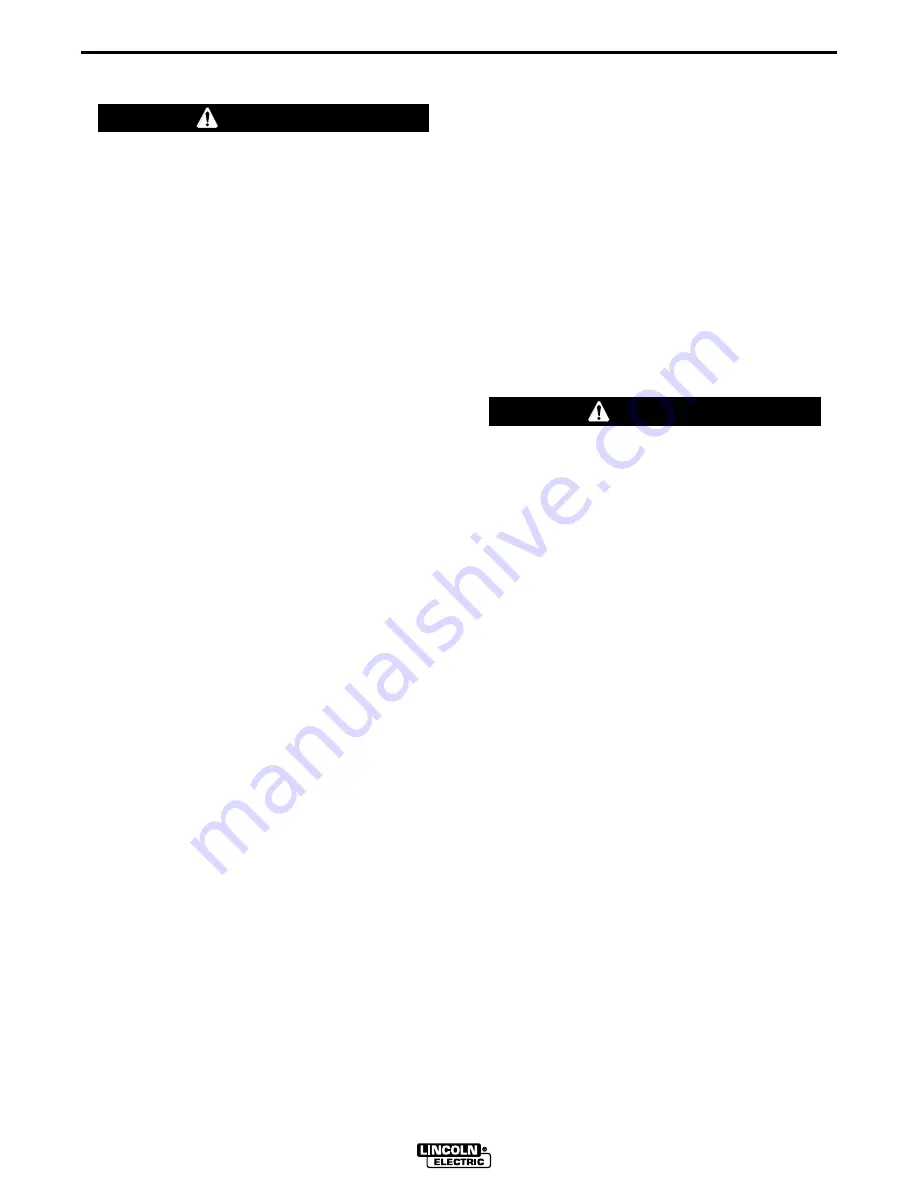
D-1
MAINTENANCE
D-1
SAFETY PRECAUTIONS
•Have a qualified technician do the maintenance
and troubleshooting work.
•Turn the engine off before working inside the
machine.
•Remove guards only when necessary and replace
them when the maintenance requiring their
removal is complete.
•Always use the greatest care when working near
moving parts.
------------------------------------------------------------------------
Read the Safety Precautions in front of this manual and
the engine instruction manual before working on this
machine.
Keep all equipment safety guards, covers and devices
in position and in good repair. Keep hands, hair, cloth-
ing and tools away from V-belts, gears, fans and all
other moving parts when starting, operating or repair-
ing the equipment.
ROUTINE AND PERIODIC
MAINTENANCE
DAILY
a. Check the crankcase oil level .
b. Refill the fuel tank to minimize moisture condensa-
tion in the tank.
c. Open the water drain valve located on the bottom of
the water separator element 1 or 2 turns and allow to
drain into a container suitable for diesel fuel for 2 to
3 seconds. Repeat the above drainage procedure
until diesel fuel is detected in the container.
WEEKLY
Blow out the machine with low pressure air periodical-
ly. In particularly dirty locations, this may be required
once a week.
ENGINE MAINTENANCE
Refer to the “Periodic Checks” section of the Engine
Operator’s Manual for the recommended maintenance
schedule of the following:
a) Engine Oil and Filter
b) Air
Cleaner
c) Fuel Filter - and Delivery System
d) Cooling
Blower
Belt
e) Battery
f) Cooling
System
Refer to Table D.1 at the end of this section for various
engine maintenance components.
AIR FILTER
EXCESSIVE AIR FILTER RESTRICTION WILL
RESULT IN REDUCED ENGINE LIFE.
------------------------------------------------------------------------
The air filter element is a dry cartridge type. It can be
cleaned and reused; however, damaged elements
should not be reused. Stop engine after 100 hours of
running time and clean filter element , replace the fil-
ter if necessary. Service air cleaner regularly accord-
ing to Engine Operator’s Manual.
1. Locate the air filter canister located behind the
engine door on the top of the engine.
2. Remove air filter element.
3. Remove loose dirt from element with compressed
air or water hose directed from inside out.
Compressed Air: 100 psi maximum with nozzles at
least one inch away from element.
Water Hose:
40 psi maximum without nozzle.
4. Soak element in a mild detergent solution for 15 min-
utes. Do not soak more than 24 hours. Swish ele-
ment around in the solution to help remove dirt.
5. Rinse elements from inside out with a gentle stream
of water (less than 40 psi) to remove all suds and
dirt.
6.Dry element before reuse with warm air at less than
160
o
F (71
o
C). Do not use a light bulb to dry the ele-
ment.
COMMANDER 400
WARNING
CAUTION
Содержание Commander 400
Страница 44: ...F 12 NOTES F 12 COMMANDER 400...