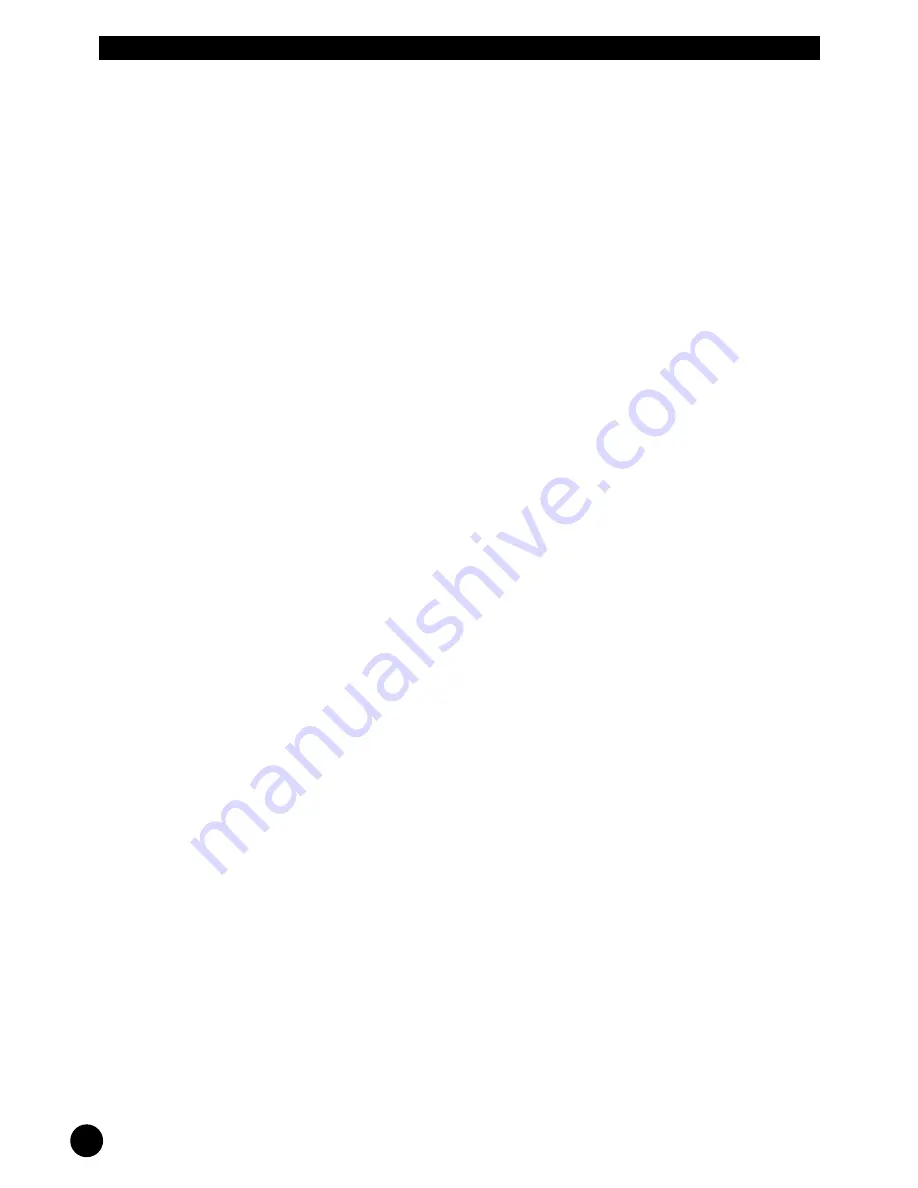
6
Electronic control - Comments
Electric system
Comments:
1.
Maximum speed
Governs the power directed to the motor in % of maximum power.
This leads to a given wheel speed depending on load. 100% is 6 km/h, with no
load and on a flat surface.
2.
1st reduced power
Governs the reduced effect sent to the motor. Is not functional when the value
is 100%.
This function can be used to set an extra top speed (lower than true top speed)
selected and deselected by a switch. When the switch is open the top speed is
reduced. When the switch is closed the top speed is equal to the maximum
speed as above. The switch must be connected to the positive pin and pin 14 of
the 15-pin socket (see circuit diagram). The speed available is not proportional
to the power used, e.g. 34% is approximately 3 km/h with no load. This
parameter is used on SELF to reduce the maximum speed to 3 km/h when the
forks are raised higher than 50 cm.
3.
2nd reduced speed
Not used.
4.
Minimum power
The power the truck starts with when the drive grip is turned.
5.
Safety forward power
The maximum power sent to the motor when the safety switch is activated.
Acceleration is the same as normal operation (see point 7).
6.
Maximum power
The maximum power sent to the motor upon starting. A reduction of this will
give less tractive power.
7.
Acceleration slope
The time difference from no power to full power when the drive grip is turned
full extent.
8.
Maximum temperature
The maximum internal temperature of the controller. If this value is reached
the controller will shut down. After a short cooling period operations may be
resumed.
9.
Safety forward time
The time the vehicle can drive (forwards) when the safety switch is activated.
10.
Battery 90%
The voltage of the battery when 90% charged. The controller loads the battery
and measures in fractions of a second when the truck starts to move.
11.
Battery 70%
As above.
12.
Battery 50%
As above.
13.
Battery 25%
As above.
14.
Battery 15%
As above.
15.
Battery charg. voltage
When this voltage is exceeded, the counter “No. of charges” increases by one
(see point 20). At the same time, the “subtotal counter“ is zeroed (see point 19).
16.
A/D start voltage
The voltage given by the Hall effect units to start moving.
Содержание LOGIFLEX SELF 1001
Страница 2: ......
Страница 14: ...www logitrans com www www logitrans com S928 10 02 2010...