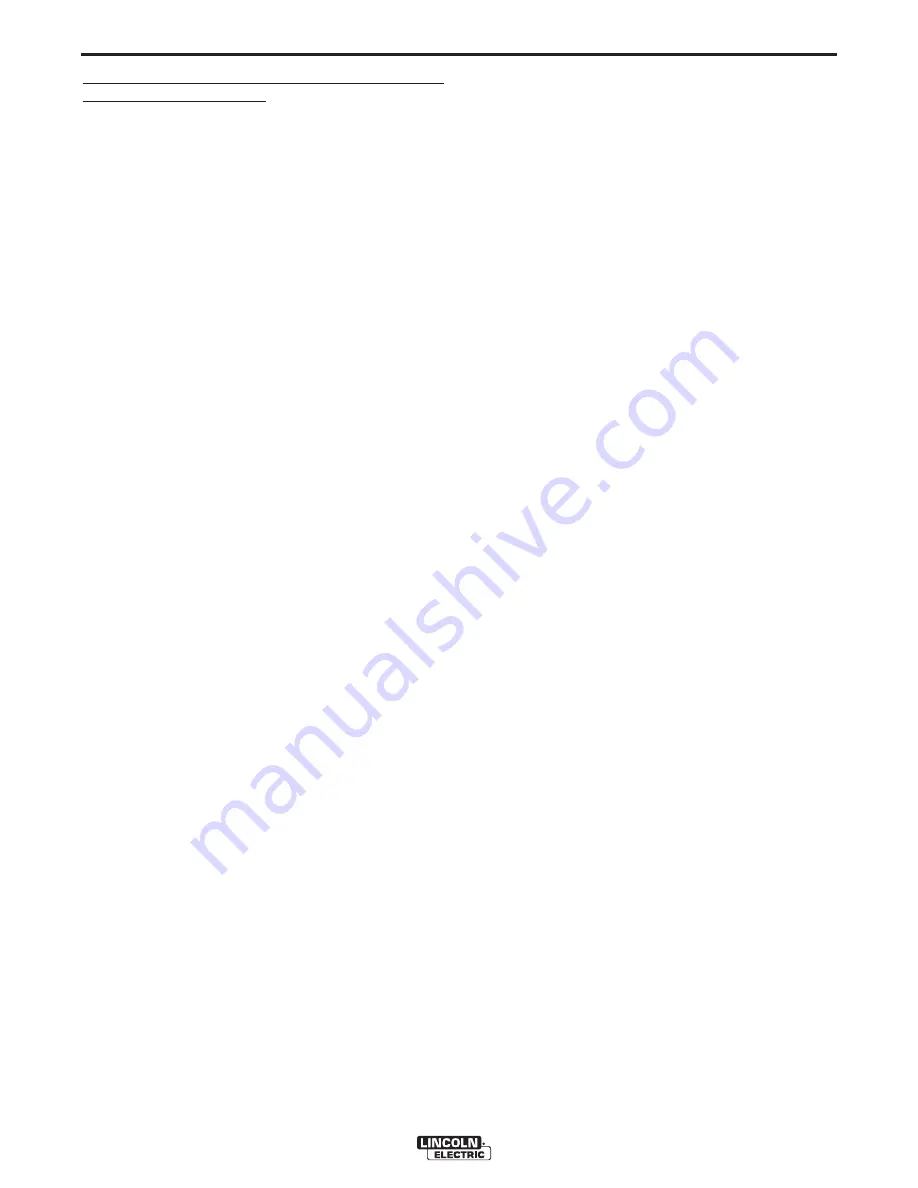
A-18
INSTALLATION
POWER WAVE
®
i400
A-18
Connections Between Power Source and Optional
DeviceNet PLC Controller
. Hard Automation applica-
tions and some earlier model controllers may require
DeviceNet connectivity to control the power source.
DeviceNet can also be used to monitor welding data,
and system status information. The optional K2780-1
DeviceNet Kit is available for this purpose. It includes
a 5 pin DeviceNet sealed mini style receptacle that
mounts on the recessed control panel of the Power
Wave i400, above the output studs. The DeviceNet
cable is keyed and polarized to prevent improper con-
nection. For best results, route DeviceNet cables
away from weld cables, wire drive control cables, or
any other current carrying device that can create a
fluctuating magnetic field. DeviceNet cables must be
sourced locally by the customer. For additional guide-
lines refer to the “DeviceNet Cable Planning and
Installation Manual” (Allen Bradley publication DN-
6.7.2).
The DeviceNet MAC ID and baud rate of the POWER
WAVE
®
i400 can be configured with the Diagnostics
Utility (included on the POWER WAVE
®
Utilities and
Service Navigator CD
ʼ
s or available at www.power-
wavesoftware.com).
OTHER SET-UP ISSUES
Selecting a Wire Drive and Setting the Wire Drive
Gear Ratio.
The POWER WAVE
®
i400 can accommo-
date a number of standard wire drives including the
AutoDrive 4R220 (default) and PF-10R. The feeder
control system must be configured for both the wire
drive type and gear ratio (high or low speed range).
This can be accomplished via the
Fanuc Teach
Pendant
(V7.30p14 or later) or with the Weld
Manager Utility (included on the Power Wave
®
Utilities
and Service Navigator CD
ʼ
s or available at www.pow-
erwavesoftware.com).
Additional information is also available in the “How To”
section at www.powerwavesoftware.com.