most restrictive overhang laws call for a
maximum of 3 ft (0.91 m) in front of the truck. Many
states have a maximum of 4 ft (122 cm) overhang in
back of the truck. Check on your state requirements.
4.
Federal Bridge Law.
The Federal Bridge Law in effect
currently states that in order to carry 54,000 lb (24 494
kg) on a three axle truck, the extremes of any group of
axles must be at least 23.5 ft (7.16 m) apart. This
equates to a truck with a wheelbase of at least 258 in
(655 cm) with a minimum length of 24 in (60.96 cm) from
the center of tandems to the center of the rear axle.
PTO, Pump, Reservoir
1. Select the PTO according to the PTO Selection pages
shown earlier in this section. PTOs are not furnished by
the factory.
2. Install the PTO and PTO shifting mechanism according
to the PTO manufacturer’s instructions. If PTO has a
reverse gear, it must be blocked out. Pump must not run
backwards.
3. If PTO integral mount flanges are to be used, the pump
can be mounted directly to the PTO. Direct mount
pumps require lubrication of the spline shaft coupling.
See “Service and Maintenance” Section for lubrication
information. Be sure adequate clearance exists for this
type of pump mount. Sometimes the pump is powered
through a drive line with the pump located no more than
42 in (107 cm) from the PTO. The drive line should not
exceed a 15° angle. The drive line U-joint yokes on both
ends of the drive shaft must be parallel with each other.
Drive lines should be sized so they can safely carry the
maximum pump horsepower requirements. See “PTO
Selection” pages. Drive lines are not normally furnished
by the factory.
4. Plan the location of the pump mounting bracket and
drive line, if used, so that ample clearance is maintained
between pump and truck drive shaft or exhaust system.
Pump should be situated so that hydraulic lines can be
connected without sharp bends especially the large
suction line from the reservoir. Pump mounting brackets
may be attached to existing frame cross-members or a 6
in (15 cm) channel cross-member can be made and
installed.
5. Install pump mounting bracket (if used) securely to
frame. Attach pump to pump mounting plate or to PTO
using capscrews provided. Install the support bar at the
rear of the pump and bolt or weld the upper end to a
crossmember if the pump is mounted with a drive line or
install the support bar to a transmission bolt if the pump
is direct mounted to the PTO.
Note: Some of the pipe fittings used are sealed by
means of two threaded tapered sections, one male and
one female. When these two tapers meet, you will note a
sudden increase in the force required to screw the
fittings together. This is true of all tapered pipe threads.
Further tightening will not only fail to increase the
pressure tightness of the joint, but may ruin the
connections and make correct assembly impossible.
Other fittings are of the o-ring boss type. These are
installed by first screwing the lock nut flush to the upper
thread land and installing fitting into port until the nut
contacts the surface of the port. Adjust fitting to desired
direction. Tighten locknut.
Most pressure fittings are the O-ring face seal types. A
small O-ring is compressed between the male and the
female fittings of the joint. Be sure the O-ring is present
on the fitting and seated properly in its groove before
the fittings are tightened.
6. Remove the dust covers from the pump inlet and outlet
and determine that the suction and pressure sides of the
pump are correct while rotating the pump in the same
direction as the PTO. Rotate the pump in the mounting
Fo
r
Reference
Only
Содержание National Crane 800D
Страница 1: ...Operator and Service Manual National Crane 800D F o r R e f e r e n c e O n l y ...
Страница 4: ...F o r R e f e r e n c e O n l y ...
Страница 98: ...MAINTENANCE 800D 3 10 Published 5 27 2018 Control 039 06 THIS PAGE BLANK F o r R e f e r e n c e O n l y ...
Страница 194: ...SPECIFICATIONS 800D 8 4 Published 5 27 2018 Control 039 06 THIS PAGE BLANK F o r R e f e r e n c e O n l y ...
Страница 216: ...INSTALLATION 800D 9 22 Published 5 27 2018 Control 039 06 THIS PAGE BLANK F o r R e f e r e n c e O n l y ...
Страница 232: ...CRANE INSTALLATION 800D 10 16 Published 5 27 2018 Control 039 06 THIS PAGE BLANK F o r R e f e r e n c e O n l y ...
Страница 252: ...SCHEMATICS 800D 2 Published 5 27 2018 Control 039 06 F o r R e f e r e n c e O n l y ...
Страница 255: ...F o r R e f e r e n c e O n l y ...
Страница 256: ...F o r R e f e r e n c e O n l y ...