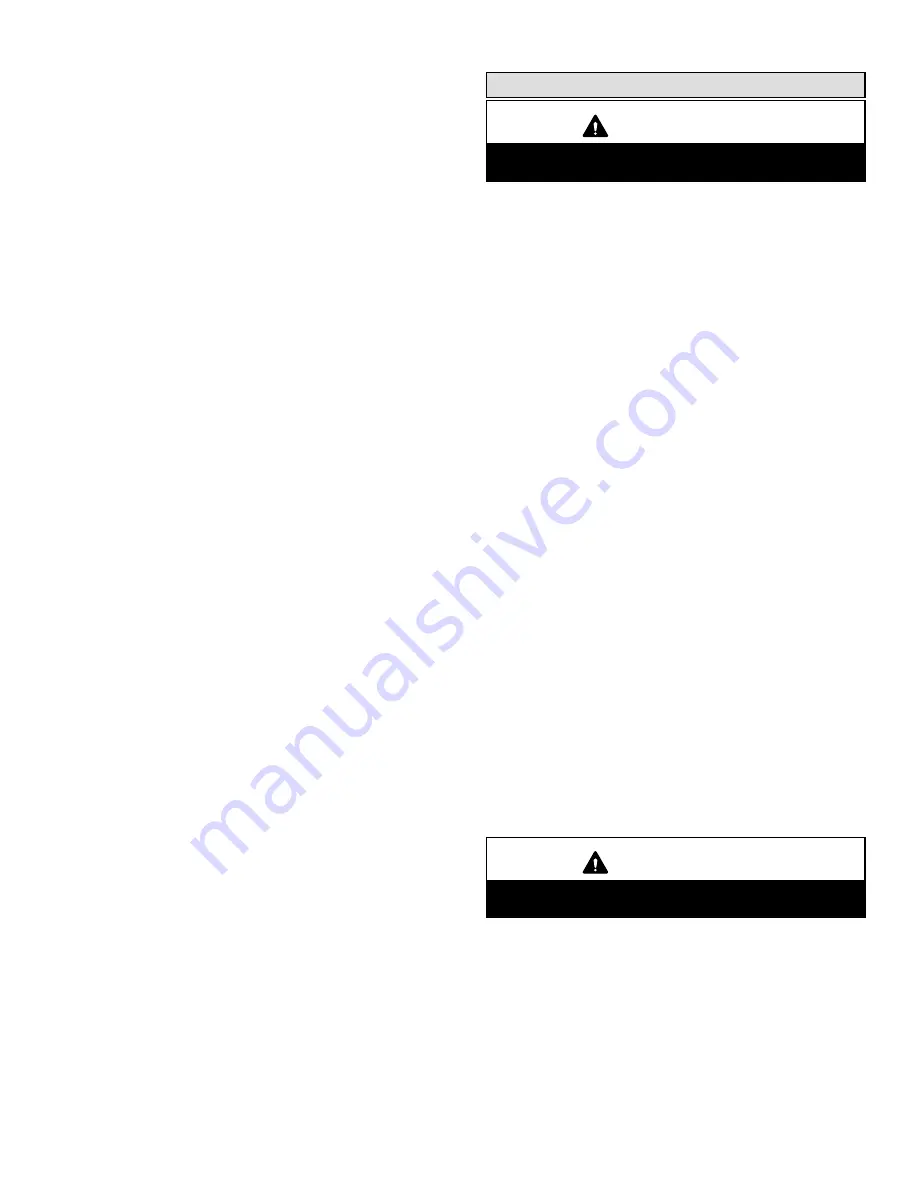
Page 17
2 − Overfire Draft
This test should be taken with the burner in operation. Re-
move the screw from the center of the inspection port. In-
sert your draft gauge into the hole.
A reading of the overfire draft should be 0.02 less than the
reading found in the vent connector. If a positive reading is
seen at this point, the combustion fan is pumping too much
air into the heat exchanger. Make the necessary adjust-
ments at the air adjustment dial.
3 − Smoke Test
The smoke test should be taken at the hole drilled in step 1.
Using a smoke test gun adjust the air inlet shutter so that
you will have just a trace of smoke. Somewhere between a
0 and #1 smoke. This is the
starting
point. Do not stop here.
4 − CO
2
Test
Again, take this sample at the vent pipe. With the unit firing
at a trace of smoke, take a sample of the CO
2
.
From the results of this test, a window of operation" will be
determined. This window of operation establishes some
tolerance. The tolerance the installer builds in provides
room within the set-up for those things which might affect
combustion. Those things which might affect combustion
can then do so without causing the unit to start sooting/
smoking. Things which might affect combustion include a
nozzle going bad, draft that changes during different clima-
tic conditions, dirty oil, dirt obstructing the air inlet, etc.
To build in a window of operation," set up the burner to be
2% less in CO
2
. For example, if you find a reading of 12%
CO
2
, adjust the air inlet shutter to increase the air and drop
the CO
2
to 10%.
5 − Retest the Smoke
With a drop in the CO
2
and increase in the air you should
see that the smoke has returned to 0.
6 − Retest the Overfire Draft
This test serves to confirm that you have not increased the
air too much. Again you do not want a positive pressure at
the test port. It should still be 0.02 less than the draft pres-
sure reading taken at the breach. You may need to in-
crease the stack draft by adjusting the barometric draft
control.
7 − Stack Temperature
Take a stack temperature reading in the vent pipe. Subtract
the room air temperature from the stack temperature. This
will give you the net stack temperature. Use the efficiency
charts provided in most CO
2
analyzers to determine fur-
nace efficiency.
Service
CAUTION
Do not tamper with unit controls. Call your qualified
service technician.
A − Servicing Filter
NOTE − Under no circumstances should the access panels
to the blower compartment be left off or left partially open.
Throw-Away Type Filters
Check filters monthly and re-
place when necessary to assure proper furnace operation.
Replace filters with like kind and size filters.
Reusable Type Filters
Filters should be checked month-
ly and cleaned when necessary to assure proper furnace
operation.
B − Blower
Blower motor is prelubricated and sealed for extended op-
eration. No further lubrication is required. Disconnect pow-
er to unit before cleaning blower wheel for debris.
C − Flue Pipe Inspection
The flue pipe should be inspected annually by a qualified
service technician. Remove and clean any soot or ash
found in the flue pipe. Inspect pipe for holes or rusted
areas. If replacement is necessary, replace with the same
size and type as required by code. Inspect the flue draft
control device and replace if found defective.
D − Cleaning the Heat Exchanger
1 − Remove the vent pipe from the furnace.
2 − Remove the locking screws and the caps from the
clean out tubes. Remove flue access elbow.
3 − Using a long spiral wire brush, sweep down the outer
drum of the heat exchanger. Then using the hose at-
tachment, vacuum out loose debris.
4 − Remove the locking screw and cap from the observa-
tion tube and with the spiral wire brush, reach upward
toward the rear of the heat exchanger to clean out the
crossover tube.
CAUTION
Do not attempt to clean the combustion chamber. It
can be easily damaged.
5 − Replace the clean out caps and flue access elbow.
Make sure locking screws are secure.
6 − Brush out and vacuum the vent outlet area of the outer
drum and replace vent pipe.
7 − Clean around the burner, blower deck and vestibule
area.
NOTE − A heat exchanger clean-out kit ABRSH380
(35K09) is available from Lennox.
Содержание O23Q2-70
Страница 14: ...Page 14 Figure 17 Typical O23 Wiring Diagram...
Страница 15: ...Page 15 Figure 18 Typical O23 Wiring Diagram...