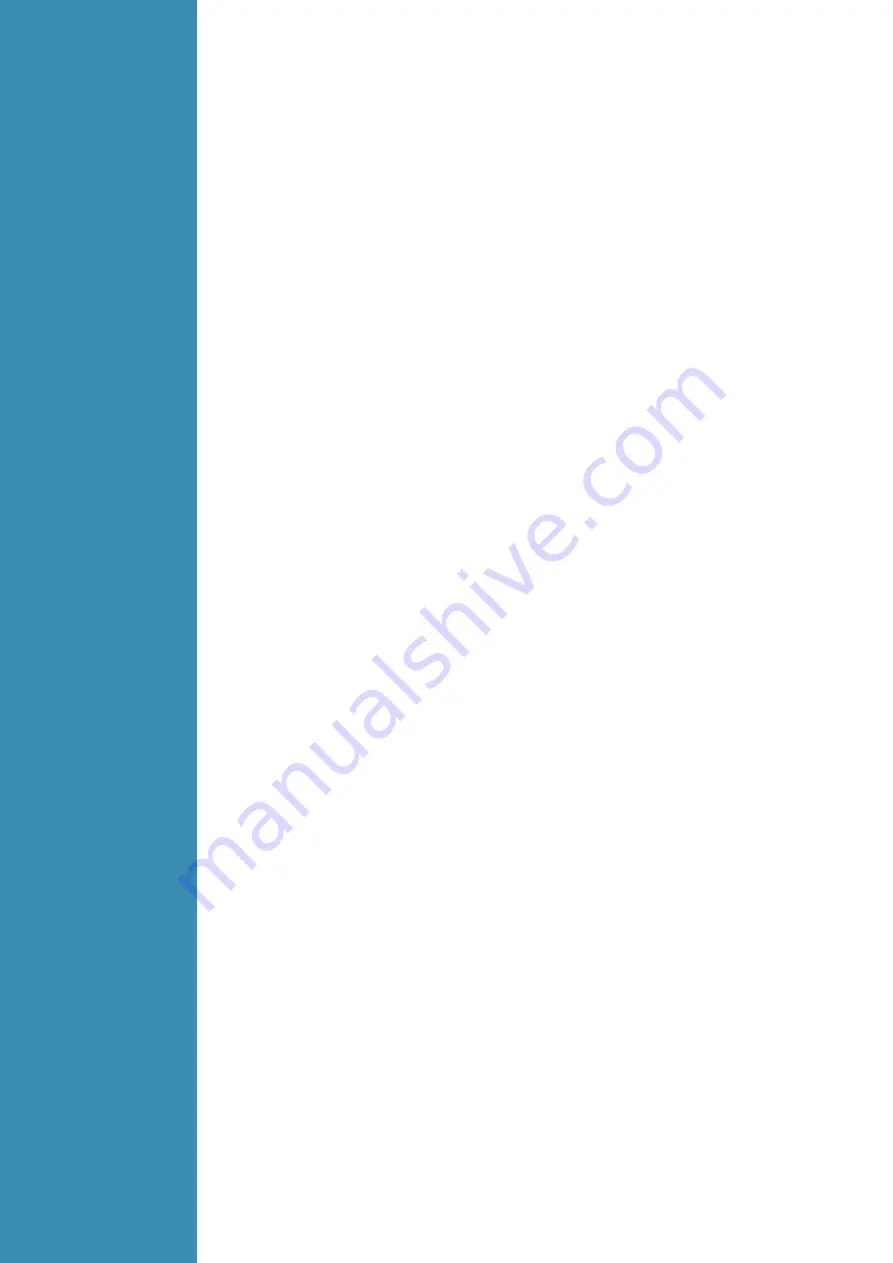
IMPORTANT
: Read this OPERATOR MANUAL together
with PRESCRIPTION AND COMPLIANCE MANUAL before
to use this equipment. In case of loss one of two parts
contact immediately your dealer.
Allow the operator to consult this manual.
Pulse frequency setting indicator (10)
Only available when pulse mode (12) is selected. Sets the rate that the welding output alternates between the
peak and base current settings. Unit(Hz) and setting range (0.5-200Hz).
Pulse mode ‘off’ indicator (11)
Pulse mode ‘On’ indicator (12)
Pulse welding
Pulse welding mode switches the welding output between a high and low current output in a cyclical manner.
When used correctly this function has substantial benefits in the TIG welding process including greater weld
penetration for less work heat input and greater control of the weld pool. The basic theory for setting the base
current using pulse mode is that the base current should be sufficient to maintain the existing molten weld pool,
while the peak current is sufficient to melt new metal in order to move/ expand the molten weld pool. Increased
pulse frequency will have the effect of making the arc more tightly focused which is useful for fine stainless work
and similar. Pulsing can also be used to help move the weld pool, this technique is useful for welding out of
position or with materials that have higher viscosity weld pool. Higher pulse duty setting will give greater heat
input, while lower pulse duty will have the opposite effect.
MMA parameter settings
Hot start (25)
Hot start provides extra power when the weld starts to counteract the high resistance of the electrode and
workpiece as the arc is started. setting range (0-10).
Arc force (23)
An MMA welding power source is designed to produce constant output current (CC).This means with different
types of electrode and arc length; the welding voltage varies to keep the current constant. This can cause
instability in some welding conditions as MMA welding electrodes will have a minimum voltage they can
operate with and still have a stable arc. Arc Force control boosts the welding power if its senses the welding
voltage is getting too low. The higher the arc force adjustment, the higher the minimum voltage that the power
source will allow. This effect will also cause the welding current to increase. 0 is Arc Force off, 10 is maximum Arc
Force. This is practically useful for electrode types that have a higher operating voltage requirement or joint types
that require a short arc length such as out of position welds.
Water / Air Cooling Selection Button (28)
When using the integrated water cooling system with a water cooled torch, select the ‘water’ option (26).
This will activate the water cooler power (the water cooler must also be switched on the rear panel) and the
water cooling protection system. If using air cooled torch, select ‘Air’ option (27). Note the welding machine
comes standard with a water cooled torch system. Operating a water cooled torch without water cooling will
quickly cause serious damage to the torch. Damage to torch or components due to lack of water is not
covered under machine warranty.
Alarm Indicator (29)
Lights when over voltage, over current, input phase loss or electrical overheating (due to exceeding duty c
ycle) is detected and protection is activated. When protection is activated, welding output will be disabled
until the safety system senses the overload has reduced sufficiently and indicator lamp goes out. May also
trigger if machine experiences an internal power circuit failure.
Water Cooling System Error Indicator (30)
When using the integrated water cooler, the system is equipped with a pressure sensor. If the coolant pressure is
insufficient, this indicator will light and the welding output will not be able to be active, in order to protect the
torch and cooling system.
3.2
Power
supply
input
connection
GRAND TIG 250 DC PULSE is designed to operate on a 380V AC power supply.
When the power supply voltage is over the safe work voltage, there are over voltage and under
voltage protection inside the welder, the alarm light will on, at the same time, the current output will
be cut off. If the power supply voltage continually goes beyond the safe work voltage range, it will
shorten the welder life-span. The below measures can be used:
� Change the power supply input net. Such as, connect the welder with the stable power supply
voltage of distributor;
� Induce the machines using power supply in the same time;
� Set the voltage stabilization device in the front of power cable input.
Содержание GRAND TIG 250 DC PULSE
Страница 22: ...4 4 Electrical schematic drawing ...