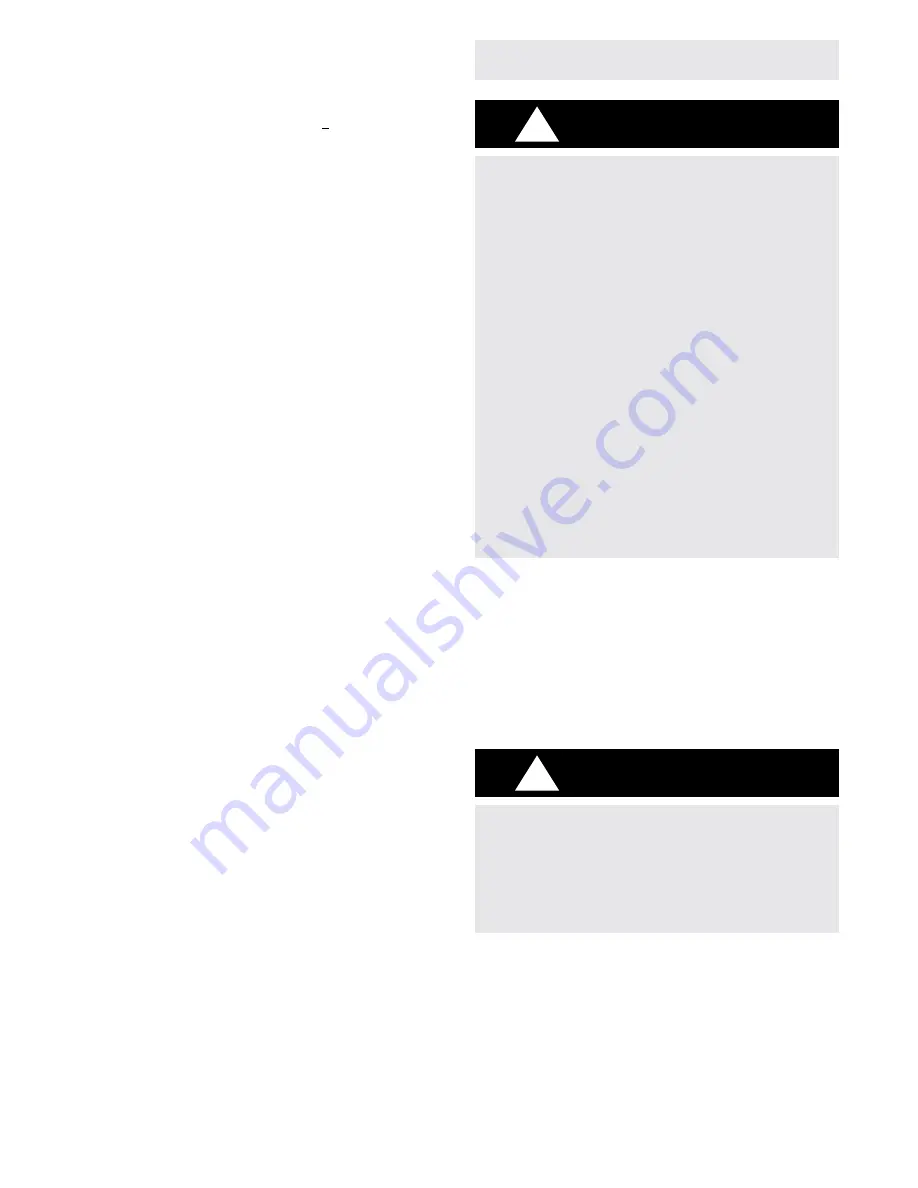
28
ELECTRICAL
1. Check all wiring for loose connections.
2. Check for the correct voltage at the furnace (furnace
operating). Correct voltage is 10%.
3. Check amp-draw on the blower motor with inner blower
panel in place.
Unit Name plate __________Actual__________
BLOWER SPEEDS
Follow the steps below to change the blower speeds.
1. Turn off electrical power to furnace.
2. Remove blower access panel.
3. Disconnect existing speed tap at integrated control speed
terminal.
See unit Product Specifications bulletin for indoor blower
data.
NOTE:
Termination of any unused motor leads must be
insulated.
4. Place unused blower speed tap on integrated control
“PARK” terminal or insulate.
5. Refer to blower speed selection chart on unit wiring
diagram for desired heating or cooling speed. See Blower
performance data beginning on the next page.
6. Connect selected speed tap at integrated control speed
terminal.
7. Re-secure blower access panel.
8. Turn on electrical power to furnace.
9. Re-check temperature rise.
ELECTRONIC IGNITION
The integrated control has an added feature of an internal
Watchguard control. The feature serves as an automatic
reset device for integrated control lockout caused by
ignition failure. This type of lockout is usually due to low
gas line pressure. After one hour of continuous thermostat
demand for heat, the Watchguard will break and remake
thermostat demand to the furnace and automatically reset
the integrated control to begin the ignition sequence.
ELECTRICAL SHOCk, FIRE, OR EXPLOSION
HAZARD.
Failure to follow safety warnings exactly could
result in dangerous operation, serious injury,
death or property damage.
Improper servicing could result in dangerous
operation, serious injury, death, or property
damage.
Before servicing, disconnect all electrical
power to furnace.
When servicing controls, label all wires prior
to disconnecting. Take care to reconnect wires
correctly.
Verify proper operation after servicing.
WARNING
!
The blower access panel must be securely
in place when the blower and burners are
operating. Gas fumes, which could contain
carbon monoxide, can be drawn into living
space resulting in personal injury or death.
WARNING
!
SERVICE
At the beginning of each heating season, a qualified
technician should check the system as follows:
BLOWER
Check the blower wheel for debris and clean if necessary.
The blower motors are pre-lubricated for extended bearing
life. No further lubrication is needed.
FILTERS
All units filters are installed external to the unit. Filters should
be inspected monthly. Clean or replace the filters when
necessary to ensure that the furnace operates properly.
Replacement filters must be rated for high velocity airflow.
Table 2 lists recommended filter sizes.