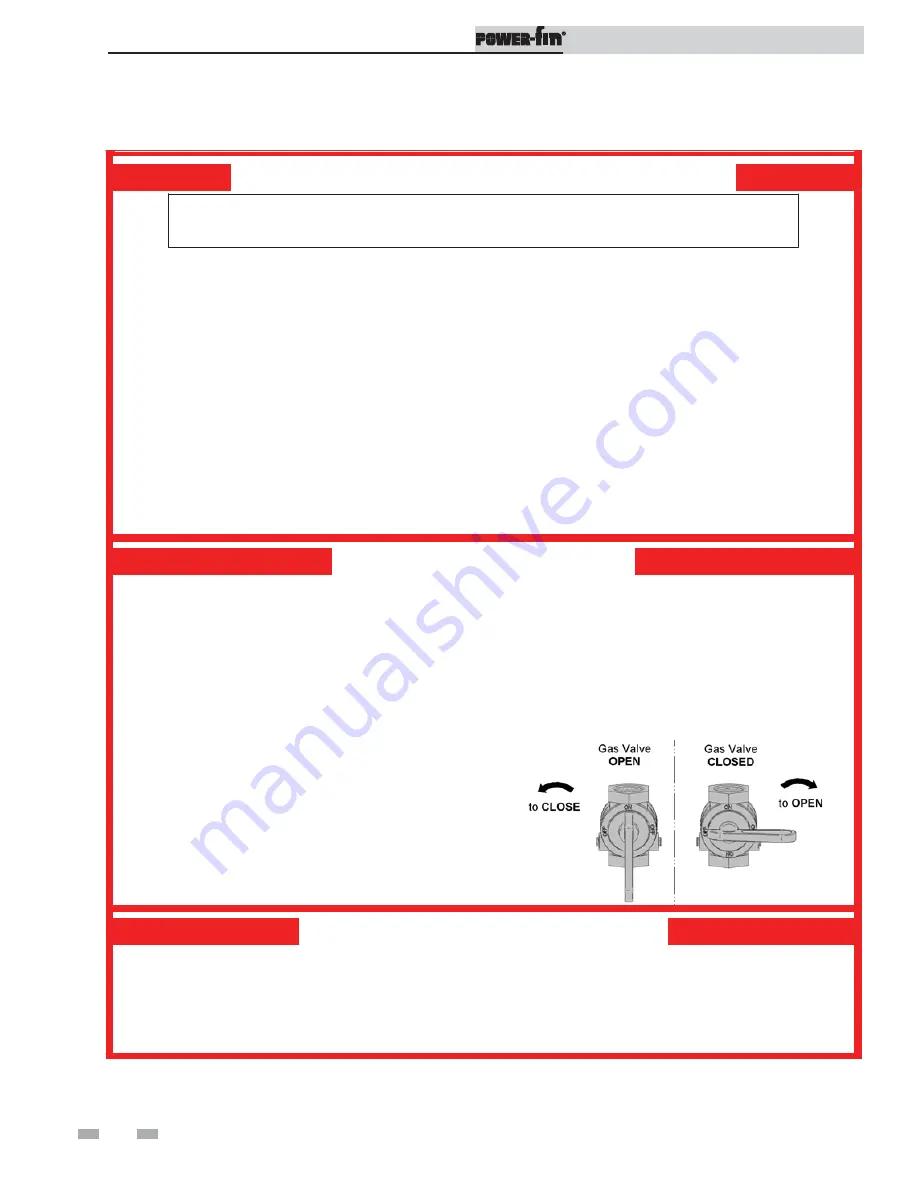
46
Installation & Operation Manual
Figure 9-2_Operating Instructions
9
Start-up
FOR YOUR SAFETY READ BEFORE OPERATING
WARNING:
If you do not follow these instructions exactly, a fire or explosion
may result causing property damage, personal injury, or loss of life.
A. This appliance does not have a pilot. It is
equipped with an ignition device which
automatically lights the burner. Do not try
to light the burner by hand.
B. BEFORE OPERATING smell all around
the appliance area for gas. Be sure to
smell next to the floor because some gas
is heavier than air and will settle on the
floor.
WHAT TO DO IF YOU SMELL GAS
•
Do not try to light any appliance.
•
Do not touch any electric switch; do
not use any phone in your building.
•
Immediately call your gas supplier from a
neighbor’s phone. Follow the gas supplier’s
instructions.
•
If you cannot reach your gas supplier, call
the fire department.
C. Use only your hand to turn the gas control knob.
Never use tools. If the handle will not turn by
hand, don’t try to repair it, call a qualified service
technician. Force or attempted repair may
result in a fire or explosion.
D. Do not use this appliance if any part has been
under water. Immediately call a qualified
service technician to inspect the applianc e and
to replace any part of the control system and
any gas control which has been under water.
OPERATING INSTRUCTIONS
1.
STOP!
Read the safety information
above on this label.
2. Set the thermostat to lowes t setting.
3. Turn off all electric power to the
applianc e.
4. This appliance is equipped with an
ignition device which automatically lights
the burner. Do not try to light the burner
by hand.
5. Remove
front
door.
6. Turn gas shutoff valve counterclockwise
to “OFF”. Handle will be perpendicular to
pipe. Do not force.
7. Wait five (5) minutes to clear out any gas.
If you then smell gas,
STOP!
Follow “B”
in the safety information above this label.
If you don’t smell gas, go to next step.
8. Turn gas shutoff valve clockwise to “ON”.
Handle will be parallel to pipe.
9. Install
front
door.
10. Turn on all electric power to applianc e.
11. Set thermostat to desired setting.
12. If the appliance will not operate, follow the
instructions “To Turn Off Gas To Appliance” and
call your service technician or gas supplier.
TO TURN OFF GAS TO APPLIANCE
1. Set the thermostat to lowes t setting.
2. Turn off all electric power to the appliance
if service is to be performed.
3. Remove
front
door.
4. Turn gas shut off valve counterclockwise to
“OFF”. Handle will be perpendicular to pipe.
Do not force.
5. Install
front
door.
L BL2 005 3 REV B