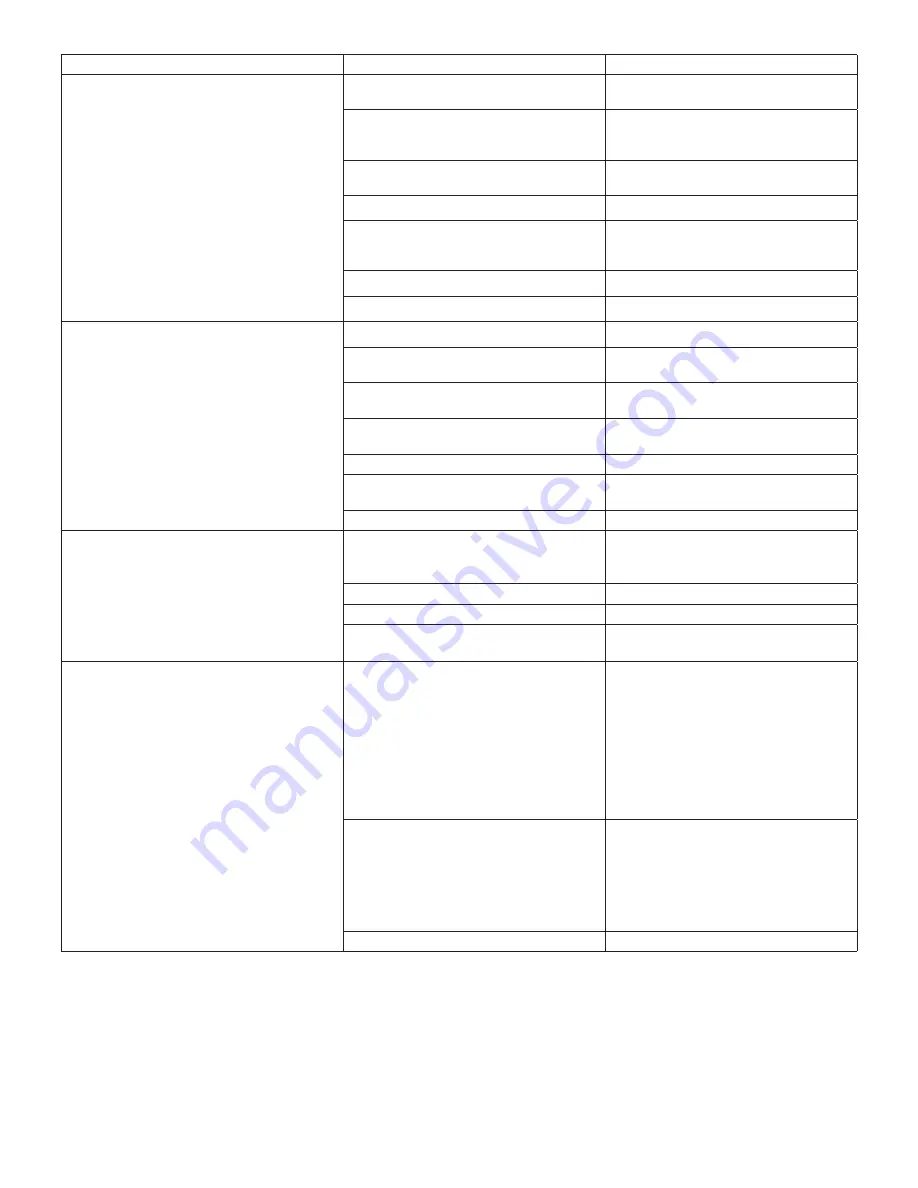
PAGE 28
Problem
Possible Cause
Solution
7. Control valve does not backwash
automatically but
does
when the
REGEN
button
is depressed and held.
a. Bypass valve in bypass position optional
a. Turn bypass handles to place bypass in
service position
b. Meter is not connected to meter
connection on PC Board if meter is
installed
b. Connect meter to three pin connection
labeled METER on PC Board
c. Restricted/ stalled meter turbine if meter is
installed
c. Remove meter and check for rotation or
foreign material
d. Incorrect programming
d. Check for programming error
e. Meter wire not installed securely into three
pin connector if meter is installed
e. Verify meter cable wires are installed
securely into three pin connector
labeled METER
f. Defective meter if installed
f. Replace meter
g. Defective PC Board
g. Replace PC Board
8. Untreated water is being delivered
a. Bypass valve is open or faulty
a. Fully close bypass valve or replace
b. Media is exhausted due to high water
usage
b. Check program settings or diagnostics
for abnormal water usage
c. Meter not registering if installed
c. Remove meter and check for rotation or
foreign material
d. Water quality fluctuation
d. Test water and adjust program values
accordingly
e. Damaged seal/stack assembly
e. Replace seal/stack assembly
f. Control valve body type and piston type
mix matched
f. Verify proper control valve body type
and piston type match
g. Fouled media bed
g. Replace media bed
9. Water running to drain
a. Power outage during regeneration
a. Upon power being restored control
will finish the remaining regeneration
time. Reset time of day
b. Damaged seal/ stack assembly
b. Replace seal/ stack assembly
c. Piston assembly failure
c. Replace piston assembly
d. Drive cap assembly not tightened in
properly
d. Re-tighten the drive cap assembly
10. Error – 101 = Control unable to sense motor
movement
a. Motor not inserted full to engage pinion,
motor wires broken or disconnected
a. Disconnect power, make sure motor is
fully engaged, check for broken wires,
make sure two pin connector on motor
is connected to the two pin connection
on the PC Board labeled MOTOR.
Press
NEXT
and
REGEN
buttons for
3 seconds to resynchronize software
with piston position or disconnect
power supply from PC Board for 5
seconds and then reconnect.
b. PC Board not properly snapped into drive
bracket
b. Properly snap PC Board into drive
bracket and then Press
NEXT
and
REGEN
buttons for 3 seconds to
resynchronize software with piston
position or disconnect power supply
from PC Board for 5 seconds and then
reconnect.
c. Missing reduction gears
c. Replace missing gears
Содержание X FACTOR LX15 Series
Страница 31: ...PAGE 31 NOTES ...