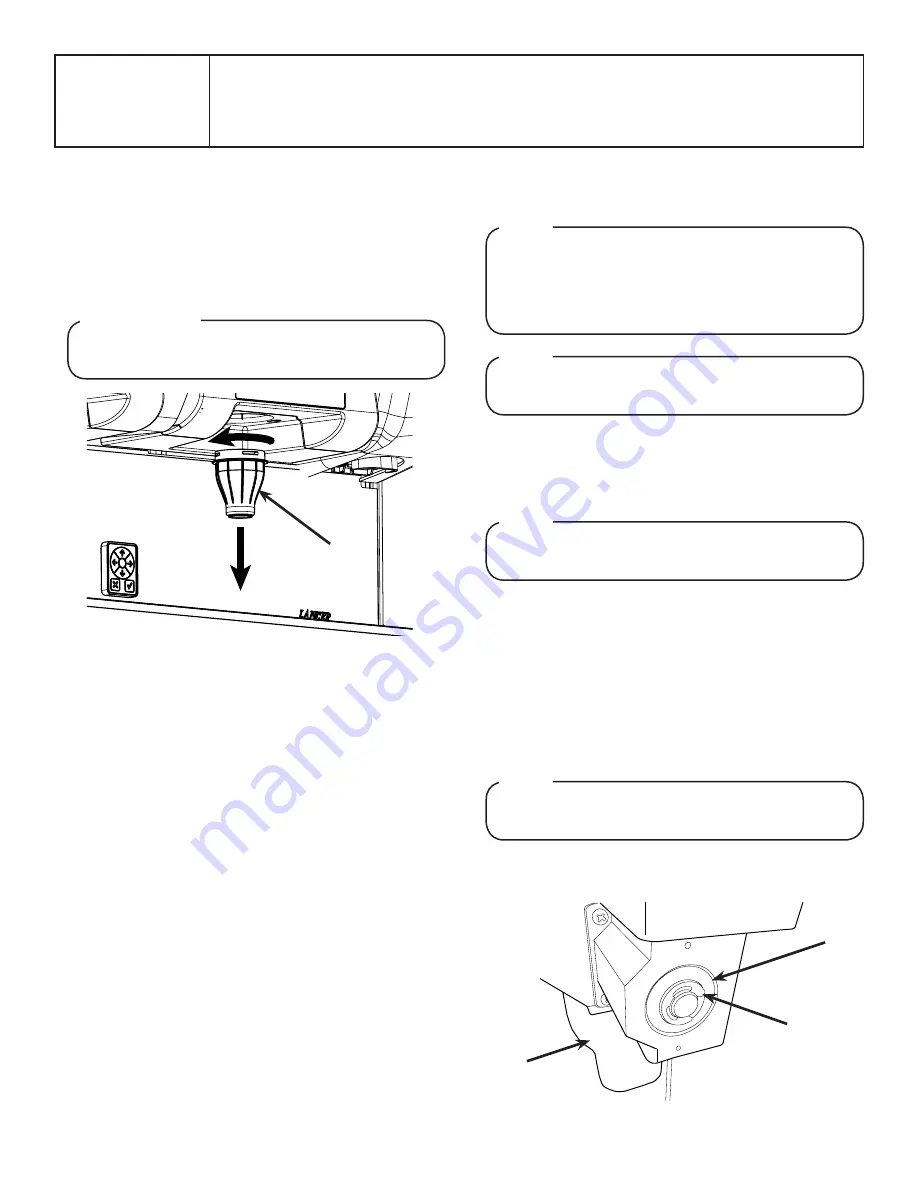
15
Every Six Months
•
Clean the syrup lines as specified by the section “Cleaning and Sanitizing Syrup Lines - Bag in Box” on
• Pull out unit (if applicable) and clean behind and underneath. Check for any loose components or
noises.
Cleaning & Sanitizing Nozzles
1. Prepare the nozzle sanitizing solution as described on the
previous page.
2. Turn the left and right key switches to deactivate valves and
avoid accidental dispense while the nozzles are exposed.
3. Remove the outer nozzle by twisting clockwise and pulling
downward.
DO NOT
attempt to activate any valves while the outer
nozzle is removed.
!
ATTENTION
A
A. Nozzle
4. Using the nozzle brush provided in the installation kit and the
cleaning solution described on page 18, clean the outer
nozzle of any residual syrup.
5. Rinse the outer nozzle with clean, potable water then soak in
the nozzle sanitizing solution prepared in step 1.
6. While the outer nozzle is in the sanitizing solution, using the
nozzle brush, dip the brush in the nozzle sanitizing solution
and thoroughly brush the bottom of the inner nozzle body.
7. Rinse the brush in warm 90° – 110°F (32.2°– 43.3°C), clean
potable water and brush the bottom of the inner nozzle body
once more
WITHOUT
the sanitizing solution.
8.
After the outer nozzle has soaked for fifteen (15) minutes,
rinse in warm 90° – 110°F (32.2°– 43.3°C), clean potable
water for a minimum of twenty (20) seconds ensuring all
surfaces of the nozzle have been thoroughly rinsed.
9. Allow outer nozzle to air dry (to expedite drying, forced
convection is recommended).
10. Reinstall the outer nozzle to the unit.
11.
Repeat Steps 3 - 10 for the second nozzle.
12. Return the left and right key switches to active valves.
Cleaning & Sanitizing Ice Bin, Auger, and
Ice Chute
1. Disconnect power to the dispenser
2. Remove the Merchandiser and Top Cover.
3. Remove Ice Chute Lever, then remove Splash Plate
Assembly by lifting it up and out from the dispenser face.
Refer to the Automatic Agitation Warning on the first
page of this manual.
NOTE
It is recommended to perform this procedure monthly,
or more often if desired. Use the cleaning solution
described on page 14. An alternate solution of one part
water to one part vinegar may be used to remove
water spots and calcium deposits.
NOTE
Always remove the ice chute lever before removing the
splash plate.
NOTE
4. Remove or melt out any remaining ice from the ice bin.
5. Disconnect the two (2) lower, horizontal LED light bars and
remove from unit.
6.
Disconnect vertical LED light bar, next to flavor injector
nozzle, from the junction box and remove from unit.
7. Repeat previous step for second light bar on opposite side of
the unit.
8.
Rotate the flavor injector nozzle 90° to disconnect from
bracket.
DO NOT
disconnect flavor lines from nozzle, when
removing from bracket.
NOTE
A
B
C
A. Auger Motor Shaft
B. “C” Clip
C. Ice Chute
9. Use a screwdriver to remove the Auger Motor shaft cover.
10. Remove the “C” clip from the Auger Motor Shaft.