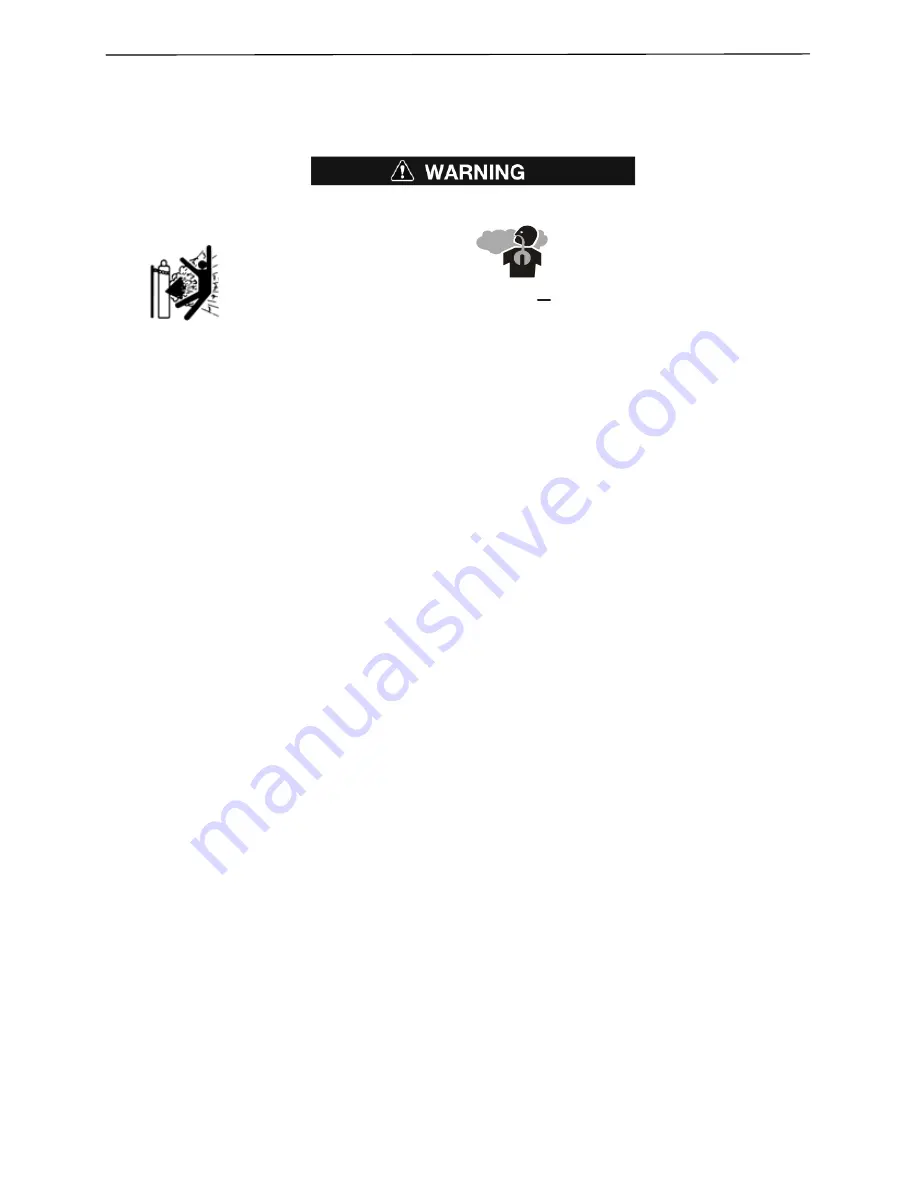
PIP
E
FAB™ WELDING SYSTEM
INSTALLATION
A-16
SHIELDING GAS CONNECTION
CYLINDER may explode if
damaged.
BUILD-UP OF SHIELDING GAS may
harm health or kill.
•
Keep cylinder upright and chained to
support.
•
Keep cylinder away from areas where it
may be damaged.
•
Never li
�
welder with cylinder a
�
ached.
•
Never allow welding electrode to touch
cylinder.
•
Keep cylinder away from welding or
other live electrical circuits.
•
Shut o
ff
shielding gas supply when not in
use.
SEE AMERICAN NATIONAL STANDARD Z-49.1, "SAFETY IN WELDING AND CUTTING" PUBLISHED
BY THE AMERICAN WELDING SOCIETY.
Maximum inlet pressure is 100 psi. (6.9 bar.)
The inlet
fi�
ng is 5/8-18 CGA type connec
�
on.
Install the shielding gas supply as follows:
1. Secure the cylinder to prevent it from falling.
2. Remove the cylinder cap. Inspect the cylinder valves and regulator for damaged threads, dirt,
dust, oil or grease. Remove dust and dirt with a clean cloth.
DO NOT ATTACH THE REGULATOR
IF OIL, GREASE OR DAMAGE IS PRESENT!
Inform your gas supplier of this condi
�
on. Oil or
grease in the presence of high pressure oxygen is explosive.
3. Stand to one side away from the outlet and open the cylinder valve for an instant. This blows
away any dust or dirt, which may have accumulated in the valve outlet.
4. A
�
ach the
fl
ow regulator to the cylinder valve and
�
ghten the union nut(s) securely with a
wrench. NOTE: If connec
�
ng to 100% CO
2
cylinder, insert regulator adapter between regulator
and cylinder valve. If adapter is equipped with a plas
�
c washer, be sure it is seated for
connec
�
on to the CO
2
cylinder.
5. A
�
ach one end of the inlet hose to the outlet
fi�
ng of the
fl
ow regulator. A
�
ach the other end
to the welding system shielding gas inlet. Using a wrench, tighten the union nuts.
6. Before opening the cylinder valve, turn the regulator adjus
�
ng knob counterclockwise un
�l
the
adjus
�
ng spring pressure is released.
7. Standing to one side, open the cylinder valve slowly a frac
�
on of a turn. When the cylinder
pressure gage stops moving, open the valve fully.
8. The
fl
ow regulator is adjustable. Adjust it to the
fl
ow rate recommended for the procedure and
process being used before making a weld.
Содержание PIPEFAB CE
Страница 18: ...PIPEFAB WELDING SYSTEM INSTALLATION A 3 FIGURE A 1 ...
Страница 97: ......