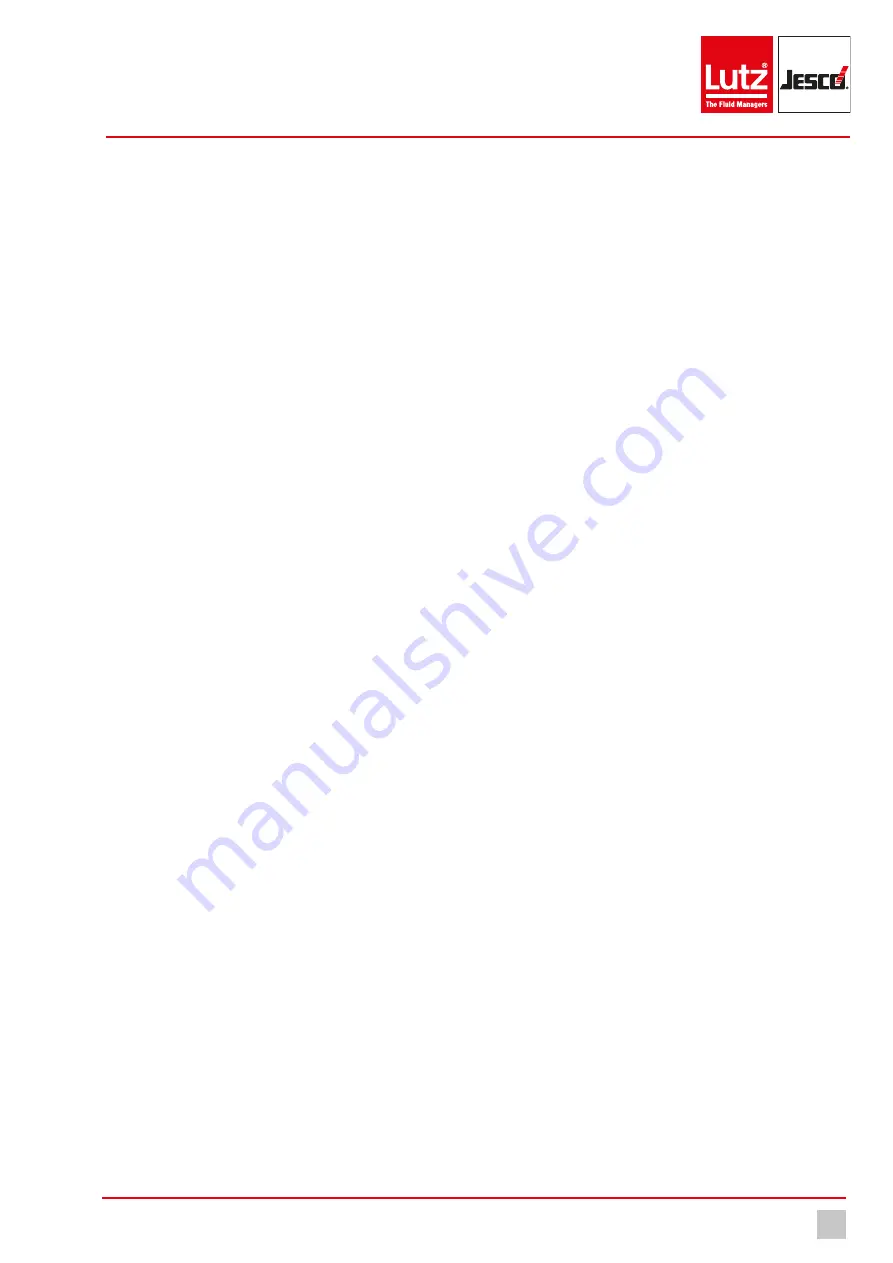
Intended use
Foreseeable misuse
9
© Lutz-Jesco GmbH 2018
Subject to technical changes.
