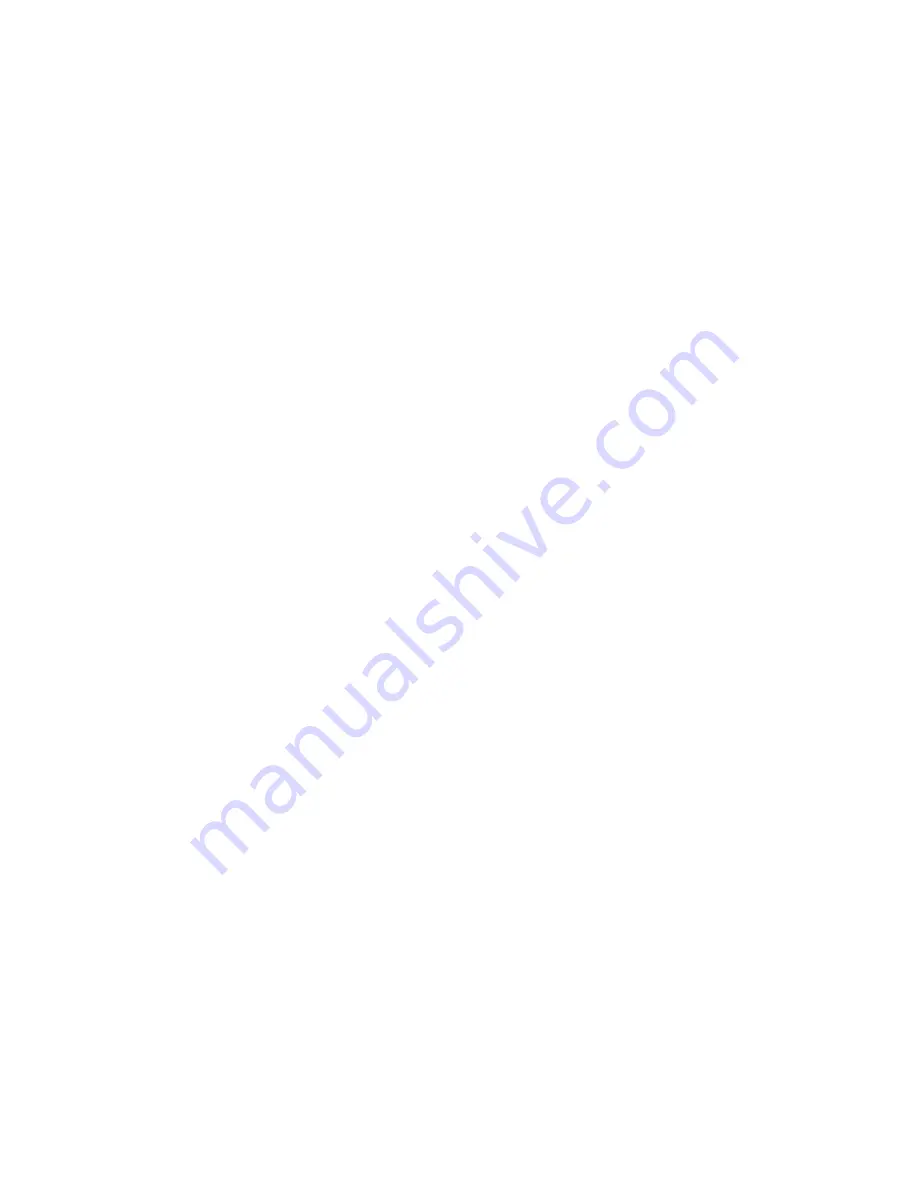
PAGE 10
INJECTOR CAP, SCREEN, INJECTOR PLUG AND INJECTOR:
The screen, injector and/or injector plug(s) are installed under the injector cap in an easy to access location on top of the
valve. The injector cap contains four slots so no water accumulates in the cap. The injector cap is designed to be hand
tightened.
