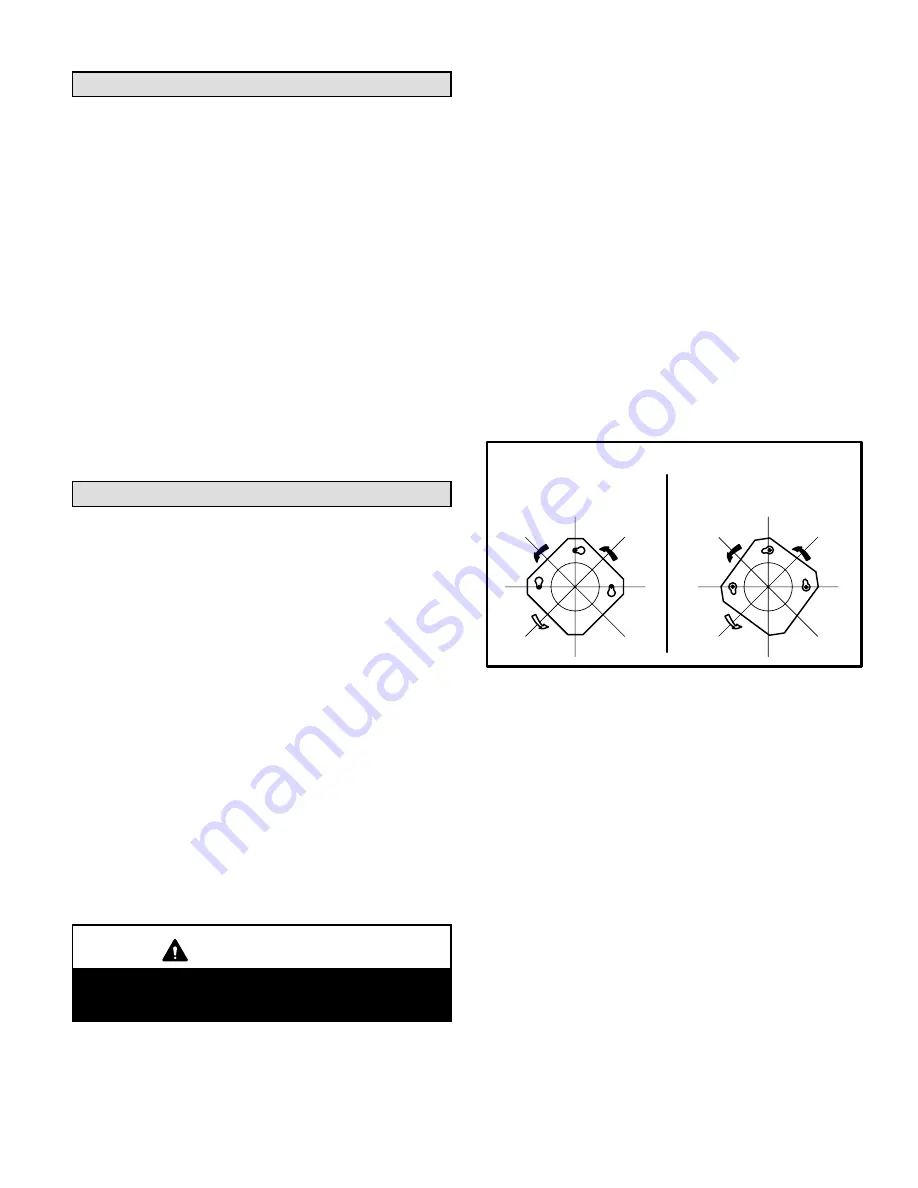
Page 5
Locate & Level the Unit
The compact design of this furnace makes it ideal for a
basement or utility room installation. Choose a central
location for the furnace so that supply air ducts approxi-
mately the same length. This will allow each room to re-
ceive the proper amount of heat. The furnace should be
placed so that the flue connection to the chimney will be of
minimum length and have a minimum number of elbows.
1− Set the unit in desired location keeping in mind the
clearances listed in table 2. Also keep in mind oil sup-
ply connections, electrical supply, flue connections
and sufficient clearance for installing and servicing
unit.
2− Level the unit from side to side and from front to rear. If
the furnace is not level, place fireproof wedges or
shims between the low side of the furnace and the
floor. Make sure the weight of the furnace is distributed
evenly on all four corners. Strain on sides of cabinet
causing cracking and popping noises may occur if
weight of furnace is not evenly distributed.
Unit Adjustments
Neither the nozzle setting nor the air adjustments are facto-
ry set. The furnace is fire tested and the limit control is
checked to make sure it functions properly; no factory set-
tings are made. During installation, the furnace must be
set up." The installing dealer/contractor must have and
use proper test equipment in order to correctly set up the oil
furnace. Proper testing equipment is required to ensure
correct operation of the unit. The use of test equipment is
now more critical than ever due to tighter tolerances need-
ed to keep the furnace operating efficiently.
Among the test equipment for an oil furnace, the proper
combustion test kit should contain the following:
D
Draft gauge
D
CO
2
or O
2
Analyzer
D
Smoke tester
D
Pressure gauge
D
High temperature thermometer
D
Oil vacuum gauge
D
Beckett T−500 gauge
D
Knowledge of proper test equipment operation
CAUTION
Improper nozzle and/or air adjustment of this unit
may result in sooting problems. Refer to the follow-
ing section for correct adjustment procedures.
Nozzle Adjustment
Proper adjustment of the nozzle assembly is critical because
alignment may have changed during shipping. Before the fur-
nace and oil lines are installed, the nozzle assembly must be
checked. This may easily be done by removing the entire
burner assembly (not just the nozzle) from the furnace. The
lower firing nozzle is factory installed. This should be verified
by the installer. Inspect the spark transformer leads also to
ensure they are still attached to the electrodes.
Note that
OF23−105/120 and OF23−140/154 series units use the
Beckett AFII burner. OF23−175/210R series units use the
Beckett AFG burner.
The burner assembly is attached to the vestibule panel by
three nuts. Slots are provided in the mounting flange for re-
moving the burner assembly from the vestibule. By loosen-
ing the nuts and by turning the whole burner assembly coun-
terclockwise (figure 3), the entire burner assembly will come
out of the furnace. There is adequate wire to remove the
burner without disconnecting wires. Once removed, just turn
the burner around in the vest panel area.
Figure 3
OF23 Series Burner Removal
First, loosen three nuts which
attach burner to vest panel.
Next, rotate burner counter-
clockwise on slots then pull
toward you.
To correctly adjust the nozzle, use a Beckett #T−500 gauge.
Insert the small end of the gauge into the end of the cone
and measure from the flat of the end cone to the tip of the
nozzle. When nozzle depth is correct, the tip of the nozzle
should just touch the end of the gauge. Refer to the illustra-
tion sheet provided with the gauge. Note that the scale side
of the gauge is not used for this purpose. Corrections are
made by sliding the entire nozzle assembly forward or
backward within the blast tube (figure 4). At the same time,
nozzle alignment must be checked.
To check nozzle alignment, again insert the small end of
gauge into the end cone and measure the nozzle and
electrode alignment against the center lines marked on
the gauge (again refer to enclosed illustration sheet). If
the nozzle is not centered, but found to be too far left or
right, a new nozzle assembly will need to be ordered. Do
not attempt to adjust by bending the 90 degree elbow in
the oil line.