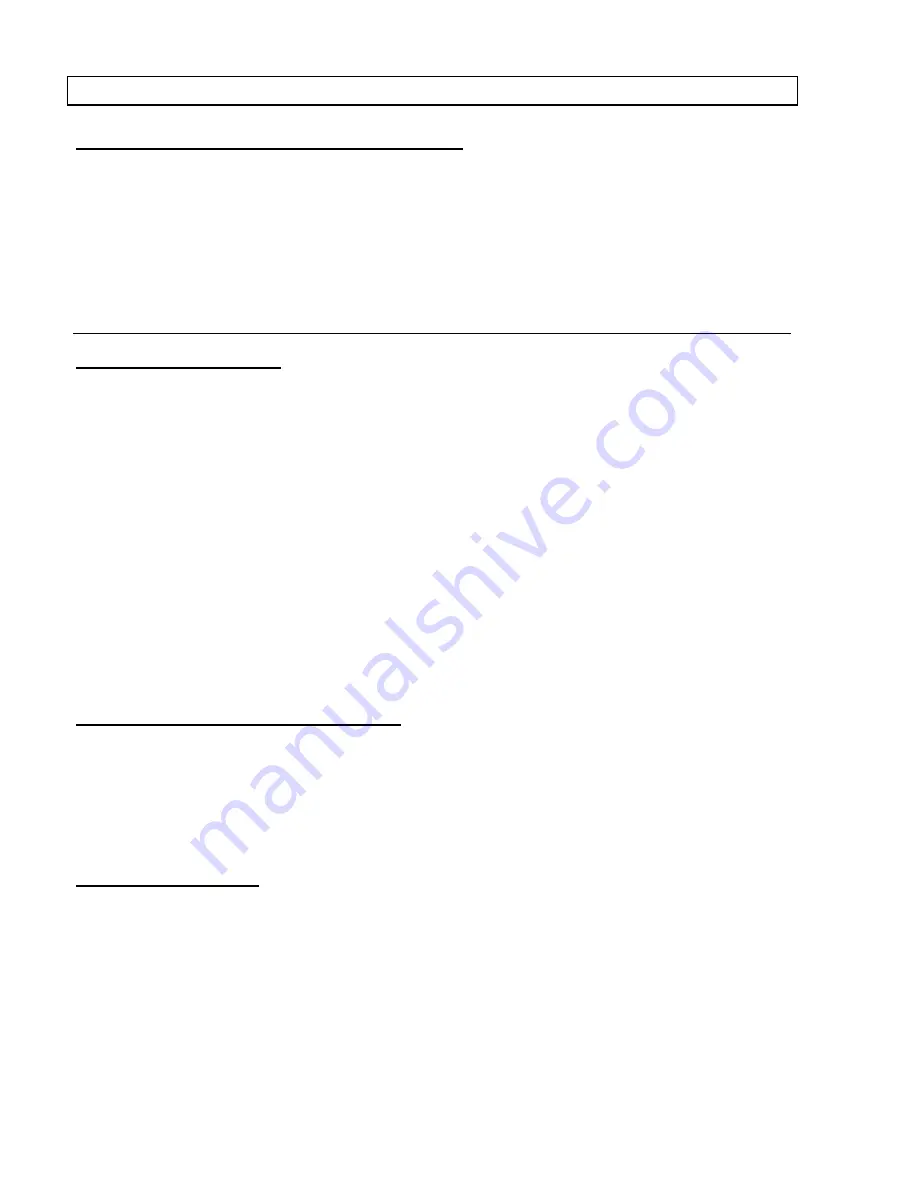
12
4.7 Additional Notes on Installation
The following should be completed on installation:
Located and Aligned
Anchored to the floor
Electrical power connected – check blower rotation
Main Air connected
Interface connected and tested
All Jog functions checked on Blaze Air
Blower motor rotation verified
Final installation suggestions:
Inching the Lathe Spindle:
It is recommended that in operation, the lathe should slowly rotate the spindle during the unload
cycle. By slowly rotating the spindle, it will ‘break’ loose any burs that can get caught on the
chuck / collet and generally will make the unload cycle faster.
The best method to enable the spindle rotation is to hardwire a connection that forces the lathe
spindle to inch. A separate Inching output is provided from the Blaze Air that is energized during
the unload cycle. This will ensure that the lathe spindle will rotate at the inching speed. If this
inching option is not available on the lathe, a slow speed should be programmed during the unload
cycle (less than 50 Rpms). If a programming mistake is made and the spindle rotates at a faster
speed, there may be damage to the back end of the spindle liner and the front end of the Blaze Air
Vacuum Tube. The damage will occur because these two parts contact each other during the
unload cycle (they have mating chamfers to align the tubes). This contact is designed to be enough
to seal any vacuum leaks, but not too much to cause the parts to damage each other when the
spindle liner inches and the Vacuum Liner does not rotate. (See
Section 7.2: Valve Descriptions
& Settings
on setting the contact pressure).
Documenting the Interface & Parameters:
Once the interface has been fully tested, mark up any wiring changes on the Interface Schematic at
the end of this manual. There is also a chart where all of the Setup Parameters (P0-P11) values
can be documented. Once the interface is fully documented, make a copy of this page and fax it to
513-851-4666 so that our records can be updated (please include machine serial number, customer
name and approximate date of installation). This will allow replacement CPUs to be pre-
programmed before shipping and also avoid repeat interface wiring mistakes.
Energy Saving Feature:
If the Lathe in Auto-Cycle interface connection is available and wired, the Blaze Air Blower can
be programmed to only be ON when the lathe is running a program. If there are no faults and the
Blaze Air is enabled to run, it will continue to be in the run state, but the blower will only run
when the Lathe is running the part program.
See Section 5.6: Menu: Setup Parameters
/
P5:
Blower Control
on how to enable this programmable option.
Содержание Blaze Air
Страница 42: ...12 COMPONENT LOCATION DRAWINGS 12 1 6104 General Assembly Floor Plan 41...
Страница 44: ...13 2 6104 A Base Assembly Drawings 3 Sheets 43...
Страница 45: ...44...
Страница 46: ...45 45...
Страница 48: ...14 2 6104 B Tube Assembly Drawings 1 Sheet 47...
Страница 51: ...17 ELECTRICAL SCHEMATICS 50...
Страница 52: ...51...
Страница 53: ...52...
Страница 54: ...17 1 Lathe Interface Schematic Generic 53...