Under the injector cap there is an easy to clean removable screen to prevent fouling of the injector. There are two holes
under the injector cap labeled “DN” and “UP”. The holes will be filled with a plug or an injector.
The plug (Order # V3010-1Z) prevents water from traveling a certain pathway. The injector lets water pass through the
pathway. The self-priming injector increases the velocity of the water, creating a zone of negative pressure that draws in
the concentrated liquid regenerant, such as sodium chloride (brine), potassium permanganate, etc. The regenerant blends
with the stream of water, which passes through the media to regenerate the bed.
The injector provides a consistent regenerant/water mixture ratio over the entire operating pressure range of the control
valve. The injector provides good performance in a variety of applications, which may involve elevated drain lines and
long regenerant draw lengths. Injectors are chosen by knowing the type, amount, and regenerant flow rate for a particular
type of media. Guidelines can be found in the media manufacturer’s literature. The color coded injectors give different
regenerant draw, slow rinse and total flow rates over the pressure range.
NOTE: It is not recommended to field convert valves from upflow to downflow and vice versa. Separate areas in the valve
supply water to the injector for upflow and downflow valves.
REFILL FLOW CONTROL ASSEMBLY OR REFILL PORT PLUG:
The refill flow control assembly consists of a refill flow elbow, refill flow control retainer assembly, refill flow control,
polytube insert and nut assembly. The refill flow control retainer fits in the refill elbow. The refill flow control retainer
houses the refill flow control which controls the flow rate when the regenerant tank is being refilled. The refill flow control
is a flexible washer-like part with a small orifice and a precision molded contour that delivers a steady 0.5 gpm regenerant
tank refill rate at varying inlet pressures. Refill is accomplished with treated water.
The refill flow control assembly is installed in an easy to access refill elbow located on top of the control valve. The refill
flow control assembly is attached to the control valve with a locking clip. The locking clip allows the elbow to rotate 270
degrees so the outlet can be orientated towards the regenerant tank.
The control valve has a standard refill elbow to which a 3/8” flexible tube can be connected.
WATER METER:
The water meter is installed on the outlet side of the control valve. The water meter uses a turbine to measure gallons
of treated water. The turbine rotates with the flow of water and reports its rate of rotation through Hall effect
2
circuitry to
the printed circuit (PC) board. This rotation permits the PC board to record the total volume of treated water and the flow
rate. The small centrally located magnet is shielded from water, which substantially reduces iron-fouling problems with the
turbine.
THIS WATER METER SHOULD NOT BE USED AS THE PRIMARY MONITORING DEVICE FOR CRITICAL OR
HEALTH EFFECT APPLICATIONS.
OPERATING PRESSURES: 20 PSI MINIMUM / 125 PSI MAXIMUM • OPERATING TEMPERATURES: 40°F MINIMUM /
110°F MAXIMUM
The turbine is accurate to within ± 5% over a wide operating flow rate range (0.25 gpm (0.95 lpm) up to control valve
maximums) and has a very low pressure drop. Water used for regeneration is not metered. If the control valve is set
to prefill the regenerant, water used between the prefill cycle up to the start of the regeneration cycle is metered. If the
control valve is in regeneration mode (e.g. a backwash cycle) and there is a water demand, that water usage is not
metered.
When facing the front of the control valve, the water meter is positioned on the left-hand side of the control valve. Allow
sufficient clearance to clean and repair the water meter without disconnecting the plumbing or disassembling any other
parts of the control valve.
Control valves can be ordered with a meter plug (i.e. no electronics or turbine) rather than a water meter if desired.
Control valves without meters should only be set up for time clock operation (i.e. no water meter, no demand-initiated
regeneration). Control valves with water meters provide a wider variety of useful information.
Do not lubricate the
turbine shaft. The turbine shaft bearings are pre-lubricated. Do not use Vaseline, oils or other unacceptable lubricants on
the o-ring. A silicone may be used on the black o-ring. Snap the turbine on the shaft and reinsert the water meter into the
side slot. Hand tighten the nut. Do not use a pipe wrench to tighten nut.