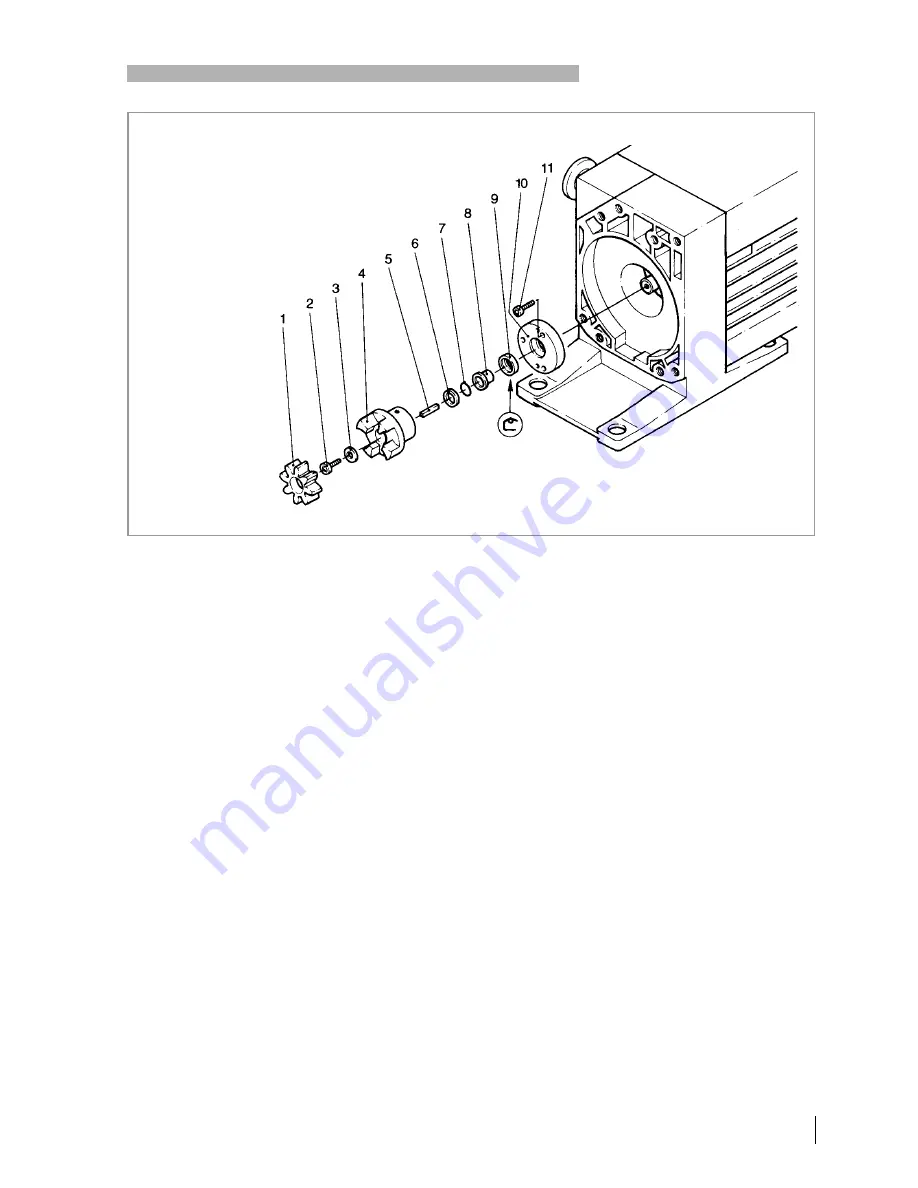
GA01201_1002 - 07/2005
27
Maintenance
5.6
Replacing the Shaft Seal
Required tools:
Allen keys 3 mm, 5 mm, 8 mm, flat-nose pliers, plastic hammer, shaft seal
driver, possibly puller for coupling.
The TRIVAC 4/8 B has two shaft seals; the outer one is subject to greater
wear. Oil marks under the coupling housing are signs of a damaged outer
shaft seal.
The outer shaft seal (12/9) can be replaced without removing or disassem-
bling the pump module.
Shutdown the pump.
Drain the oil (see Section 5.2) or place the pump on its front side.
Unscrew the four non-recessed hex. socket screws (11/7) and remove the
motor (11/6) together with the intermediate flange (11/8).
Remove the gasket (11/1).
Remove the coupling element (12/1).
Remove the hex. socket screw (12/2) and the spring washer (12/3).
Pull off the coupling (12/4).
Remove the key (12/5).
Pull off the compression disc (12/6) and the O-ring (12/7).
Unscrew the hex. socket screws (12/11) and pull off the centering disk
(12/10) together with the bushing (12/8).
If the centering disk is stuck, screw the capscrews (12/11) into the jack-
screw holes in the centering disk.
Fig. 12 Exchanging the shaft seal
Key to Fig. 12
1 Coupling element
2 Hexagon socket screw
3 Spring washer
4 Coupling (one half)
5 Key
6 Compression disc
7 O-ring
8 Bushing
9 Shaft seal
10 Centering disk
11 Hexagon socket screws