181112
BA-10407-02-V08
Motor-driven diaphragm dosing pump
MEMDOS LB
Operating instructions
3.7 Foreseeable misuse
Below, there is information about the applications of the dosing pump or
associated equipment that are not considered to be intended use. This
section is intended to allow you to detect possible misuse in advance and
to avoid it.
Foreseeable misuse is assigned to the individual stages of the product
lifetime:
3.7.1 Incorrect assembly
n
Unstable or unsuitable bracket
n
Dosing pump bolted wrongly or loosely
3.7.2 Incorrect hydraulic installation
n
Suction and pressure lines dimensioned incorrectly
n
Unsuitable connection of the pipes due to wrong material or unsuita-
ble connections.
n
Suction and pressure lines mixed-up
n
Damage to threads due to them being tightened too much
n
Bending of pipelines
n
No free return flow of the pressure relief valve
n
Excessive demand due to the pressure differences between the suc-
tion and pressure valves
n
Through-suction at installation without back-pressure valves
n
Damage due to undamped acceleration mass forces
n
Exceeding the admissible pressure on the suction and discharge sides
n
Using damaged parts
3.7.3 Incorrect electrical installation
n
Connecting the mains voltage without a protective earth
n
Unsecured mains or one that does not conform to standards
n
Not possible to immediately or easily disconnect the power supply
n
Wrong connecting cables for mains voltage
n
Dosing pump accessories connected to wrong sockets
n
Diaphragm monitoring not connected or defective
n
Protective earth removed
3.7.4 Incorrect start-up
n
Start-up with damaged system
n
Shut-off valves closed at commissioning
n
Closed suction or pressure line, e.g. due to blockages
n
Personnel was not informed before the start-up
n
System was recommissioned after maintenance without all the pro-
tective equipment and fixtures, etc. being reconnected.
n
Inadequate protective clothing or none at all
3.7.5 Incorrect operation
n
Protective equipment not functioning correctly or dismantled
n
Modification of the dosing pump without authority
n
Ignoring operational disturbances
n
Elimination of operational disturbances by personnel without ade-
quate qualifications
n
Deposits in the dosing head due to inadequate purging, particularly
with suspensions
n
Bridging the external fuse
n
Operation made more difficult due to inadequate lighting or machines
that are difficult to access
n
Operation not possible due to dirty or illegible display of the dosing
pump
n
Delivery of dosing media for which the system is not designed
n
Delivery of particulate or contaminated dosing media
n
Inadequate protective clothing or none at all
3.7.6 Incorrect maintenance
n
Carrying out maintenance during ongoing operation
n
Carrying out work that is not described in the operating manual
n
No adequate or regular inspection of correct functioning
n
No replacement of damaged parts or cables with inadequate insula-
tion
n
No securing against reactivation during maintenance work
n
Using cleaning materials that can cause reactions with the dosing
media
n
Inadequate cleaning of the system
n
Unsuitable purging medium
n
Unsuitable cleaning materials
n
Detergents left in system parts
n
Using unsuitable cleaning equipment
n
Using the wrong spares or lubricants
n
Contaminating the dosing medium with lubricant
n
Installing spare parts without following the instructions in the operat-
ing manual
n
Blocking venting orifices
n
Pulling off sections of the plant
n
Contamination at installation without a dirt trap
n
Mixing up the valves
n
Mixing up the sensor lines
n
Not reconnecting all the lines
n
Damaging or not installing all the seals
n
Not renewing seals
n
Not paying attention to safety data sheets
n
Inadequate protective clothing or none at all
3.7.7 Incorrect decommissioning
n
Not completely removing the dosing medium
n
Dismantling lines while the dosing pump is running
n
Device not disconnected from the power supply
n
Using the wrong dismantling tools
n
Inadequate protective clothing or none at all
3.7.8 Incorrect disposal
n
Incorrect disposal of dosing media, operating resources and other
materials
n
No labelling of hazardous substances