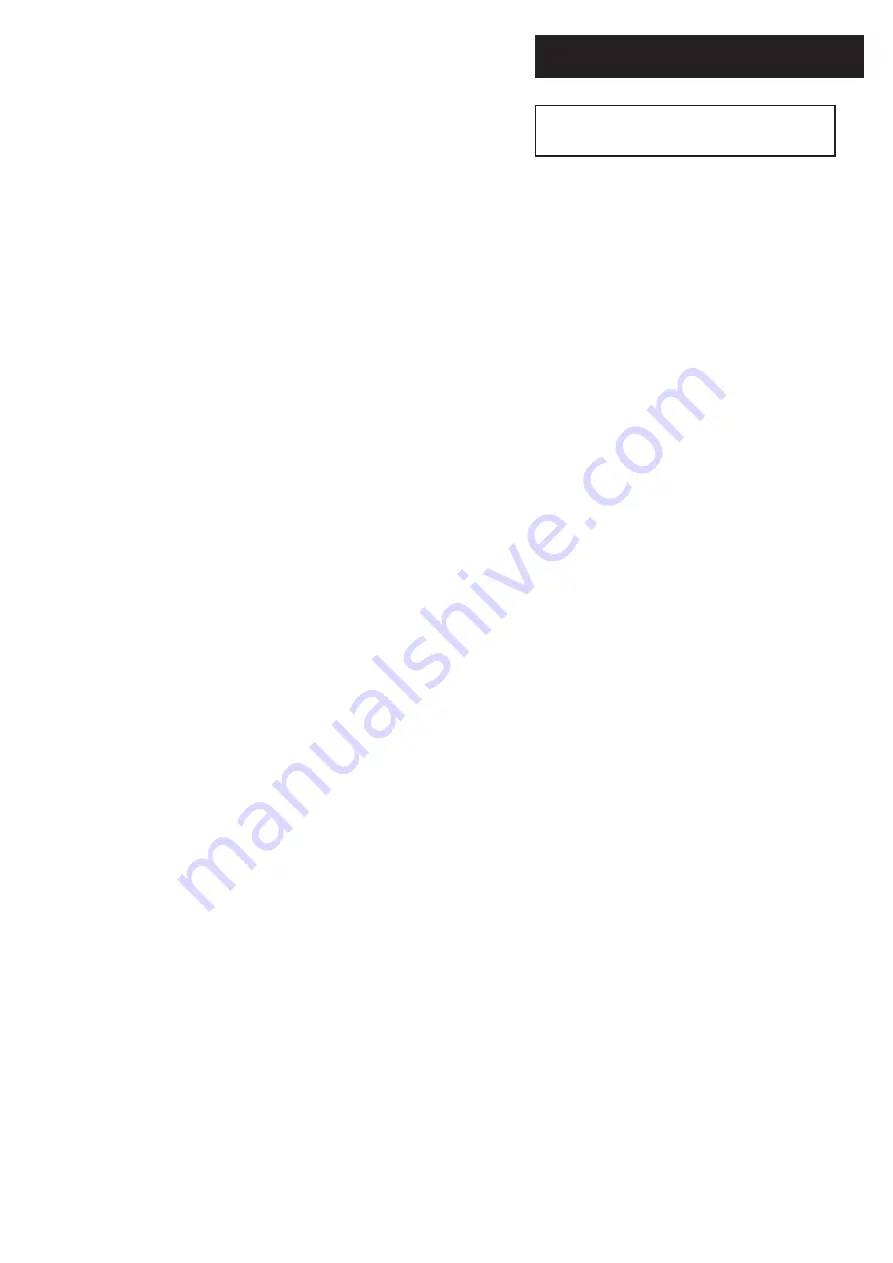
4
Legislation
© Baxi Heating UK Ltd 2011
Codes of Practice - refer to the most recent version
This company declare that no substances harmful to health
are contained in the appliance or used during appliance
manufacture.
The appliance is suitable only for installation in GB and IE and
should be installed in accordance with the rules in force, and
only used in a suitably ventilated location.
In GB, the installation must be carried out by a CORGI
Registered Installer. It must be carried out in accordance with
the relevant requirements of the:
• Gas Safety (Installation & Use) Regulations.
• The appropriate Building Regulations either The Building
Regulations, The Building Regulations (Scotland), Building
Regulations (Northern Ireland).
• The Water Fittings Regulations or Water Byelaws in
Scotland.
• The Current I.E.E. Wiring Regulations.
Where no specific instructions are given, reference should be
made to the relevant British Standard Code of Practice.
In IE, the installation must be carried out by a competent
Person and installed in accordance with the current edition of
I.S. 813 ‘Domestic Gas Installations’, the current Building
Regulations and reference should be made to the current ETCI
rules for electrical installation.
All systems must be thoroughly flushed and treated with
inhibitor (see section 6.2).
The boiler meets the requirements of Statutory Instrument “ The Boiler (Efficiency)
Regulations 1993 N
o
3083” and is deemed to meet the requirements of Directive
92/42/EEC on the energy efficiency requirements for new hot water boilers fired with
liquid or gaseous fuels:-
Type test for purpose of Regulation 5 certified by:
Notified Body 0087.
Product/Production certified by:
Notified Body 0086.
For GB/IE only.
IMPORTANT - Installation, Commissioning, Service & Repair
This appliance must be installed in accordance with the manufacturer’s instructions and
the regulations in force. Read the instructions fully before installing or using the
appliance.
In GB, this must be carried out by a competent person as stated in the Gas Safety
(Installation & Use) Regulations.
Definition of competence:
A person who works for a Gas Safe registered company
and holding current certificates in the relevant ACS modules, is deemed competent.
In IE, this must be carried out by a competent person as stated in I.S. 813 “Domestic
Gas Installations”.
The addition of anything that may interfere with the normal operation of the appliance
without express written permission from the manufacturer or his agent could invalidate
the appliance warranty. In GB this could also infringe the Gas Safety (Installation and
Use) Regulations.
Warning -
Check the information on the data plate is compatible with local supply
conditions.
All Gas Safe registered engineers carry an ID card with their licence number and a
photograph. You can check your engineer is registered by telephoning
0800 408 5500 or online at www.gassaferegister.co.uk
In GB the following Codes of Practice apply:
Standard
Scope
BS 6891
Gas Installation.
BS 5546
Installation of hot water supplies for domestic
purposes.
BS EN 12828
Heating systems in buildings.
BS EN 14336
Installation & commissioning of water based
heating systems.
BS 6798
Installation of gas fired hot water boilers.
BS 5440 Part 1
Flues.
BS 5440 Part 2
Ventilation.
BS 7074
Expansion vessels and ancillary equipment for
sealed water systems.
BS 7593
Treatment of water in domestic hot water
central heating systems.
In IE the following Codes of Practice apply:
Standard
Scope
I.S. 813
Domestic Gas Installations.
The following standards give valuable additional information;
BS 5546
Installation of hot water supplies for domestic
purposes.
BS EN 12828
Heating systems in buildings.
BS EN 14336
Installation & commissioning of water based
heating systems.
BS 7074
Expansion vessels and ancillary equipment for
sealed water systems.
BS 7593
Treatment of water in domestic hot water
central heating systems.
Supplied by HeatingSpares247.com