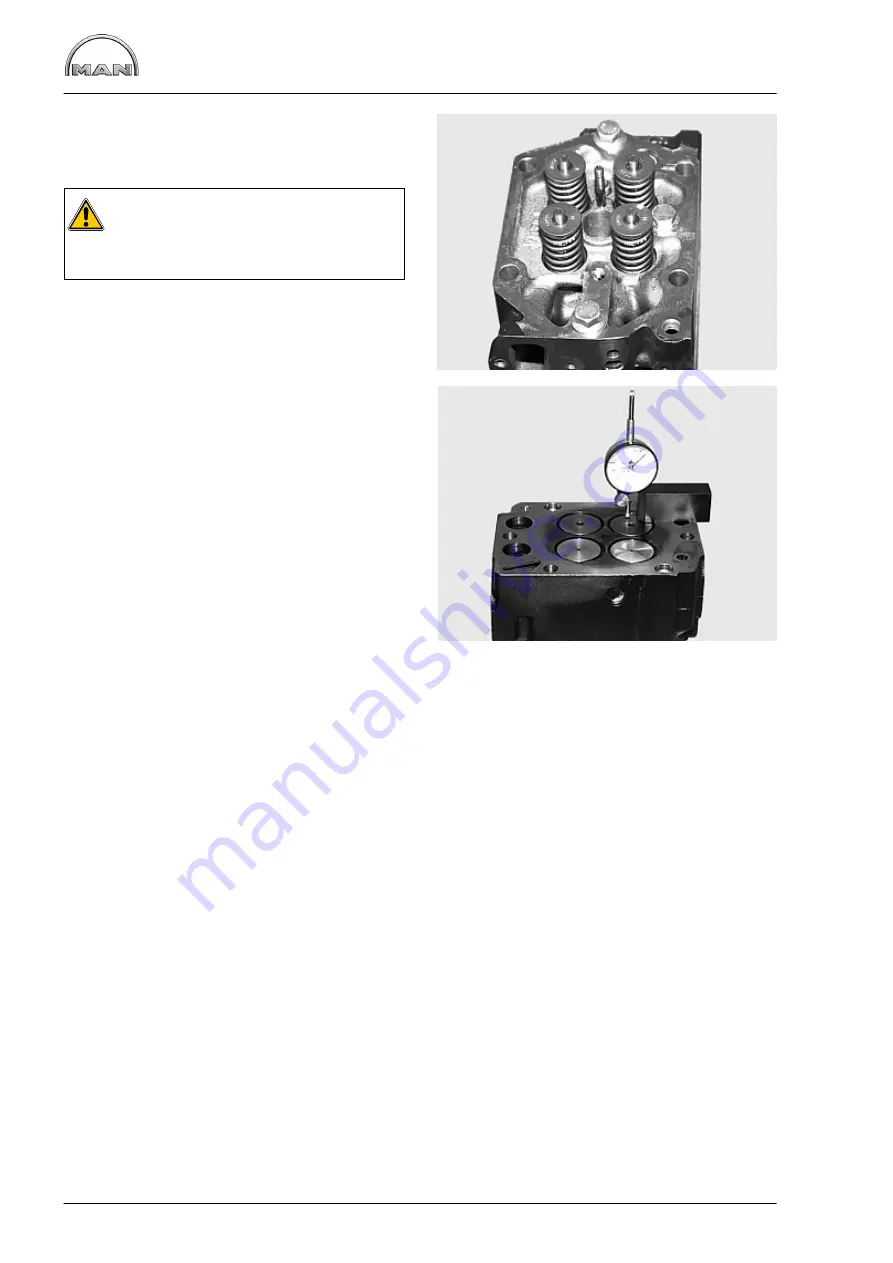
21
22
Removing and installing valves
92
Fig. 21
The valve tapers must snap reliably into place
when the pressure fork is released.
Caution:
Make sure the valve tapers are correctly
seated as tapers which spring out may
cause serious engine damage.
Measuring valve recess
Fig. 22
Position the dial gauge with its holder on the cylin-
der head. Set the tip of the dial gauge on the cylin-
der head and set the gauge to “0”, swivel to the
valve plate and read off the recess. Replace the
valve and valve seat insert if necessary.
Содержание D 2842 LE 620
Страница 1: ......
Страница 2: ......
Страница 20: ...Engine views D 2842 LE 620 18 7 1 2 4 3 5 6 7 1 2 4 11 9 10 8...
Страница 136: ...134...
Страница 137: ...135 Service Data...
Страница 163: ...161 Special tools...
Страница 164: ...Special tools 162 1 2 3 4 5 6 7 8 9 10 11 11 1 11 2 12 12 1 12 2 13 14...
Страница 166: ...Special tools 164 15 1 15 2 15 3 15 4 15 5 1 2 7 15 6 3 4 5 6 15 7...
Страница 168: ...Special tools 166 16 16 1 16 2 16 3 16 6 17 16 4 16 5 16 7 18 19 20 1 20 2 21 22 23 24 25 26 27 28...
Страница 170: ...Special tools 168 3 1 4 29 5 6 2 29 30 31 32 33 34 35...
Страница 172: ...Special tools 170 36 37 38 39 42 40 41 44 2 44 1 44 43 1 43 2 43 3 43 45 46...
Страница 178: ...176...
Страница 179: ......
Страница 180: ......