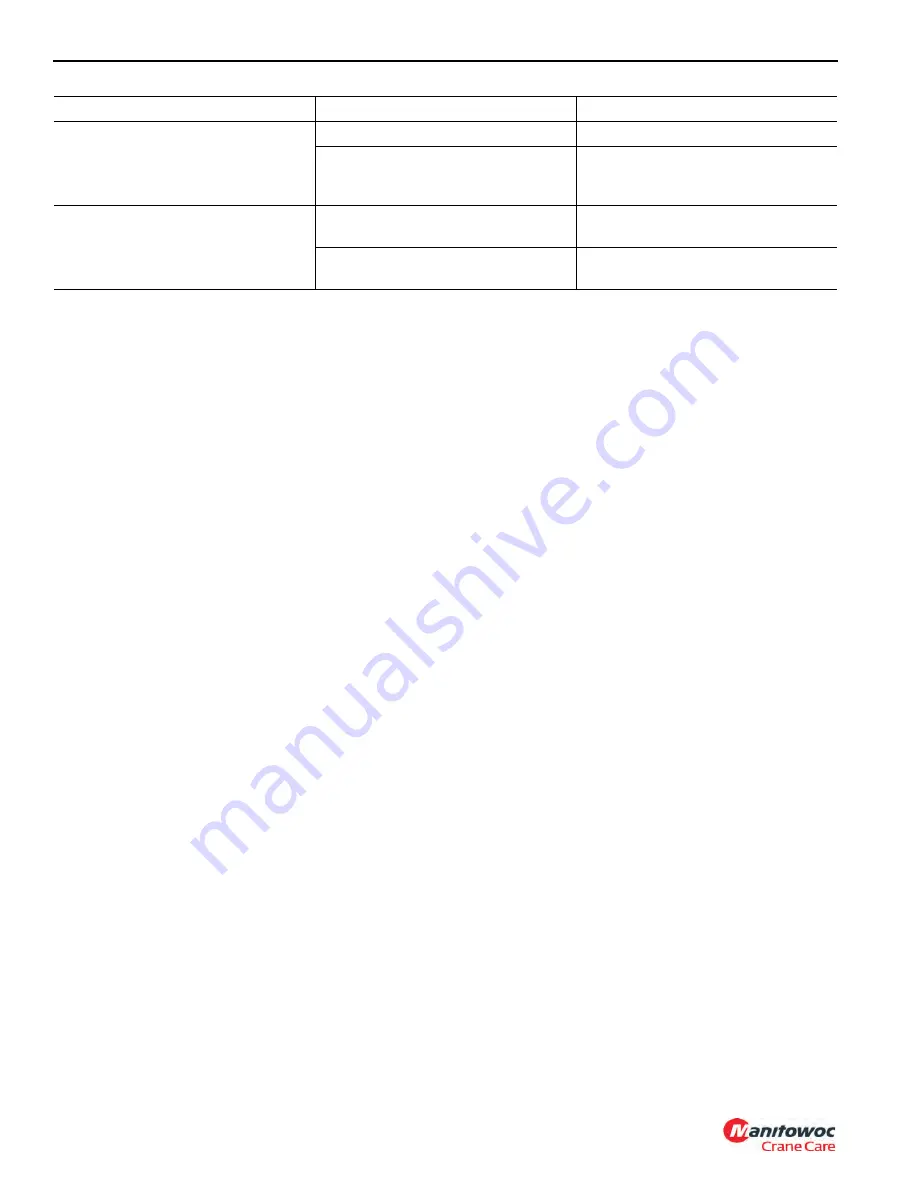
POWER TRAIN
RT765E-2 SERVICE MANUAL
7-26
Published 9-04-2014, Control # 422-08
Removal
1.
Extend and set the outriggers just enough to take up the
slack in the outrigger pads. Chock the wheels.
2.
Position the boom over the side and stop the engine.
3.
Remove the engine and transmission/torque converter
from the crane as an assembly. Refer to
4.
Remove the two-section and single section hydraulic
pumps from the transmission/torque converter. Cover all
openings. Refer to in
removal of the pump.
NOTE:
The transmission/torque converter weighs
approximately 966 lb (438 kg) dry.
5.
Attach an adequate lifting device to the transmission/
torque converter and take up any slack.
