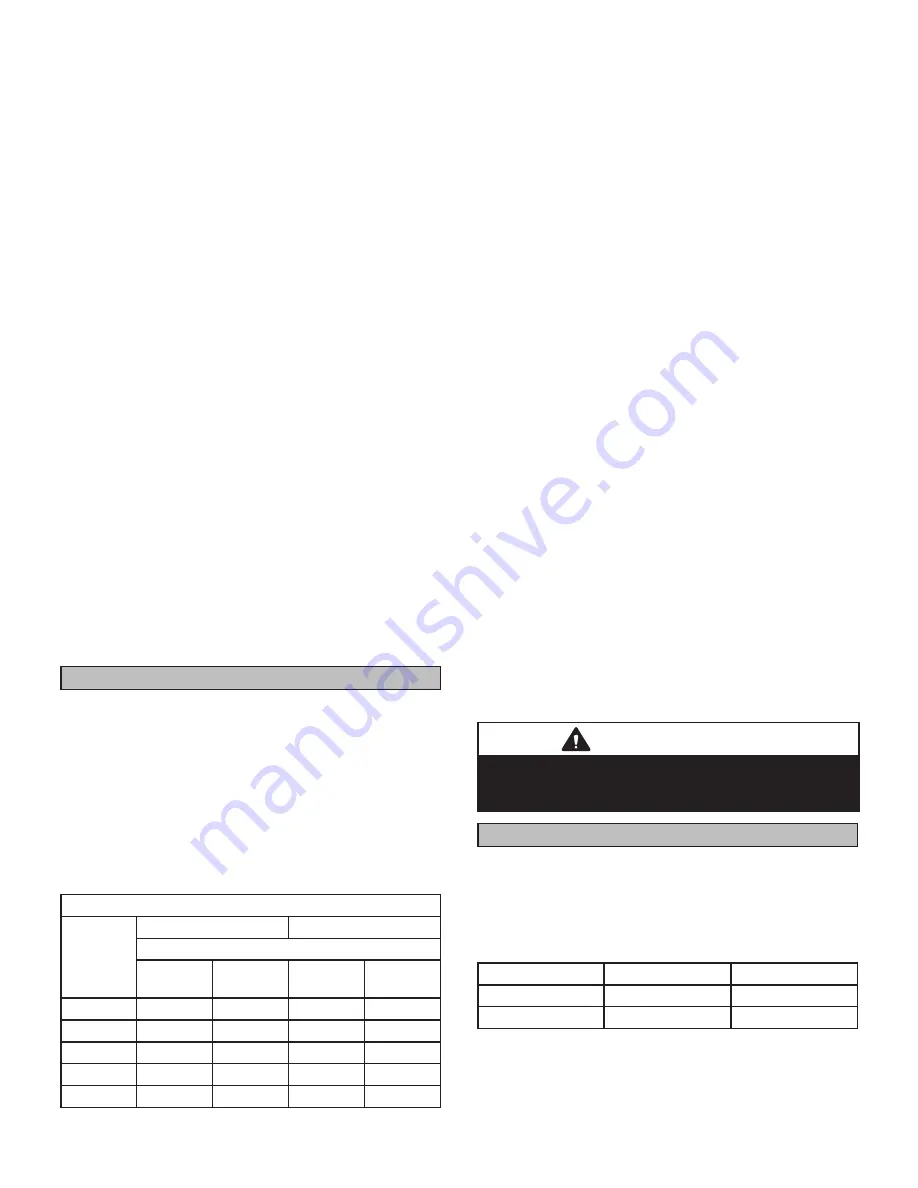
Page 42
12 -
If the appliance will not operate, follow the
instructions “Turning Off Gas to Unit” and call your
service technician or gas supplier.
Turning Off Gas to Unit
1 - Set the thermostat to the lowest setting.
2 - Turn off all electrical power to the unit if service is to
be performed.
3 - Remove the upper access panel.
4 - Move gas valve switch to
OFF
position. Do not
force. See figure 34 or 35.
