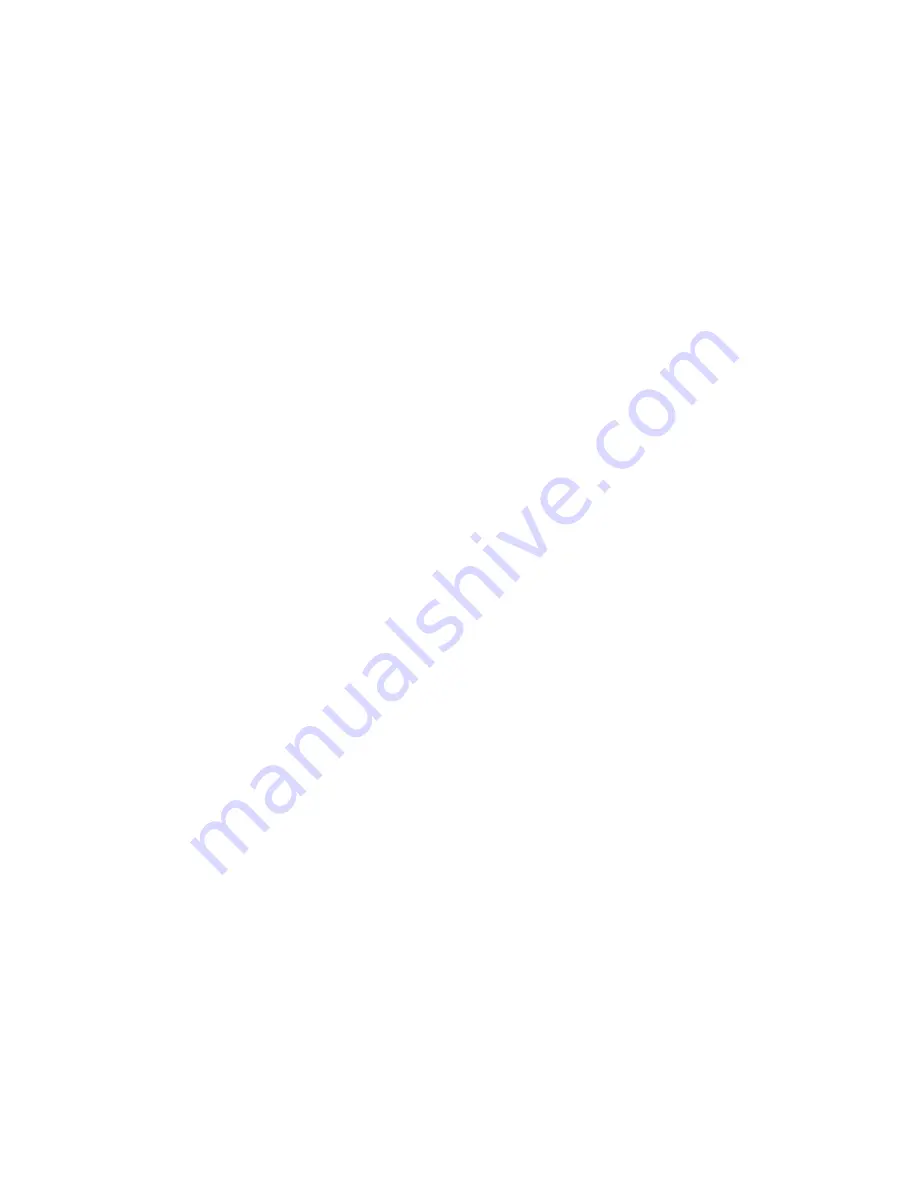
B. Mark both ends of product and water lines and route to dispenser. Flush lines to be sure each
is clean. Failure to do so may result in clogging of valve(s), resulting in improper operation.
Connect lines to dispenser and secure using Oetiker clamps.
C. Route drain tube to dispenser.
D. Connect drain tube to drip tray and install on dispenser.
E. Turn on water supply.
F. Open all dispenser valves until air is bled from system.
G. Actuate valve until a smooth flow of water is obtained.
H. Check for leaks.
I.
Connect free ends of product lines to proper tanks or bag-in-box.
J. Check for syrup leaks.
K. Adust the water flow.
L. Install splash plate on dispenser.
M. Install cup rest on dispenser.
N. Replace bonnet on dispenser.
2. SCHEDULED MAINTENANCE
2.1
DAILY
A. Remove the nozzle and diffuser from each valve and rinse well in warm water.
Do
NOT
use
soap or detergent. This will cause foaming and off taste in finished product.
B. Remove the cup rest and wash in warm soapy water.
C. Pour warm soapy water into the drip tray and wipe with a clean cloth.
D. With a clean cloth and warm water, wipe off all of the unit's exterior surfaces.
DO NOT USE
ABRASIVE SOAPS OR STRONG DETERGENTS.
E. Replace the cup rest, valve diffusers, and valve nozzles.
2.2
WEEKLY
A. Taste each product for off tastes and/or brix changes.
B. Remove the bonnet and check the level of water in the water bath. Replenish as required, and
replace the bonnet.
2.3
MONTHLY
A. Unplug the dispenser from power source.
B. Remove the bonnet and clean the dirt from the condenser using a soft brush.
C. Replace the bonnet and plug in the unit.
2.4
EVERY SIX MONTHS
A. Clean and sanitize the unit using the appropriate procedures outlined in Section 3 of this
manual.
2.5
YEARLY
A
Clean water bath interior, including evaporator coils and refrigeration components.
B. Clean the entire exterior of the unit.
C. Sanitize syrup lines.
3. DISPENSER CLEANING AND SANITIZING
3.1
AMBIENT PROCESS
A. The ambient process is the most common method for cleaning and sanitizing dispenser
equipment. The detergent should be caustic-based and the sanitizer should be low pH (7.0)
chloride solution.
B. Disconnect syrup containers and remove product from tubing by purging with carbon dioxide.
C. Rinse the lines and fittings with clean, room temperature water to remove all traces of residual
product.
D. Fill lines with a caustic-based (low-sudsing, non-perfumed, and easily rinsed) detergent solution.
The solution should be prepared in accordance with the manufacturer’s recommendations, but
should be at least two (2) percent sodium hydroxide. Make sure the lines are completely filled
and allow to stand for at least ten (10) minutes.
E. Flush the detergent solution from the lines with clean water. Continue rinsing until testing with
3
Содержание 500 Series
Страница 14: ...13 NOTES...