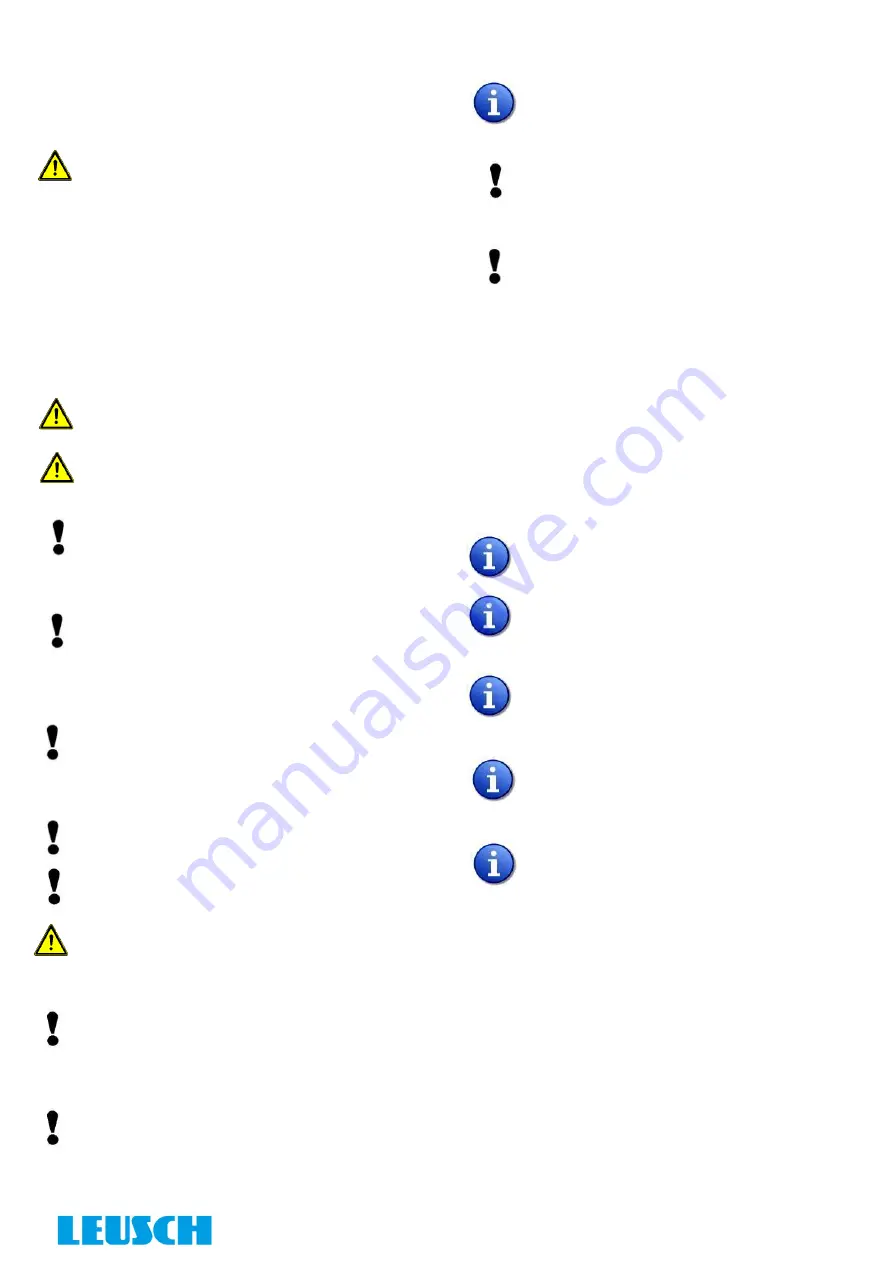
6
During maintanance and adjustment works, the
following issues have to be considered
1. Before starting work on the device, ensure that:
all energy supply lines and control signals of the
actuator are disconnected or locked so that the
actuator cannot unexpectedly set the valve disc
in motion
the affected system part is de-pressurised and
the pipeline has been emptied. Special precau-
tions must be taken (e.g. personal protective
equipment) if there is a risk of escaping fluid.
Parts which are to be processed have cooled or
warmed up to ambient temperature to prevent
burns from (skin) contact.
the valve disc is in the closed position in cases
where the valve must be removed from the pipe-
line.
2. Never loosen or tighten fastening elements (e.g.
screws/bolts) on parts when they are pressur-
ised.
3. No manual gear or actuators may be disassem-
bled when the butterfly valves are pressurised.
4. Visually check the device at regular intervals for
contamination, corrosion, leaks, functionality and
other adverse effects. Further points to be
checked may include: Usability, settings on the
components, labels, coating and conductivity
5. In the event of leaks on the gland packing, alter-
nately tighten the nuts on the gland in small
steps. Do not tighten nuts more than necessary.
Comply with the maximum
torques Page 8, Tab. 1
6. Modifications to the factory settings for actuators
(e.g. limit stops) and accessories (e.g. filter regu-
lator, booster) are not permitted and may only be
carried out in individual cases with the approval
of the manufacturer by qualified and specialised
personnel.
7. Only use original spare parts for maintenance/
repairs. These are available on request
8. During reassembly in the pipework the note in
section 7 has to be considered
9. After finishing the service/repair, a hydrostatic
pressure test on the pressure loaded parts has to
be executed according to a suitable test proce-
dure
10.Valves which are not actuated for long periods
must undergo functional tests on a regular basis.
If necessary, shorter maintenance intervals may
be required if increased wear is expected on the
sealing elements (e.g. through abrasive, chemi-
cal or other adverse effects).
11.Valves for the SIL (Safety Integrity Level) Appli-
cation must be handled according to the follow-
ing standards in regard to maintenance and re-
pair: - VDI 2180, -EN 61511,- EN 61508,
Manual WA 236
Limit stop adjustment
If necessary (e.g. in the event of impermissi-
ble leakage on the sealing element of the
valve), the adjustment pressure between
Seat and Seatring can be changed by adjust-
ing the limit Stop position at the actuator.
ATTENTION! Settings may only be changed
by specialist personnel, with the approval of
the manufacturer, who are familiar with the
handling and setting of such devices. The
instructions in the operating instructions of
the actuator for setting the limit stops must
also be followed unconditionally
Before settings are changed, a functional test
should first be carried out as follows:
Open the valve fully to flush out possible
solids from the sealing surfaces of Seat
and Seatring.
Close the valve and check whether the
valve closes correctly (there should be
no solids stuck between the Seat and
Seatring).
The following procedure is recommended if
no improvement has been achieved:
1.
Loosen the lock nut for the limit position
stop and slightly open the valve until the
stop has been cleared.
2.
Turn the adjustment screw by 1/4 turns
in counter clockwise direction and clos-
es the valve again. Check for leakage
integrity.
3.
If the result is satisfactory (observing
the permissible leakage rate), tighten
the lock nut again while the valve disc is
closed.
4.
Otherwise repeat step 2. However, the
adjustment screw should not be un-
screwed by more than 1 revolution alto-
gether.
5.
If the leakage rate remains impermissible,
the sealing pair (Seat/Seatring) may pos-
sibly be damaged and must be examined
more closely (e.g. replacing the Seatring).
The manufacturer should be notified in
this case.