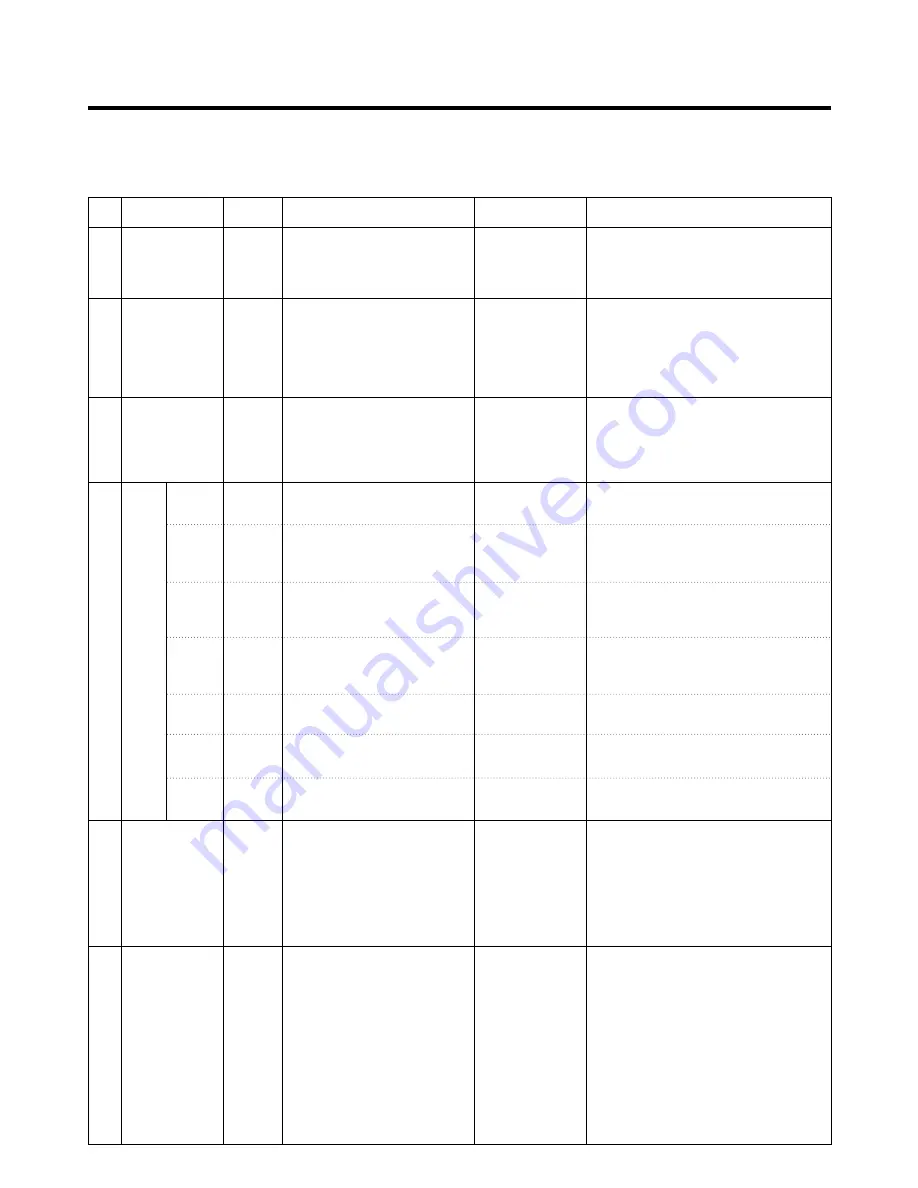
- 16 -
NO.
ITEMS
UNIT
STANDARDS
PURPOSES
REMARKS
▼
General Control of Refrigerating Cycle
Pipe and
piping system
opening time
Welding
N
2
sealed
parts
Refrige-
ration
Cycle
Refrigerant
weighing
Drier
replacement
Leak check
1
2
3
4
5
6
7
Min.
Nitrogen
pressure
Confirm
N
2
leak
Min.
Torr
EA
EA
EA
EA
Pipe: within 1 hour.
Comp: within 10 minutes.
Drier: within 20 minutes.
Weld under Nitrogen
atmosphere.
(N
2
pressure:
0.1~0.2 kg/cm
2
)
Confirm the sound of
pressure relief when
removing the rubber cap.
Sound: usable
No sound: not usable
More than 40 minutes
Below 0.03 (ref)
High and low pressure sides
are evacuated at the same
time for models above 200
l
.
Use R-134a manifold
exclusively.
Use R-134a manifold
exclusively.
R-134a manifold exclusively.
R-134a manifold exclusively.
Use R-134a exclusively.
Weighing allowance:
±
5g
Note: Winter: -5g
Summer: +5g
- Use R-134a exclusively for
R-134a refrigerator.
- Replace drier whenever repairing
refrigerator cycle piping.
- Do not use soapy water for
check. It may be sucked
into the pipe by a vacuum.
To protect
moisture
penetration.
To protect oxide
scale formation.
To protect
moisture
penetration.
To remove moisture.
To protect mixing
of mineral and
ester oils.
To protect R-12
refrigerant mixing.
To protect R-12
refrigerant mixing.
To protect R-12
refrigerant mixing.
Do not mix with
R-12 refrigerant.
To remove the
moisture from
pipe inside.
Defect in
refrigerant leak
area.
The opening time should be reduced
to a half of the standards during rain
and rainy seasons (the penetration of
water into the pipe is dangerous).
- Refer to repair note in each part.
- R-134a refrigerant is more
susceptible to leaks than R-12 and
requires more care during welding.
- Do not apply force to pipes before and
after welding to protect pipe from cracking.
- In case of evaporator parts, if it doesn't
make sound when removing rubber
cap, blow dry air or N
2
gas for more
than 1 min. and than use the parts.
Note: Only applicable to the model
equipped with reverse flow
protect plate.
Vacuum efficiency can be improved
by operating compressor during
evacuation.
The rubber pipes for R-12 refrigerant
will be melted when they are used for
R-134a refrigerant (causes of leak.)
- Do not weigh the refrigerant at too
hot or too cold an area.
(77°F [25°C] is adequate.)
- Make Copper charging canister
(Device filling refrigerant)
Socket: 2SV Plug: 2PV R-134a
Note: Do not burn O-ring (bushing)
during welding.
- Check for an oil leak at the refrigerant
leak area. Use an electronic leak
detector if an oil leak is not found.
- The electronic leak detector is very
sensitive to halogen gas in the air. It
also can detect R-141b in urethane.
Practice many times before using this
type of detector to avoid false readings.
Evacuation
time
Vacuum
degree
Vacuum
Vacuum
piping
Pipe
coupler
Outlet
(Socket)
Plug
Содержание LRTN19320
Страница 9: ...BEST MODEL 5 CIRCUIT DIAGRAM 9 ...
Страница 10: ...BETTER MODEL 10 ...
Страница 40: ...P No 3828JL8008A MARZO 2003 Printed in México ...