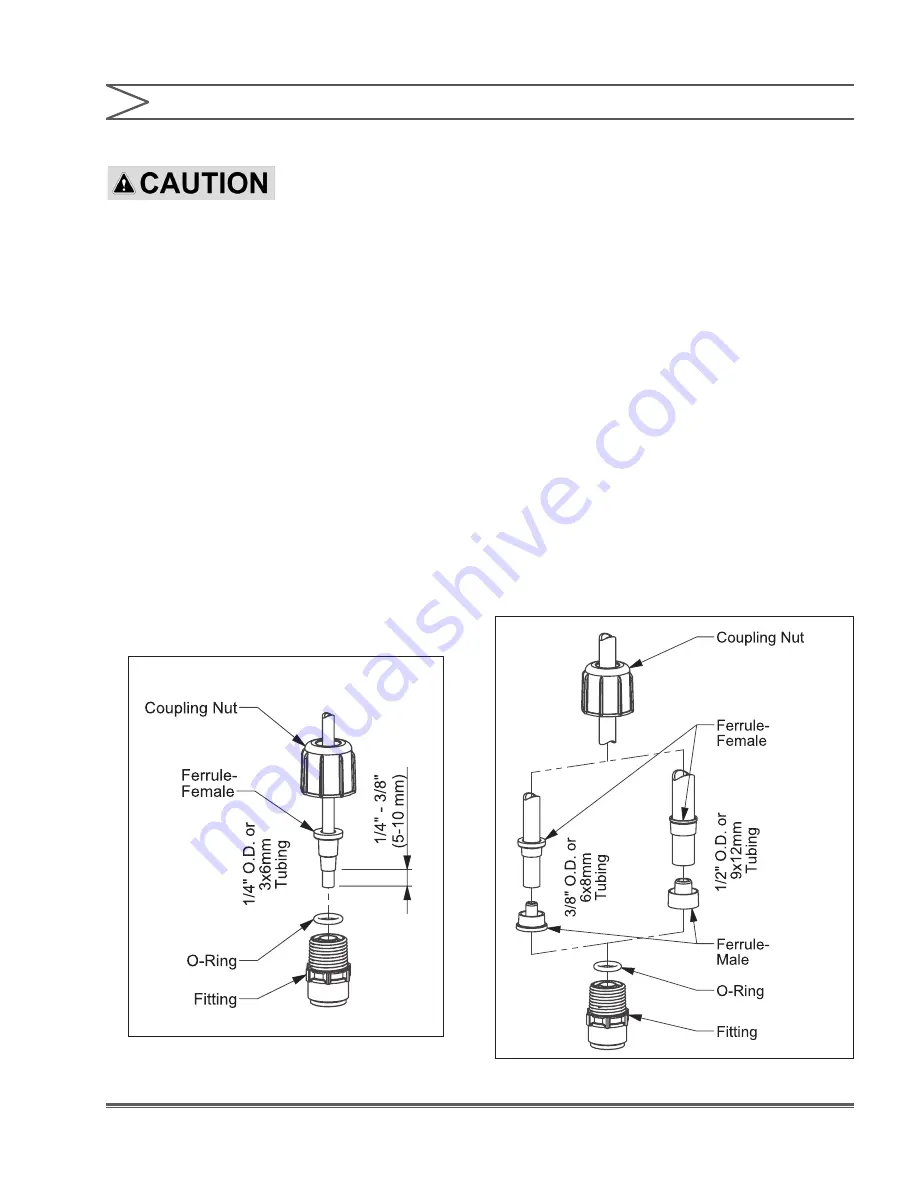
5
Instruction Manual
SECTION 2 - INSTALLATION
Figure 4a.
2.3 TUBING CONNECTIONS
A. USE ONLY LMI
®
TUBING.
B. DO NOT USE CLEAR VINYL TUBING ON THE DISCHARGE
SIDE OF THE PUMP. THE PRESSURE CREATED BY THE
PUMP CAN RUPTURE VINYL TUBING, WHICH IS ONLY FOR
CONNECTION TO THE RETURN LINE OF THE FASTPRIME™
FITTING.
C. BEFORE INSTALLATION, ALL TUBING MUST BE CUT
WITH A CLEAN SQUARE END.
D. VALVE AND HEAD CONNECTIONS FROM THE FACTORY
ARE CAPPED OR PLUGGED TO RETAIN PRE-PRIME WATER.
REMOVE AND DISCARD THESE CAPS OR PLUGS BEFORE
CONNECTING TUBING.
E. DO NOT USE PLIERS OR PIPE WRENCH ON COUPLING
NUTS OR FITTINGS.
The LMI
®
Tubing Connection System provides
a reliable system to connect your pump to
corresponding tubing sizes. To assemble tubing
onto the fitting:
1. Insert tubing through Coupling Nut-Tubing
should enter the smaller end of the Coupling Nut
first, orienting the larger opening of the Coupling
Nut toward the tubing end.
2a. For 1/4” OD tubing: Position the Female
Ferrule so that 1/4” to 3/8” (5-10 mm) of tubing
protrudes from the Female Ferrule. Orient the
raised collar of the Ferrule toward the Coupling
Nut
(reference FIGURE 4a)
.
2b. For 3/8” or 1/2” OD tubing: Position a Female
Ferrule about one inch (25 mm) from end of
tubing. Orient the raised collar of the Female
Ferrule toward the Coupling Nut. Then,
insert the Male Ferrule onto the end of the
tube, pushing the tube into the bottom of the
groove in the Male Ferrule. Then slide the
Female Ferrule down the tubing and with your
fingers, press tightly into the Male Ferrule
(reference FIGURE 4b)
.
3. Firmly hand tighten the Coupling Nut onto the
fitting.
Note:
Tightening with pliers may cause the Ferrules
to break.
Figure 4b. Tubing Connections