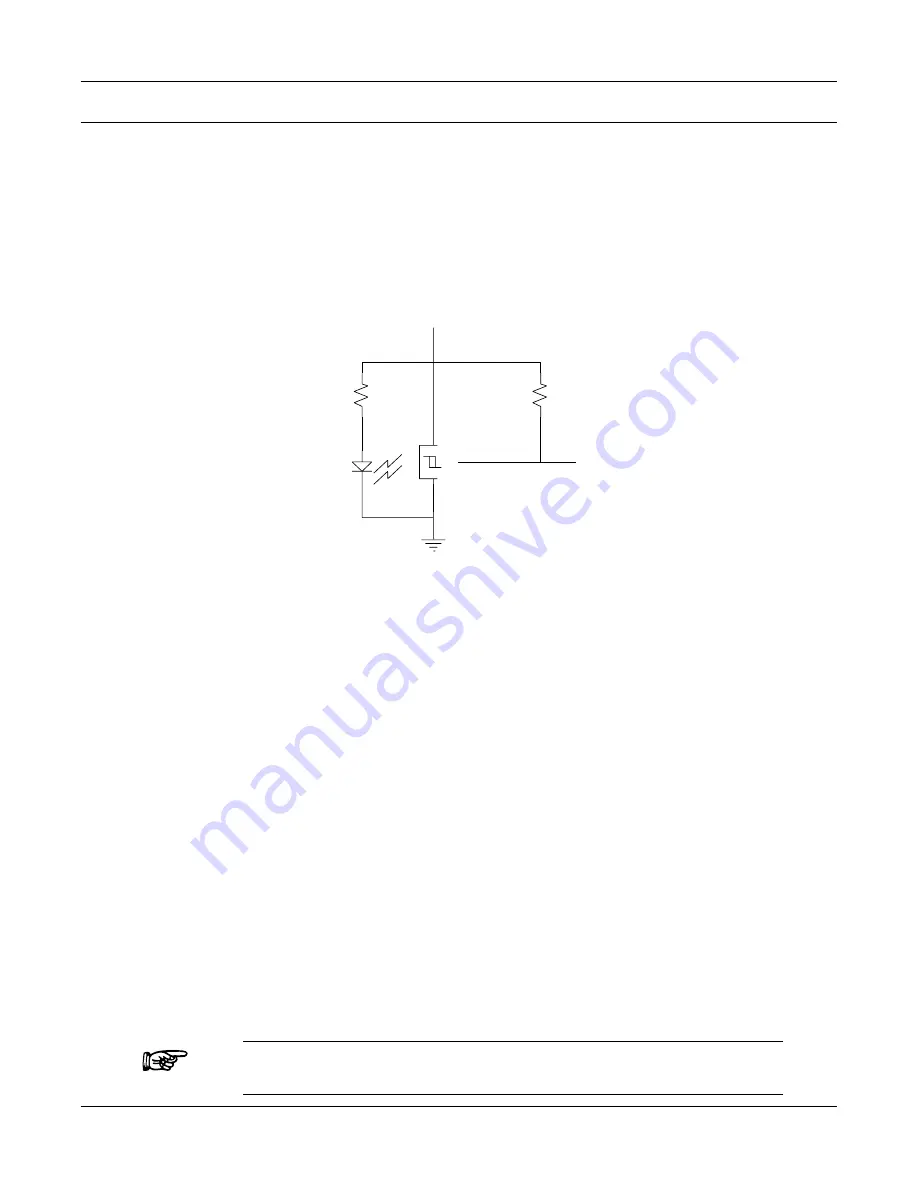
13
4. Operating Principles
4.1 SPEED
The dynamometer is shipped with an internal speed pickup and two cords: one terminating with a
2-pin plug for the brake power, the other is a 14-pin plug servicing an optical encoder. This encoder
consists of an infrared transmitter/receiver pair. On the end of the dynamometer shaft, positioned
between the LED and detector, is an optical disc with opaque and clear segments. Rotation of the
disc results in the detector generating a frequency of 60 pulses per shaft revolution.
R1
470
U1
4
OPB963
2
3
Fo
R2
200
5V (Pin 7)
5
(Pin 8)
(Pin 10)
1
Figure 4–1 Optical Encoder Circuit
4.2 TORQUE
Torsional force, acting upon the hysteresis brake, is produced by the test motor, and applied to the
brake’s rotor-shaft assembly. Whatever torque exists on the rotor-shaft, must be reacted upon equally
by the suspended brake-dial-weight assembly.
Since the brake assembly is imbalanced by the suspended weight attached to it, torsional force will
lift the weight. The graduated dial provides a readout value equal to this torque. Once the weights
are calibrated to match the dial graduations, the system accuracy becomes permanently fixed.
When torque is defined by a point on the radius of a weight, lifted in a circular motion, the scale
derivation is inherently a cosine function - thus, the nonlinear scale graduations.
4.2.1
t
orque
s
taBility
A major advantage in using a hysteresis brake as a loading means, is the ability to produce torque
essentially independent of speed. This permits very low speed and locked rotor torque testing.
Three factors have a minor secondary influence on hysteresis brake torque. They are:
• Hysteresis brake control current (
see Section 1.2.1
)
• Eddy current (
see Section 3.9
)
• Temperature rise (
see Section 3.10
)
Note:
Torque changes as a result of these influences are always part of the
actual torque measured—as applied to a test motor—and not errors.