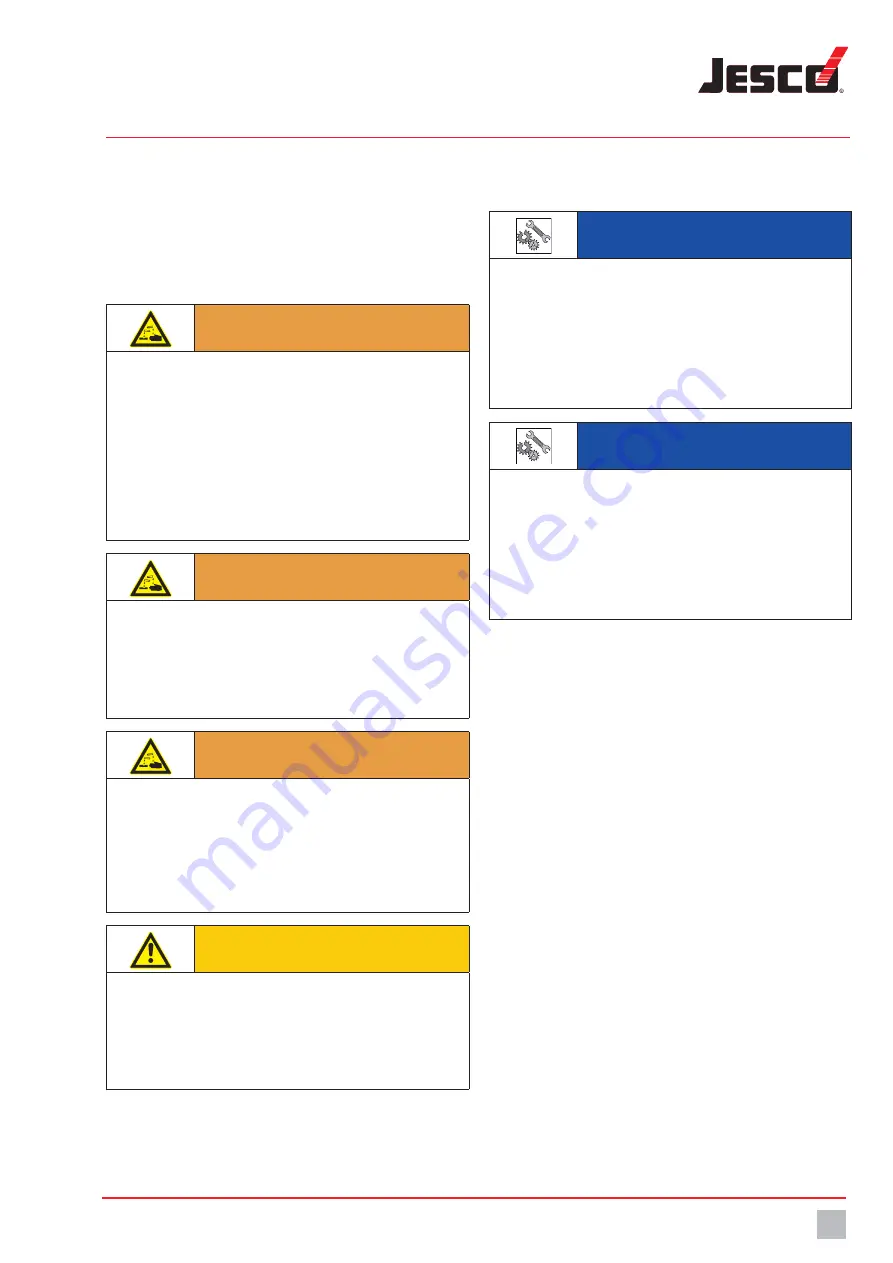
Hydraulic installation
Design of the system
19
© Lutz-Jesco GmbH 2014
Subject to technical changes.
140725
BA-10103-02-V01
Stepper Motor-driven Diaphragm Dosing Pump
MEMDOS SMART LK
Operating instructions
8 Hydraulic installation
In this chapter, you will fi nd information about the hydraulic parts of a
system that you should install or that can install additionally. In many
cases, you must install hydraulic accessories to be able to use all the
functions that the MEMDOS SMART LK dosing pump offers, to guarantee
functional safety or to achieve a high level of dosing precision.
WARNING
Caustic burns or other burns through dosing media!
The materials of the dosing pump and hydraulic parts of the system
must be suitable for the dosing medium that is used. Should this not
be the case, the dosing media may leak. Depending on the type and
hazardousness of the dosing medium, this can result in injury.
Make sure that the materials you are using are suitable for the
dosing medium.
Make sure that the lubricants, adhesives, sealants, etc. that you
use are suitable for the dosing medium.
WARNING
Caustic burns or other burns through dosing media!
If there is a diaphragm rupture, the dosing medium can escape in an
uncontrolled way. Depending on the type and hazardousness of the
dosing medium, this can result in injury.
Install a leakage drain.
WARNING
Caustic burns or other burns through dosing media!
The dosing pump can generate a pressure that is many times the
rated one. A blocked pressure line can lead to dosing medium
escaping. Depending on the type and hazardousness of the dosing
medium, this can result in injury.
Install pressure relief valves.
CAUTION
Danger of personal injury and material damage!
High peak pressures can lead to piping vibrating and cause them to
snap. This can result in injury due to uncontrollable piping or escaping
dosing media.
Install pulsation dampeners.
NOTICE
Damage to drives due to overloading
The pressure conditions between the suction and discharge sides
must be balanced; otherwise, overloading can result. This can lead to
uncontrolled dosing processes, damage to the plant pipework and to
the dosing pump.
Ensure that the pressure on the discharge side is at least 1 bar
greater than on the suction side.
NOTICE
Locking of threads
Stainless steel and plastic parts (particularly those made of PVC) that
are bolted together in a detachable connection (e.g. the dosing head
and the valves) can lock. This makes them diffi cult to release.
Before bolting, grease the corresponding parts with a lubricant,
e.g. PTFE spray). Ensure that the lubricant is compatible with the
dosing medium.
8.1 Design of the system
The dosing pump's technical data (see chapter 5 „Technical
specifi cations“ on page 14) must be taken into account and the
plant's layout must be set up appropriately (e.g. pressure loss when
rating the lines with regard to their nominal diameter and length).
You must design the entire plant and its integrated dosing pump such
that escaping dosing medium due to the failure of wearing parts such
as the diaphragm, or to burst hoses does not lead to permanent
damage to parts of the system or the premises.
The leakage opening of the dosing head must be visible so that you
can detect a diaphragm rupture. It must be possible for the outfl ow
from the leakage drain to be on a free downwards gradient.
If you use hazardous dosing media, the installation must be designed
such that no disproportionately high consequential damages arise
due to dosing media escaping.
To avoid dosing errors after the end of the process, the dosing pump
must be locked hydraulically.
To allow you to easily inspect the pressure conditions in the system,
you should provide connections for pressure gauges close to the
suction and discharge valves.