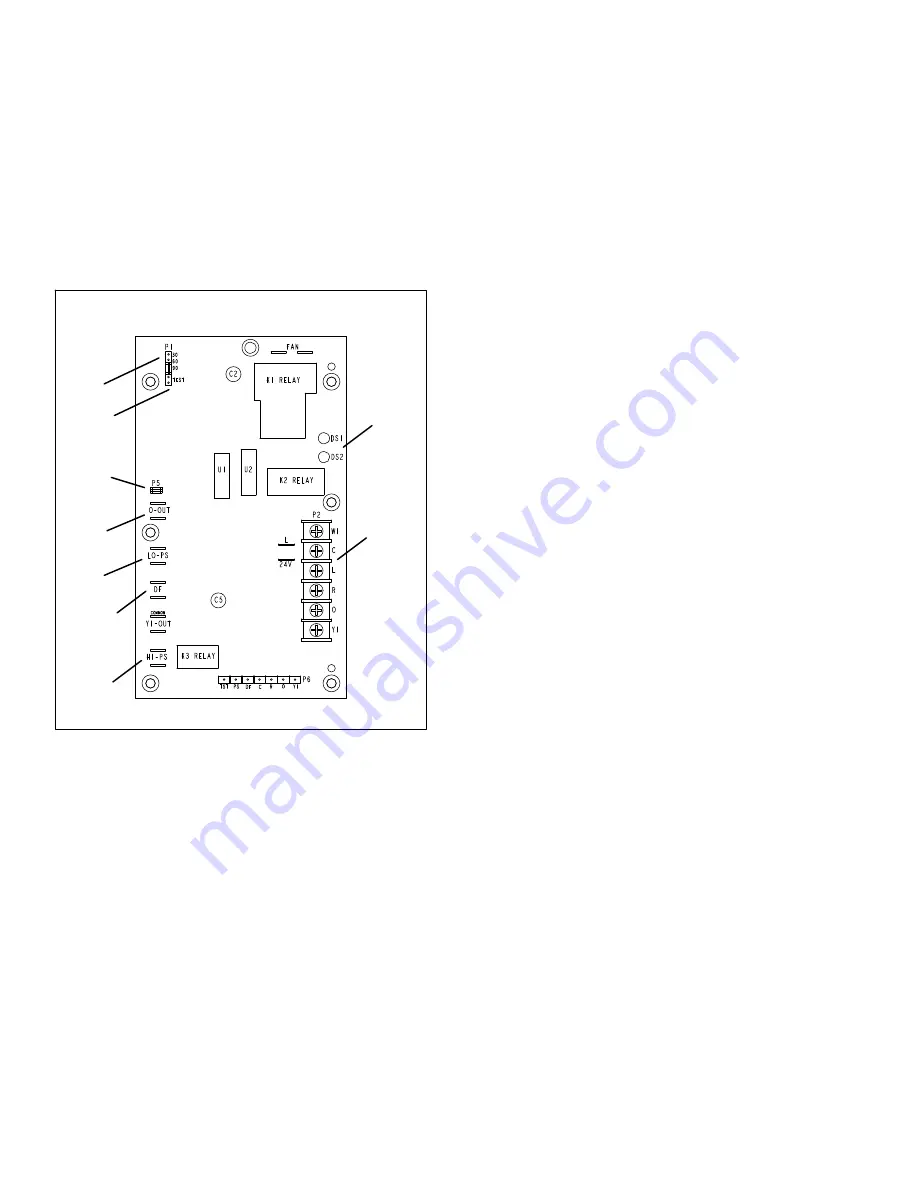
Page 5
Revised 05−2009
TPA*S4
Defrost Control
The defrost control board includes the combined functions
of a time/temperature defrost control, defrost relay,
diagnostic LEDs and terminal strip for field wiring
connections. See figure 4.
The control provides automatic switching from normal
heating operation to defrost mode and back. During
compressor cycle (call for defrost), the control
accumulates compressor run times at 30-, 60-, or
90-minute field−adjustable intervals. If the defrost
thermostat is closed when the selected compressor run
time interval ends, the defrost relay is energized and
defrost begins.
TPA036S4 Outdoor Unit Defrost Control
Board
FIGURE 4
LEDs
24v terminal
strip
Timing
Pins
Test Pins
Compressor
Delay Pins
Reversing
Valve
Low Pressure
Switch (S87)
High Pressure
Switch (S4)
Defrost
Thermostat
Defrost Control Timing Pins
Each timing pin selection provides a different
accumulated compressor run time period for one defrost
cycle. This time period must occur before a defrost cycle
is initiated. The defrost interval can be adjusted to 30
(T1), 60 (T2), or 90 (T3) minutes (see figure 4). The
defrost timing jumper is factory−installed to provide a
90−minute defrost interval. If the timing selector jumper is
not in place, the control defaults to a 90−minute defrost
interval. The maximum defrost period is 14 minutes and
cannot be adjusted.
A TEST option is provided for troubleshooting.
The TEST
mode may be started any time the unit is in the heating
mode and the defrost thermostat is closed or
jumpered.
If the jumper is in the TEST position at
power-up, the control will ignore the test pins. When the
jumper is placed across the TEST pins for two seconds, the
control will enter the defrost mode. If the jumper is removed
before an additional 5−second period has elapsed (7
seconds total), the unit will remain in defrost mode until the
defrost thermostat opens or 14 minutes have passed. If the
jumper is not removed until after the additional 5−second
period has elapsed, the defrost will terminate and the test
option will not function again until the jumper is removed
and re−applied.
Compressor Delay
The defrost board has a field−selectable function to reduce
occasional sounds that may occur while the unit is cycling
in and out of the defrost mode. The compressor will be
cycled off for 30 seconds going in and out of the defrost
mode when the compressor delay jumper is removed.
NOTE − The 30-second off" cycle is not functional when
jumpering the TEST pins.
Time Delay
The timed-off delay is five minutes long. The delay helps to
protect the compressor from short-cycling in case the
power to the unit is interrupted or a pressure switch opens.
The delay is bypassed by placing the timer select jumper
across the TEST pins for 0.5 seconds.
Pressure Switch Circuit
The defrost control incorporates two pressure switch
circuits. The optional high pressure switch (S4) connects to
the board’s HI PS terminals. The board also includes
connections for an optional low pressure, or
loss-of-charge-pressure, switch (S87). See figure 4 for
switch terminal location.
During a single demand cycle, the defrost control will lock
out the unit after the fifth time that the circuit is interrupted
by any pressure switch wired to the control board. In
addition, the diagnostic LEDs will indicate a locked-out
pressure switch after the fifth occurrence of an open
pressure switch (see Table 1). The unit will remain locked
out until power to the board is interrupted, then
re-established or until the jumper is applied to the TEST
pins for 0.5 seconds.
NOTE The defrost control board ignores input from the
low-pressure switch terminals as follows:
S
during the TEST mode,
S
during the defrost cycle,
S
during the 90-second start-up period,
S
and for the first 90 seconds each time the reversing
valve switches heat/cool modes.
If the TEST pins are
jumpered and the 5-minute delay is being
bypassed, the LO PS terminal signal is not ignored
during the 90-second start-up period.