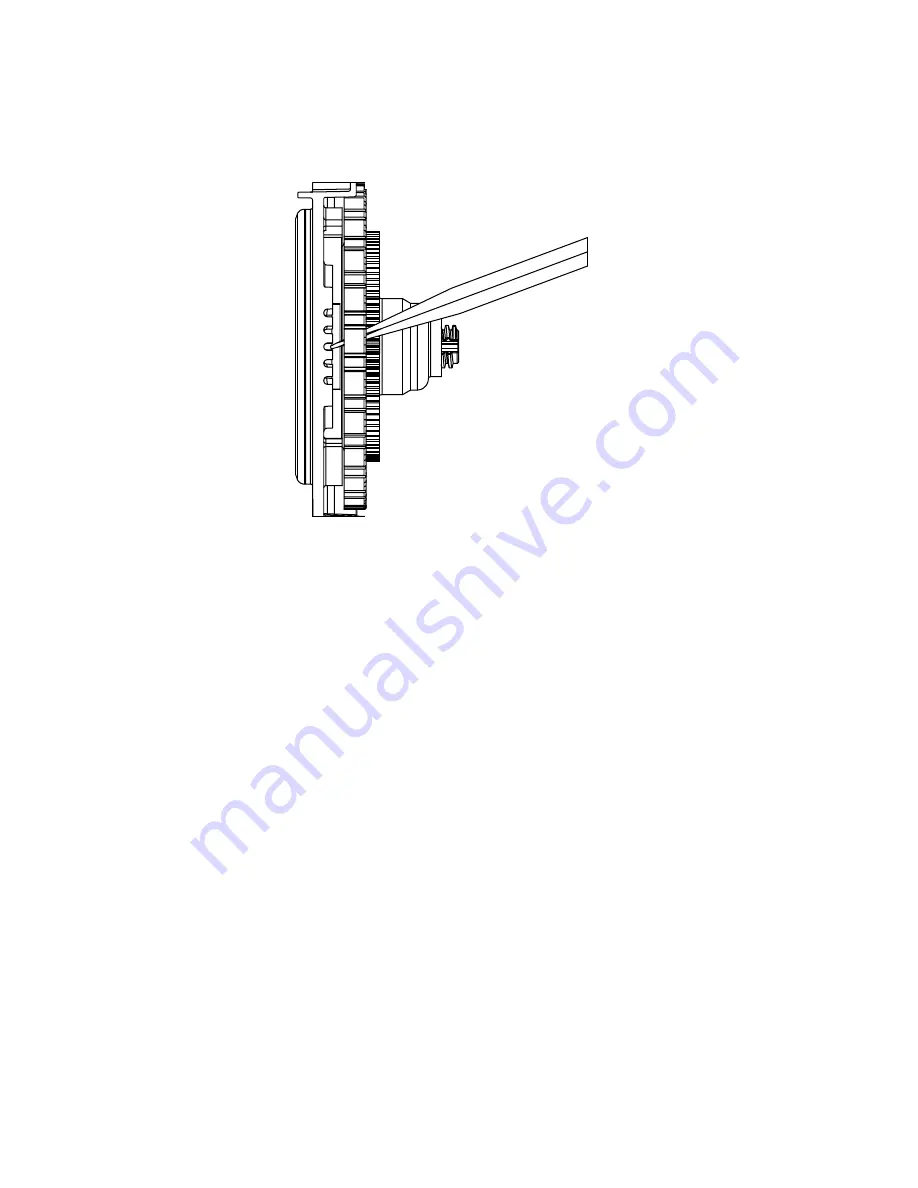
PAGE 25
DRIVE CAP ASSEMBLY, MAIN PISTON AND REGENERANT PISTON:
The drive assembly must be removed to access the drive cap assembly. The drive cap assembly must be removed to access the
piston(s). The drive cap assembly is threaded into the control valve body and seals with an o-ring. To remove the drive cap assembly
use the special plastic wrench or insert a ¼” to ½” flat blade screwdriver into one of the slots around the top 2” of the drive cap
assembly so it engages the notches molded into the drive back plate around the top 2” of the piston cavity. See below. The notches are
visible through the holes. Lever the screwdriver so the drive cap assembly turns counter clockwise. Once loosened unscrew the drive
cap assembly by hand and pull straight out.
The drive cap assembly contains the drive cap, the main drive gear, drive cap spline, piston rod and various other parts that should not
be dissembled in the field. The only replaceable part on the drive cap assembly is the o-ring. Attached to the drive cap assembly is the
main piston and if a regenerant is used, a regenerant piston.
The regenerant piston (the small diameter one behind the main piston) is removed from the main piston by pressing sideways and
unsnapping it from its latch. Chemically clean in dilute sodium bisulfite or vinegar, or replace the regenerant piston if needed. To remove
the main piston fully extend the piston rod and then unsnap the main piston from its latch by pressing on the side with the number.
Chemically clean in dilute sodium bisulfite or vinegar, or replace the main piston.
Reattach the main piston to the drive cap assembly. Reattach the regenerant piston (if needed) to the main piston. Reinsert the drive
cap assembly and piston into the spacer stack assembly and hand tighten the drive cap assembly. Continue to tighten the drive cap
assembly using a screwdriver as a ratchet until the black o-ring on the spacer stack assembly is no longer visible through the drain port.
Excessive force can break the notches molded into the drive back plate. Make certain that the main drive gear still turns freely.
The exact position of the piston is not important as long as the main drive gear turns freely. Reattach the drive assembly to the control
valve and connect all plugs. After completing any valve maintenance involving the drive assembly or the drive cap assembly and
pistons unplug power source jack from the printed circuit board (black wire) and plug back in or press and hold NEXT and REGEN
buttons for 3 seconds.
This resets the electronics and establishes the service piston position. The display should flash all wording, then flash the software
version and then reset the valve to the service position.
REFILL FLOW CONTROL ASSEMBLY:
To clean or replace the refill flow control, pull out the elbow-locking clip and then pull straight up on the elbow. Replace the elbow
locking clip in the slot so that it is not misplaced. Twist to remove the white flow control retainer. The flow control can be removed by
prying upward through the side slots of the retainer with a small flat blade screwdriver.
Chemically clean the flow control or the white flow control retainer using dilute sodium bisulfite or vinegar. Do not use a wire brush. If
necessary, replace the flow control, o-ring on the flow control retainer, or the o-ring on the elbow.
Reseat the flow control so the rounded end is visible in the flow control. Reseat the white flow control retainer by pushing the retainer
into the elbow until the o-ring seats. Remove locking clip, push down on elbow to reseat and insert locking clip.
Do not use Vaseline, oils, or other unacceptable lubricants on o-rings. A silicone lubricant may be used on the o-ring on the elbow or the
white retainer.