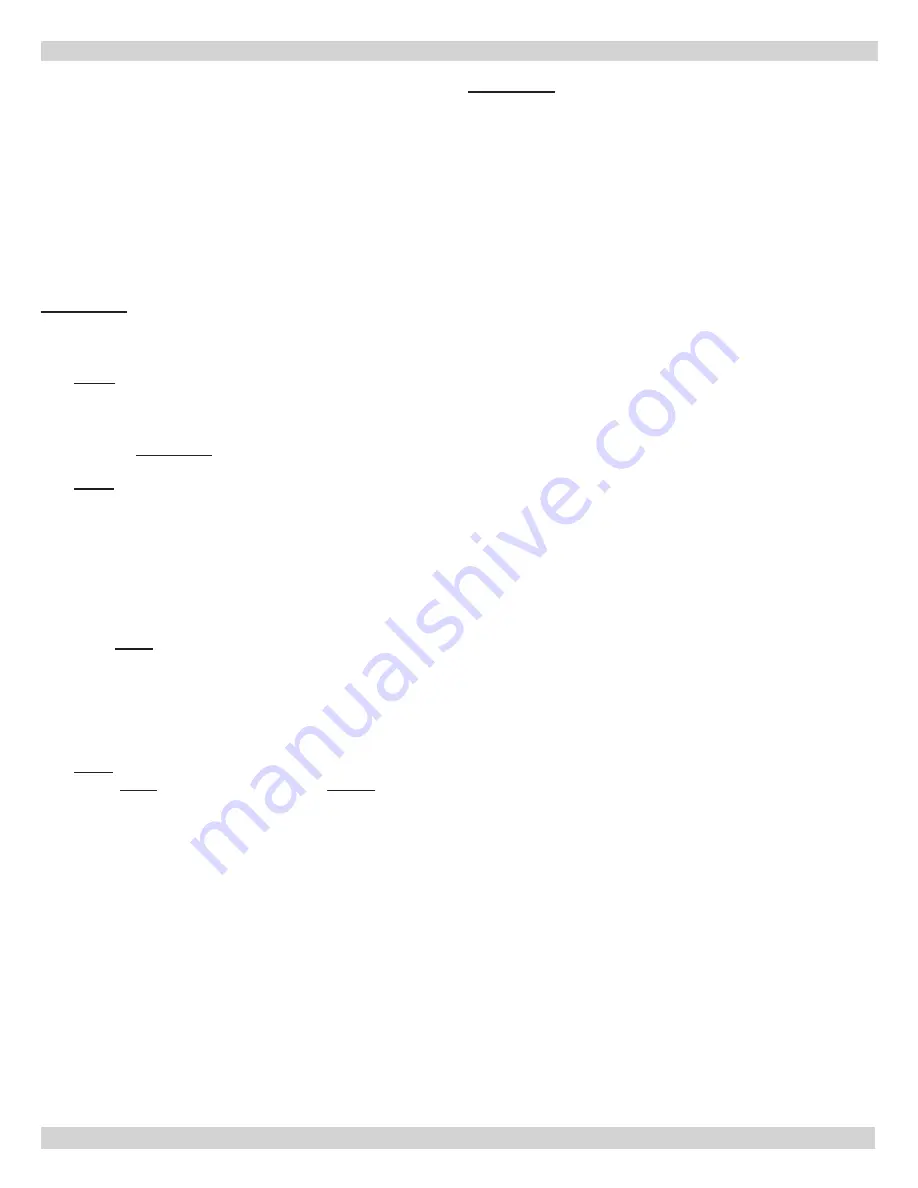
19
How A Hot Water System Operates
Entire heating system (boiler, piping, and radiation units)
is filled with water. As water in the boiler is heated, it is
circulated from top of boiler through supply main to ra-
diation units. Cooler water in radiation units flows back
through return piping through return main into the boiler.
This arrangement provides positive and rapid response to
the thermostat.
Filling The System With Water
OPTION #1
This method utilizes boiler piping as shown in
figure on page 6.
A. Close
main shutoff valve, isolation valves, and zone
valves (if applicable). If bypass piping is installed, also
close two throttling valves. Leave boiler service shutoff
valve (if installed) and balancing valves to each heat-
ing zone
fully open
.
B. Open
following valves in order: drain valve for power
purging, isolating valves before and after boiler cir-
culator (if applicable), both throttling valves (if appli-
cable), and then open fill line shutoff valve. Water will
fill bypass piping and push air through piping and out
power purging drain valve. When power purging drain
valve runs air free, close bypass piping throttling valve
(leaving throttling valve to supply piping fully open).
C.
Next,
open
isolation valve (or zone valve) to first
zone. Water will fill piping and push any air out power
purging drain valve. When power purging drain valve
runs air free, close isolation valve or zone valve). Re-
peat this procedure for remaining heating zones.
D.
Once all zones are filled with water and purged of air,
close
power purging drain valve and fill line shut off
valve,
open
main shutoff valve, and
adjust
throttling
valves and balancing valves as required.
OPTION #2
• Close air vents on all radiation units.
• Open valves to radiation units. Verify boiler drain
valve, expansion tank drain cock, and air bleed screw
on expansion tank drain fitting are closed.
•
Open fill valve on piping to expansion tank.
• Open water inlet to boiler and leave it open.
• Open air vent on lowest radiation unit.
•
When all air has escaped and water starts to flow from
vent, close it.
•
Go to next radiation unit, and repeat this process until
finishing with highest radiation unit.
• If heating system has automatic vents, this manual
venting is unnecessary but it will speed up proper fill
-
ing of the system.
If system is a closed expansion tank system, automatic fill
valve is needed. Leave automatic fill valve open to refill
system automatically as needed.
Note initial fill pressure on boiler’s temperature / pressure
gauge, which should be 10-15 psig. Any lowering of pres-
sure from its initial fill pressure indicates loss of water due
to leakage. Automatic fill valve should then compensate for
this water pressure loss. If it does not, manually open this
valve to refill system until needle is again pointing to same
pressure reading. Instructions are packaged with valve.
FILLING THE BOILER