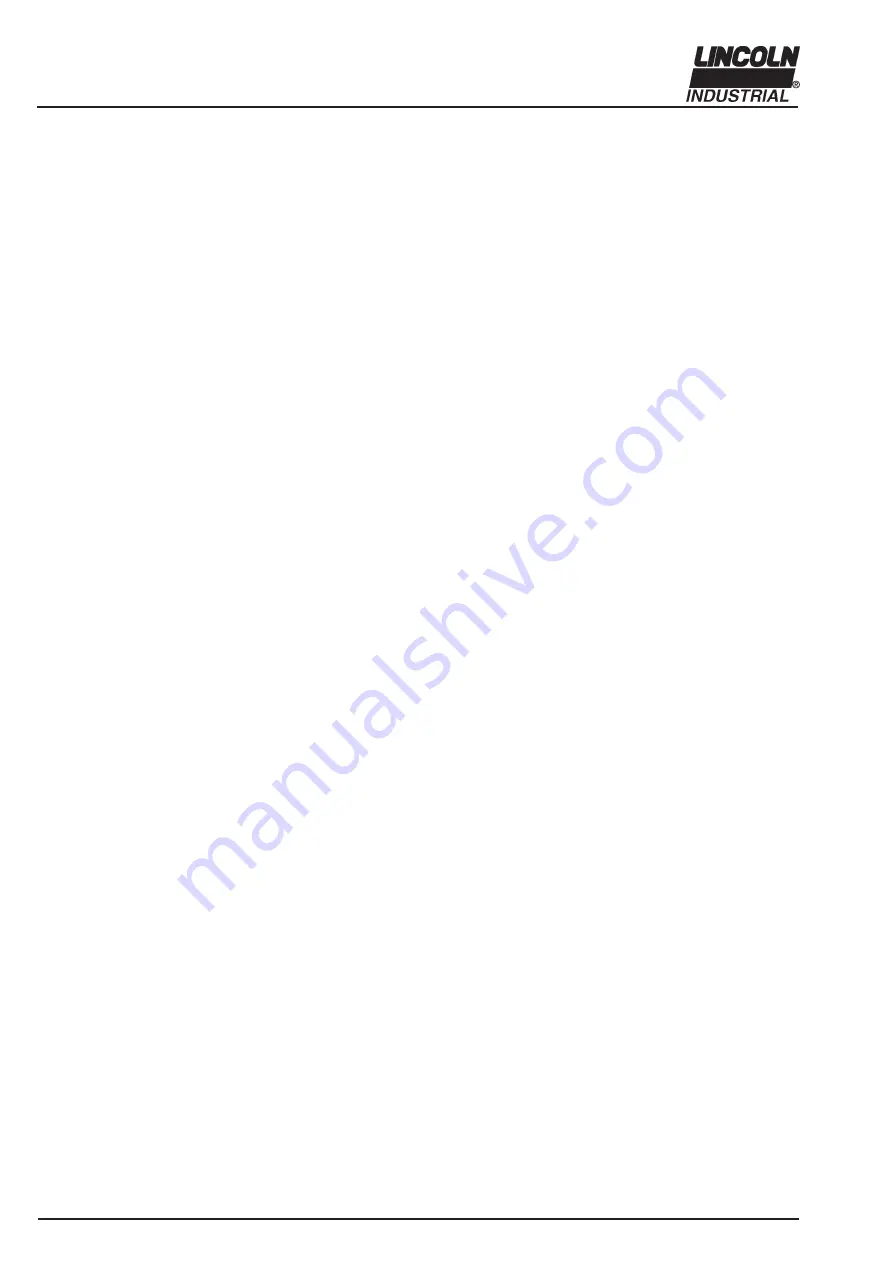
LINCOLN GmbH • Postfach 1263 • D-69183 Walldorf • Tel +49 (6227) 33-0 • Fax +49 (6227) 33-259 • Tx 466088
Page 2 from 13
Owner Manual
Technical Description
2.1A-28001-A94
Subject to modifications
Safety Instructions
The Operating Manual contains important instructions regarding
safe, proper and economical operation of the pump/system.
Keeping to these instructions will avoid risks, reduce repair costs
and down time and improve reliability and pump life. The Operating
Manual has to be completed by instructions which are part of the
existing national safety and environmental regulations. The Opera-
ting Manual must always be available on site where the pump/sy-
stem is erected.
If persons engaged with the pump operation are not fully in com-
mand of the German language, the user of the pump must see to it
that his operating staff, prior to commencement of working, is instruc-
ted of the contents of the Operating Manual, especially of all safety
instructions. Any persons engaged witrh pump operation must read
and follow the Operating Manual, e. g.
• operation including setting-up elimination of faults in the working
procedure, removal of production chips, dumping of auxiliary and
working material
• servicing ( maintenance, inspection, repair) and/or
• transportation
Notes directly fixed to the pump must be observed and kept in legible
condition.
Staff Qualification and Training
The staff responsible for operation, maintenance, inspection and
installation must be adequately qualified for these jobs. The user
must properly regulate the field responsibility and supvision of the
personnel. If the personnel has not the necessary expertise, then
they must be adequately trained and instructed. If necessary, this can
be done by the manyfacture(supplier) on behalf of the machine user.
Furthermore, the user must ensure that the contents of the Operating
Manual are fully understood by the personnel.
Hazards resulting from ignoring the safety notes
Failure to heed the safety warnings may result in equipment and
environment damage and/or personal injury. Ignoring the afety no-
tes may result in the disqualification from damage claim.
Safety instructions for user/operator
• Protection devices against accidental contact for moving parts
must not be removed from a pump in operation
• Leakages of harmful materials must be dumped wthout jeopardi-
zing human beings or environment. The requirements of the Law
must be satisfied.
• Danger caused by electric energy must be excluded (for details
refer to the applicable specifications of VDE and the local power
supply companies).
Safety instructions for maintenance, inspection and installation
services
The user make sure that all maintenance, inspection and installation
work will be executed by authorized and qualified experts who have
thoroughly read the Operating Manual.
Generally, any work on the machine must be done while the machi-
ne is out of operation. Pumps and pump units delivering harmful
materials, must be decontaminated, Immediately after completion of
the cleaning procedure, all safety and protection devices must be
reassembled. Materials harmful to the enviroment must be disposed
of in accordance with the applicable official regulations. Before put-
ting the pump/pump unti into operation all items given in the Opera-
ting Manuel must be observed.
Unauthorized modifications and spare part production
Alteration and modification of the machinenare only allowed if ag-
reed upon by the manufacture. Original spare parts andaccessory
authorized by the manufacture serve the purpose of safety. When
other parts are used, the manufacture may be released from liability
for the resulting consequences.
Application as agreed
The pump has been designed to be exclusively used in vcentralized
lubrication systems. The maximum values given in the Data Sheet
must no tbe exceeded. Any application other than the one described
above is not vovered by warranty. The product (pump/pump unit) is
not allowed to be put to operation in the European Community un-
less it has been stated that the machine in question complies with
the CE guidelines.