5 - Replace the upper access panel.
Failure To Operate
If the unit fails to operate, check the following:
1 - Is the thermostat calling for heat?
2 - Are access panels securely in place?
3 - Is the main disconnect switch closed?
4 - Is there a blown fuse or tripped circuit breaker?
5 -
Is the filter dirty or plugged? Dirty or plugged filters
will cause the limit control to shut the unit off.
6 - Is gas turned on at the meter?
7 - Is the manual main shut-off valve open?
8 - Is the internal manual shut-off valve open?
9 - Is the unit ignition system in lock out? If the unit locks
out again, call the service technician to inspect the
unit for blockages.
10 -
Is pressure switch closed? Obstructed flue will
cause unit to shut off at pressure switch. Check flue
and outlet for blockages.
11 -
Are flame rollout switches tripped? If flame rollout
switches are tripped, call the service technician for
inspection.
Gas Pressure Adjustment
Furnace should operate at least 5 minutes before check-
ing gas flow. Determine time in seconds for two revolu
-
tions of gas through the meter. (Two revolutions assures
a more accurate time.) Divide by two and compare to time
in table 17 below. If manifold pressure matches table 19
and rate is incorrect, check gas orifices for proper size and
restriction. Remove temporary gas meter if installed.
NOTE - Shut unit off and remove manometer as soon as
an accurate reading has been obtained. Take care to re-
place pressure tap plug.
TABLE 17
GAS METERING CLOCKING CHART
SL280
Unit
Natural 1000 btu/cu ft
LP 2500 btu cu/cu ft
Seconds For One Revolution
1 cu ft
dial
2 cu fr
dial
1 cu ft
Dial
2 cu ft
Dial
-045
80
160
200
400
-070
55
110
136
272
-090
41
82
102
204
-110
33
66
82
164
-135
27
54
68
136
Supply Line Pressure
White Rodgers Gas Valve
An inlet post located on the gas valve provides access
to the supply pressure. See figure 34. Back out the 3/32
hex screw one turn, connect a piece of 5/16 tubing and
connect to a manometer to measure supply pressure. See
table 19 for supply line pressure.
Honeywell Gas Valve
A threaded plug on the inlet side of the gas valve provides
access to the supply pressure tap. Remove the thread-
ed plug, install a field-provided barbed fitting and connect
a manometer to measure supply pressure. See table 19
for supply line pressure. Replace the threaded plug after
measurements have been taken.
Manifold Pressure
NOTE - Pressure test adapter kit (10L34) is available from
Lennox to facilitate manifold pressure measurement.
1 -
Connect test gauge to manifold pressure post
(figure 34) or tap (figure 35) on gas valve.
2 -
Ignite unit on high fire and let run for 5 minutes to
allow for steady state conditions.
3 - After allowing unit to stabilize for 5 minutes, record
manifold pressure and compare to value given in
table 19.
4 - If necessary, make adjustments. Figures 34 and 35
show location of high fire adjustment screw.
5 -
If an adjustment is made on high fire, re-check
manifold pressure on low fire. Do not adjust low fire
manifold pressure. If low fire manifold pressure is
more than 1/2” above or below value specified in
table 19, replace valve.
6 - Shut unit off and remove manometer as soon as an
accurate reading has been obtained. Take care to
replace pressure tap plug if removed.
7 - Start unit and perform leak check. Seal leaks if
found.
IMPORTANT
For safety, shut unit off and remove manometer as soon
as an accurate reading has been obtained. Take care to
replace pressure tap plug.
Proper Combustion
Furnace should operate minimum 15 minutes with correct
manifold pressure and gas flow rate before checking com
-
bustion. Table 18 shows acceptable combustion for ALL
SL280UHV models.
The maximum carbon monoxide
reading should not exceed 100 ppm.
TABLE 18
Firing Rate
CO
2
% For Nat
CO
2
% For LP
High Fire
6.8 - 7.4
7.5 - 9.0
Low Fire
4.2 - 5.7
5.0 - 6.0