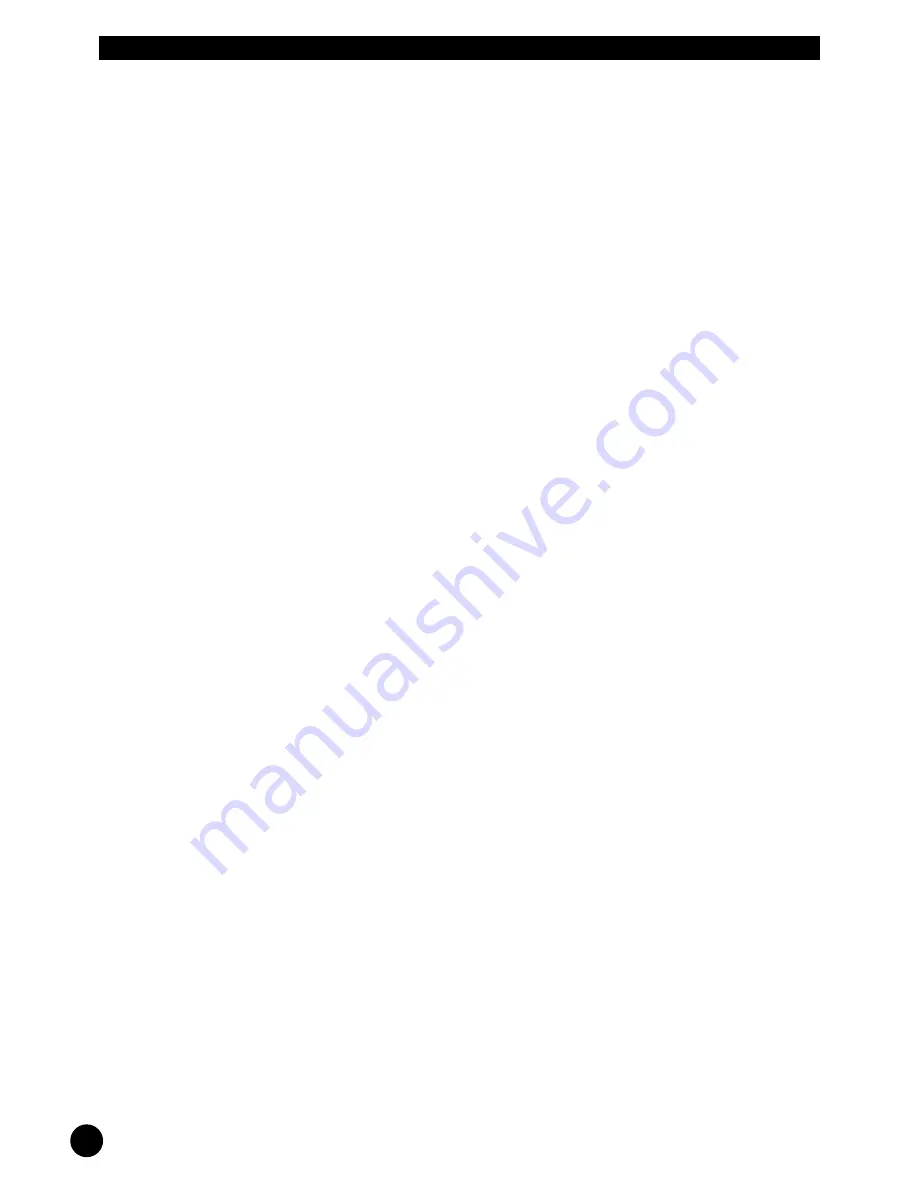
12
Drive motor
Maintenance
Drive motor
Wheel bandage
It is recommended that the wheel bandage is replaced when it is worn down to less than 5 mm
thickness.
Wheel bandage replacement
- Remove motor cables. Note their position - they must be refitted exactly the same.
- Remove the M5 screws which secure the wheel bandage.
- Screw 3 M6 screws into the threaded holes to extract wheel.
- Fit new wheel bandage and O-ring so that the two dowels match the holes.
- Carefully strike the wheel bandage into position and screw in the screws.
- Tighten the screws.
- Fit cables - in the same position as before!
Brake
- see drawing on page 13.
- To regulate the braking torque resulting from daily operation, turn screw D.
- Periodically, check clearance C. When it is more than 0.7 mm the brake needs adjustment thus:
- Loosen 3 screws
A
- Adjust 3 screws
B
until C is 0.2 mm
- Tighten screws
A
while holding screws
B
- Check clearance
C
- When the brake lining has worn to less than 5 mm (E) it must be replaced.
- Under all circumstances, replace the brake lining after 500 hours of operation.
- Check the resistance in the brake coil (especially if the brake is not working):
The resistance between the two leads must be about 25 ohm.
If not, the brake must be replaced.
Brushes
- Check the brushes after 250 hours of operation. New brushes are 20 mm long and when more than
half this length is worn away, the carbons should be replaced. In any event they should be replaced
after 500 hours of operation.
Lubrication
NOTE:
- Normally, grease need not be replenished. Only when the truck has been operating in very warm
surroundings, replenishment becomes necessary.
- Grease must be replaced after two years, or not later than after 1000 hours of operation.
- The recommended type of grease is AGIP GR MU/EP1.
Содержание LOGIFLEX SELF 1001
Страница 2: ......
Страница 14: ...www logitrans com www www logitrans com S928 10 02 2010...