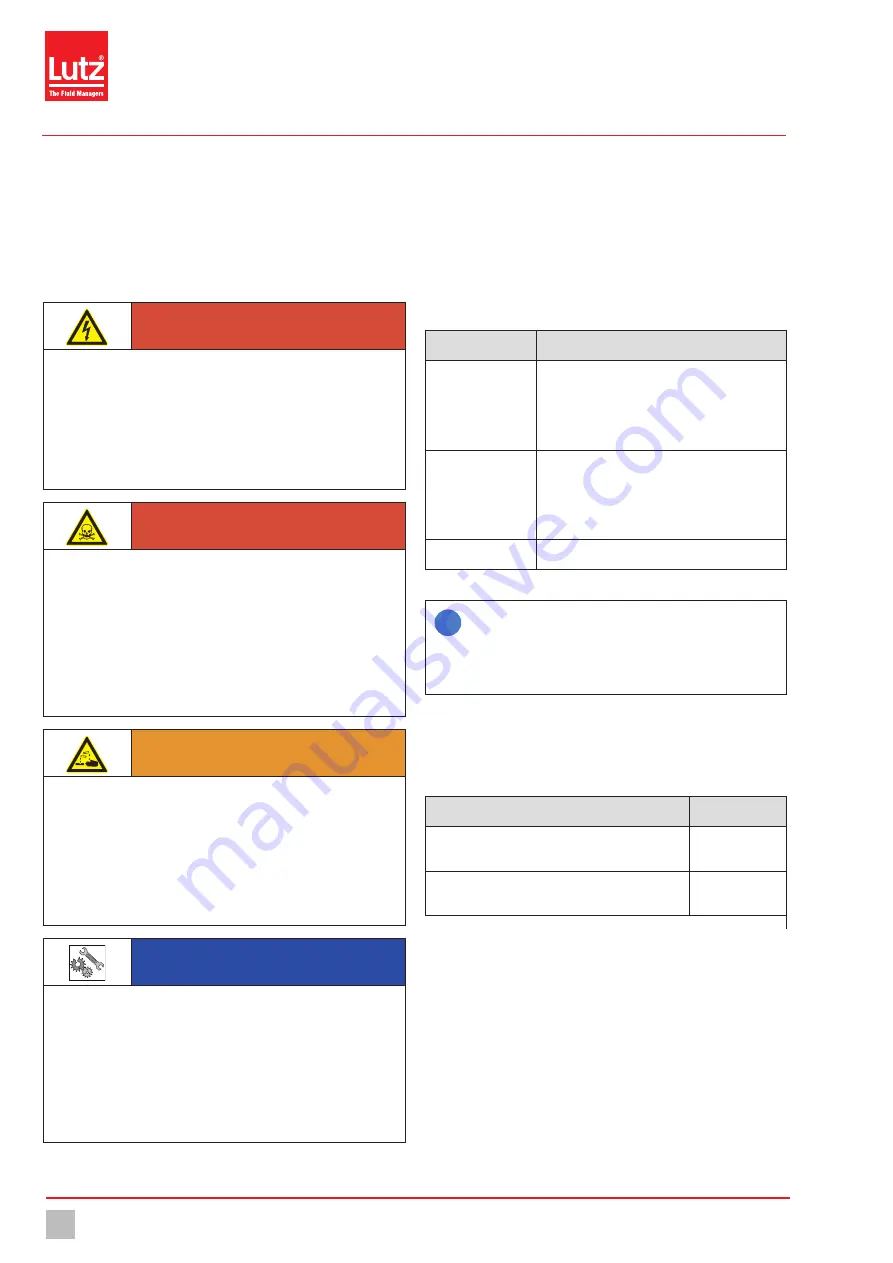
Maintenance
Maintenance intervals
28
© Lutz-Jesco GmbH 2015
BA-24721-02-V01
Chlorine gas changeover unit C 7523
Operating instructions
12 Maintenance
Products by Lutz-Jesco are manufactured to the highest quality
standards and have a long service life. However, some parts are subject
to operational wear. This means that regular visual inspections are
necessary to ensure a long operating life. Regular maintenance will
protect the device from operation interruptions.
DANGER!
Mortal danger from electric shock!
Live parts can inflict fatal injuries.
ð
Before carrying out any maintenance work, always disconnect the
device from the power supply.
ð
Secure the system to prevent it from being switched on by
accident.
DANGER!
Danger to life from chlorine poisoning!
Do not carry out maintenance or any other work on the chlorinator
until the system has been decommissioned and all of the chlorine gas
has been removed from the lines. The failure to follow this instruction
presents a significant risk of injury.
ð
Prior to any maintenance work, prepare the system in accordance
with section 12.3 „Preparing the system for maintenance“ on page
28.
WARNING!!
Increased risk of accidents due to insufficient qualifica-
tion of personnel!
Chlorinators and their accessories must only be installed, operated
and maintained by personnel with sufficient qualifications. Insufficient
qualification will increase the risk of accidents.
ð
Ensure that all action is taken only by personnel with sufficient and
corresponding qualifications.
Note
Damage to the system due to corrosion
Water in chlorine carrying system components combines with chlorine
to form hydrochloric acid and leads to corrosion
ð
After maintenance work is complete, remove all water residues
from the system before placing it into operation.
ð
Keep the connection of the contact vacuum meter closed so that
humidity cannot penetrate
12.1 Maintenance intervals
To avoid hazardous incidents, chlorinators must be regularly maintained.
This table gives you an overview of maintenance work and the intervals
at which you must carry it out. The next few sections provide instructions
for carrying out this work.
Interval
Maintenance
After 1 year
Minor maintenance:
n
Clean the device.
n
Change the connection seals
n
Functional control
After 3 years
Major maintenance:
n
Clean the device.
n
Replace all elastomers
n
Functional control
After 5 years
n
Replace the contact gauge
Table 25: Maintenance intervals
i
In some cases, regional regulations may require shorter
maintenance intervals. Maintenance intervals depend only on
how frequently the equipment is used. Chemical wear of
rubber parts, for example, begins with the initial medium
contact and continues irrespective of the usage.
Maintenance sets are listed in chapter 14 „Spare parts“ on page 32.
12.2 Maintenance accessories
Description
Part number
Silicone grease, medium viscosity 35 g
for application to seals
35537
Plastic tools
for dismantling O-rings
W00133
Table 26: Maintenance accessories
12.3 Preparing the system for maintenance
Perform the following working steps:
1.
Close the chlorine tank valves.
2.
Use the injector to suck off the remaining chlorine.
3.
Run the chlorinator for approximately five minutes with nitrogen or
dry compressed air.
4.
Switch off the injector.
ü
The system is prepared for maintenance.