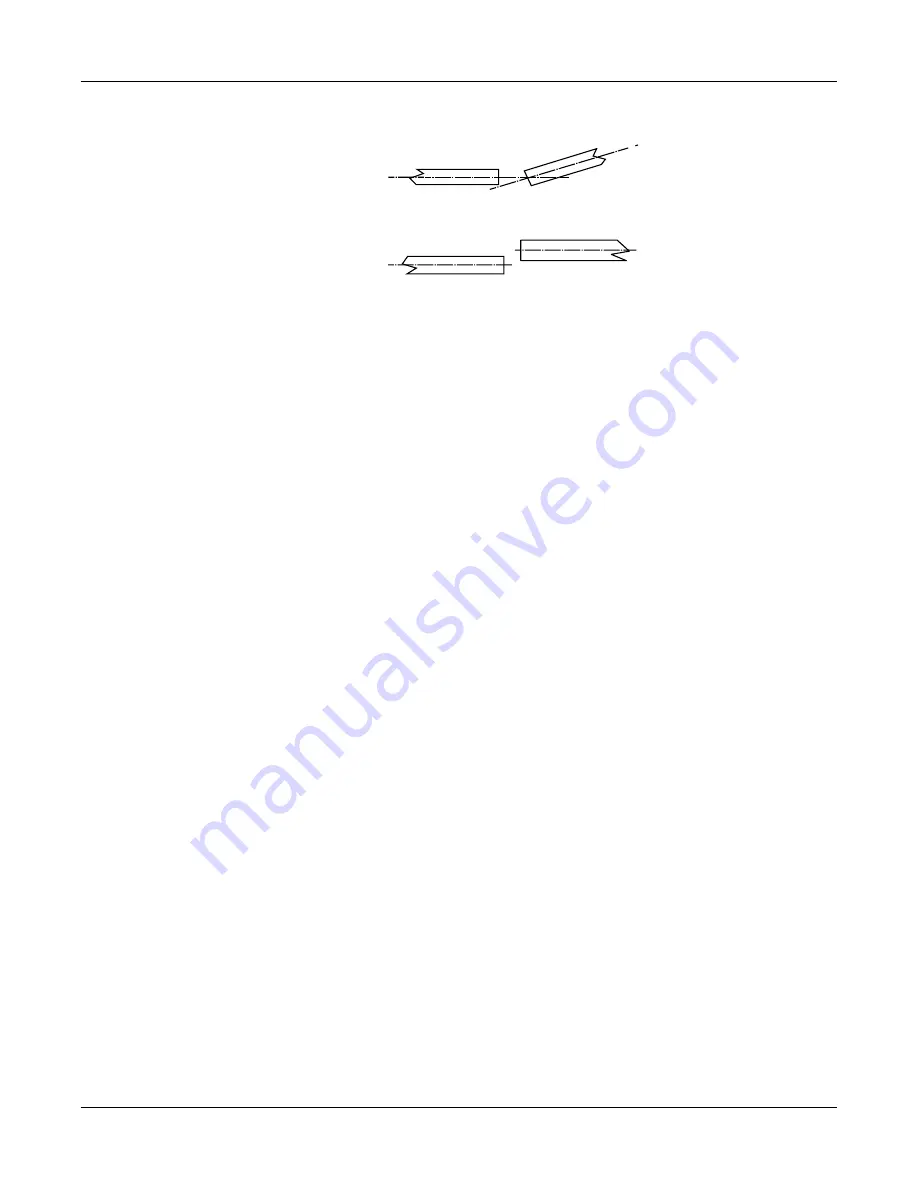
10
Magtrol Dial Weight Dynamometers
User’s Manual
The following diagram illustrates examples of possible shaft misalignment.
PARALLEL OFFSET
ANGULAR
Figure 3–8 Examples of Possible Shaft Misalignment
The use of high quality double flexure couplings is recommended to help correct any misalignment
problems. This type of coupling—two flexing elements separated by a solid link—inherently tolerates
greater parallel offset. If you would like more specific coupling recommendations, contact Magtrol
Technical Assistance. For precise misalignment tolerances, consult your coupling manufacturer.
3.5
WINDAGE
Although a smooth surface, the dynamometer rotor will drag air around with it. This air friction
is tangential to the surface and impinges upon the stationary field assembly. The viscous drag that
results then becomes part of the motor load and torque reading. However, there is a small amount
of air dissipated as pumping loss. Since this appears as a load on the motor, not measured by the
dynamometer, it becomes a source of error.
Windage effects on accuracy tests have been conducted on all Magtrol dynamometers. The percentage
of torque loss due to windage ranges between 0.025% and 0.20% of full scale at maximum rated
rpm. The larger percentage applies toward the smallest capacity dynamometer (HD-106). Because
windage is proportional to the square of speed, it magnifies rapidly above rated speed. Conversely,
at one half of the rated speed, the effect becomes immeasurably small.
3.6
FRICTION
Friction of the shaft bearings is a measurable load, but some friction can exist in the carrier bearing.
When correctly loaded and lubricated, the friction is insignificant. The value may be quantitatively
established by the following procedure.
1. Remove all attachments to the dynamometer shaft.
2. Swing the brake assembly up to full scale - by hand.
3. Carefully allow the assembly to return to zero without swinging back and forth.
4. Repeat steps 2 and 3—this time in the opposite direction—and note the reading.
The difference between zero and the second reading should be within the accuracy specifications
listed in
Section 1.2 – Technical Specifications
. During actual motor testing there is usually enough
system vibration to “settle” negating frictional effects. If excessive drag is present, mechanical
realignment may be required, dependent upon dynamometer size. Certain mechanical factors need
to be determined before corrective action proceeds. Please contact Magtrol Technical Assistance.