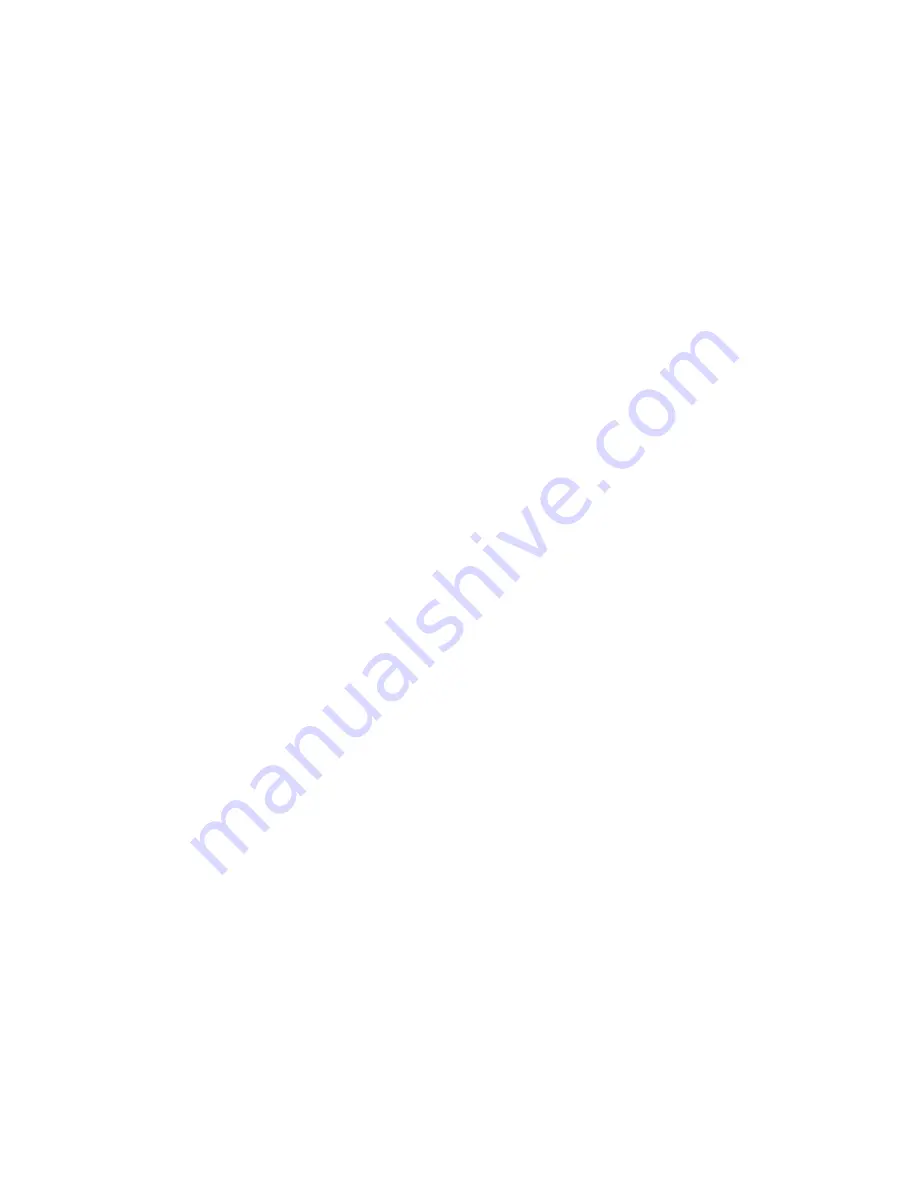
7. Operatings
★
"ON" and "OFF" indicating switch on the real panel.
★
Preset the welding voltage ,welding current(wire speed).and Arc force.Diagram 4
★
Confirm the specification of the wire feed hose
★
Confirm the specification of nib base .It affects the extended length of the wire .
★
Confirm the specification of nib. It affects the electric resistance.
★
Confirm the wire slot of the roller is suitable for the diameter of the wire. Different diameter of
wire select different wire slot. Otherwise it affects the wire feed result.
★
Confirm the pressure of the roller to avoid slipping.
If the pressure is not enough ,the wire feed is slow speed.
If the pressure is too much ,the wire will be anamorphic.
The wire feeder can not work properly.
★
Confirm the flow of the gas and air proof.
We suggest the gas flow to be "L" more than 10D(D-diameter of wire ).If the selection is not
proper,it also affects the welding quality.When using the CO
2
gas,please confirm if the heating power
works properly or not .
★
Straight the hose of welding gun as much as possible .The bending radius can not be less than
160mm.Otherwise it affects the wire feeder.
7.1 working process
press the switch of the gun ,the normal welding begins.Relax the switch,the arc stops.
7.2 Gas inspection
Press the switch of the gun before the wire roller is firmed,preset the gas flow through the meter to
check if it is gas proof.Otherwise ,it affects the welding result.
7.3Rip into the wire
Select the specification of the wire ,materials according to the craft requirements.Firm the bolt and
press the button on the front panel.The speed of ripping wire can be controlled by the welding current
knob.Unload the nib if necessary and load it again after the wire is out.
12