6.
Remove the capscrews and hardened flat washers
securing the drive plate assembly to the flywheel.
7.
Remove the nuts and washers securing the
transmission/torque converter housing to the engine
flywheel housing.
Installation
NOTE:
The transmission/torque converter assembly
weighs approximately 966 lb (438 kg) dry.
1.
If a new transmission/torque converter is to be installed,
remove all fittings and brackets from the old one and
i n s t a l l t h e m i n t h e s a m e l o c a t i o n s o n t h e n e w
transmission/torque converter.
2.
Install the two-section and single section hydraulic
pumps on the transmission/torque converter. Refer to
, page 2-17 for installation of the
hydraulic pump.
3.
Position the transmission/torque converter to the engine
with the lifting device.
4.
Remove all burrs from the flywheel mounting face and
nose pilot bore. Clean the drive plate surface with
solvent.
NOTE:
Refer to Figure 7-12.
5.
Check the engine flywheel and housing for conformance
to standard S.A.E. No. 3/S.A.E. J-927 tolerance
specifications for bore size, pilot bore runout and
mounting face flatness. Measure and record engine
crankshaft end play.
6.
Install the 12 studs in the engine flywheel housing.
Rotate the engine flywheel to align a drive plate
mounting screw hole with the flywheel housing front
access hole.
7.
Install a 4.00 in (101.6 mm) long drive plate locating stud
0.375-24 fine thread in a drive plate nut.
8.
Rotate the transmission/torque converter to align the
locating stud in the drive plate with the flywheel drive
plate mounting screw hole positioned in step 6. Locate
the transmission on the flywheel housing, aligning the
drive plate to the flywheel and the transmission on the
flywheel housing mounting studs. Install the
transmission to flywheel housing nuts and washers.
Tighten the nuts to 30 lb-ft (41 Nm).
9.
Remove the drive plate locating stud. Install one drive
plate attaching capscrew and lockwasher. Snug the
capscrew but
do not tighten
.
NOTE:
Some engine flywheel housings have a hole
located on the flywheel housing circumference in
line with the drive plate screw access hole. A
screwdriver or pry bar used to hold the drive plate
against the flywheel will facilitate installation of the
drive plate capscrews.
10.
Rotate the engine flywheel and install the remaining
seven flywheel to drive plate attaching capscrews and
hardened flat washers. Snug the capscrews but
do not
tighten
. After all eight capscrews and hardened flat
washers have been installed, torque the capscrews to
28 lb-ft (38 Nm). This will require torquing each
capscrew, then rotating the engine flywheel until all
capscrews have been torqued.
11.
Measure the engine crankshaft end play after the
transmission/torque converter has been completely
installed on the engine flywheel. This value must be
within 0.001 in (0.025 mm) of the end play recorded in
step 5.
4.
Noisy converter.
a.
Worn oil pump.
a.
Replace pump.
b.
Worn or damaged bearings.
b.
A complete disassembly will be
necessary to determine what
bearing is faulty.
5.
Lack of power.
a.
Low engine RPM at converter
stall.
a.
Tune engine and check
governor.
b.
See “Overheating” and make
same checks.
b.
Make corrections as explained
in “Overheating.”
SYMPTOM
PROBABLE CAUSE
REMEDY
Reference Only
Содержание Grove RT765E-2
Страница 1: ...Service Maintenance Manual Grove RT765E 2 R e f e r e n c e O n l y ...
Страница 2: ...R e f e r e n c e O n l y ...
Страница 278: ...UNDERCARRIAGE RT765E 2 SERVICE MANUAL 8 24 Published 9 04 2014 Control 422 08 FIGURE 8 28 R e f e r e n c e O n l y ...
Страница 320: ...LUBRICATION RT765E 2 SERVICE MANUAL 9 30 Published 9 04 2014 Control 422 08 FIGURE 9 12 102 R e f e r e n c e O n l y ...
Страница 326: ...LUBRICATION RT765E 2 SERVICE MANUAL 9 36 Published 9 04 2014 Control 422 08 THIS PAGE BLANK R e f e r e n c e O n l y ...
Страница 329: ...R e f e r e n c e O n l y ...
Страница 330: ...R e f e r e n c e O n l y ...