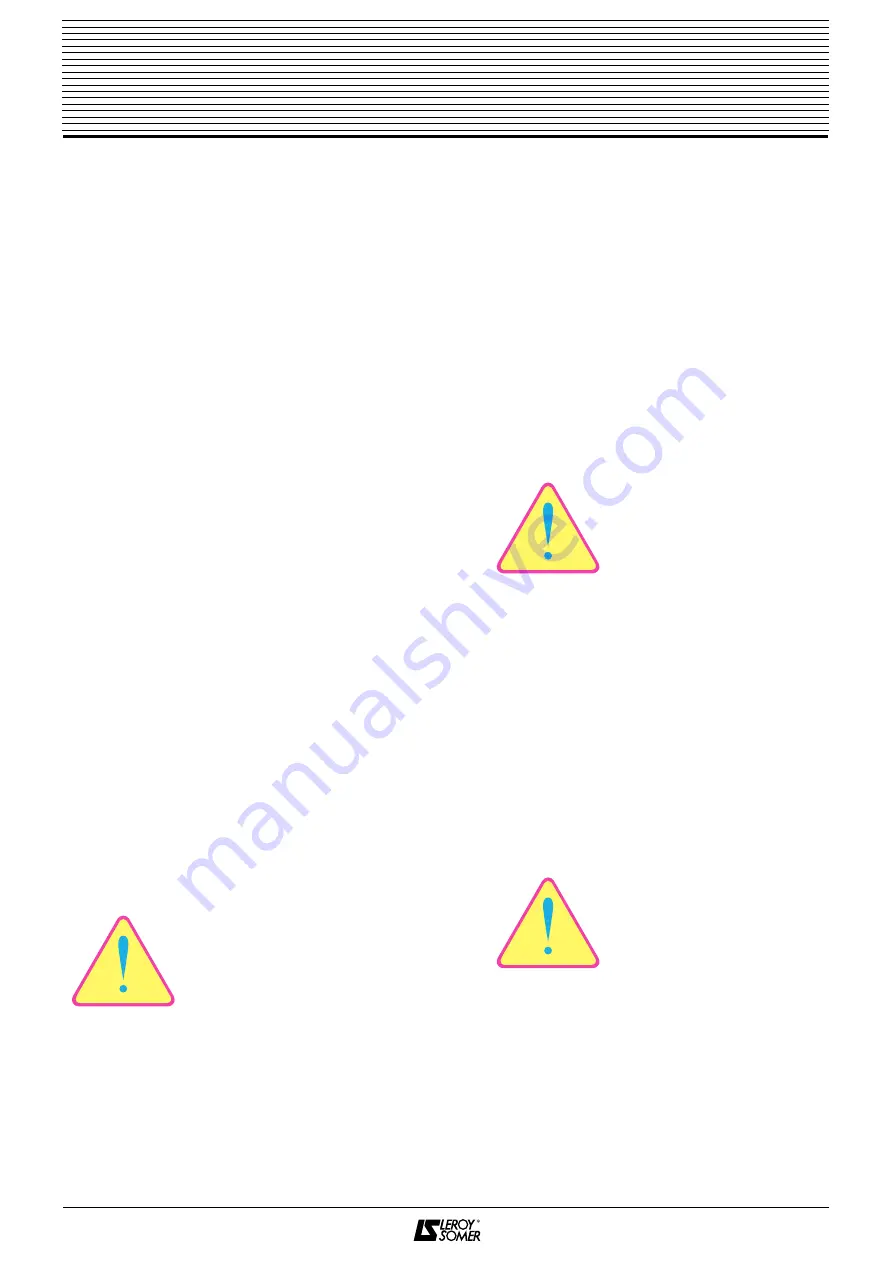
1 : + brush wear probes
2 : - brush wear probes
3 - 4 : space heaters
1T7 - 2T7: front end shield probes (DE)
1T8 - 2T8: rear end shield probes (NDE)
The labels used for the thermal detectors
incorporated into the windings are as follows:
• on one level:
T1 - T2: trip;
• on two levels:
1T1 - 1T2: alarm
2T1 - 2T2: trip.
6.5 - Accessories
(see technical catalogue ref. 1337… section G)
For motors equipped with option(s) check that the
correct parts are used for the various connections
(brake, tacho detector, etc). For the brake, check
the power supply voltage conforms with that of the
winding, indicated on the brake plate. Refer to the
detailed manual on brakes enclosed.
Do not forget to connect the air flow detector if
necessary.
If motors fitted with a pulse generator (PG or
encoder) have a connecting cable longer than
20 m, the cable should be of the shielded twisted
pair type and should be no longer than 500 m to
the opto-coupler input.
If necessary, the connection of the detection
probes to the relay (brush wear detection probes
are optional) can control an audible or flashing
alarm, or a circuit-breaker.
6.6 - Before start-up
Do a global check reviewing the whole drive
chain to ensure nothing has been forgotten
(tightening of various screws and bolts,
installation of various components).
Warning : the ventilation unit
should be installed, then the
field powered at the rated
voltage before the motor is
started.
The power supply must include
protection against field faults
(risk motor racing : taken into
account by LEROY-SOMER
speed controllers).
Changing the direction of rotation
This should be done when the motor is powered
down; to change the direction of motor rotation
reverse the field polarity.
7. - MAINTENANCE
See section 5 of the general manual reference
1596… to ensure the motor lasts as long as
possible.
Brushes
Warning : the following operations must only be
performed when the motor is at a standstill and
powered down.
The brushes should be checked (state of the
brushes, freedom of movement, pressure exerted
by the springs) 200 hours after first use. They
should be checked again after a further 500 hours
of operation. The results of these two checks
should be used to determine the interval at which
periodic checks are made. Replace the brushes be-
fore they reach the wear limit indicated on the label.
IP 55 IC 416 motors only : each
time the motor is checked or at
most every 500 hours, com-
pletely clean (armature and
commutator : inside and out-
side, stator) by blowing with
compressed air, with the ins-
pection doors open.
8. - RECOMMENDED SPARE PARTS
We recommend the following emergency spare
parts :
- set of brushes,
- set of bearings.
Other main parts :
- brush-holders,
- set of armature windings,
- set of main pole windings,
- set of pole switching windings,
- wound armature (balanced),
- ventilation induction motor.
9. - DISMANTLING
During the guarantee period this
operation should only be
performed in a LEROY-SOMER
approved workshop or at one of
our factories, otherwise the
guarantee may no longer be valid.
When the guarantee period is over any
dismantling operations should either be done by
an approved workshop or at one of our factories.
Day-to-day maintenance may be performed by
staff trained in electrical rotating machines.
See exploded view (p.10 to 13) for how to
configure parts.
9.1 - Procedure
- Switch off the motor and disconnect it from the
machine.
-
Label the cables and connections in the
terminal box. Disconnect them.
6
LSK
D.C. motors