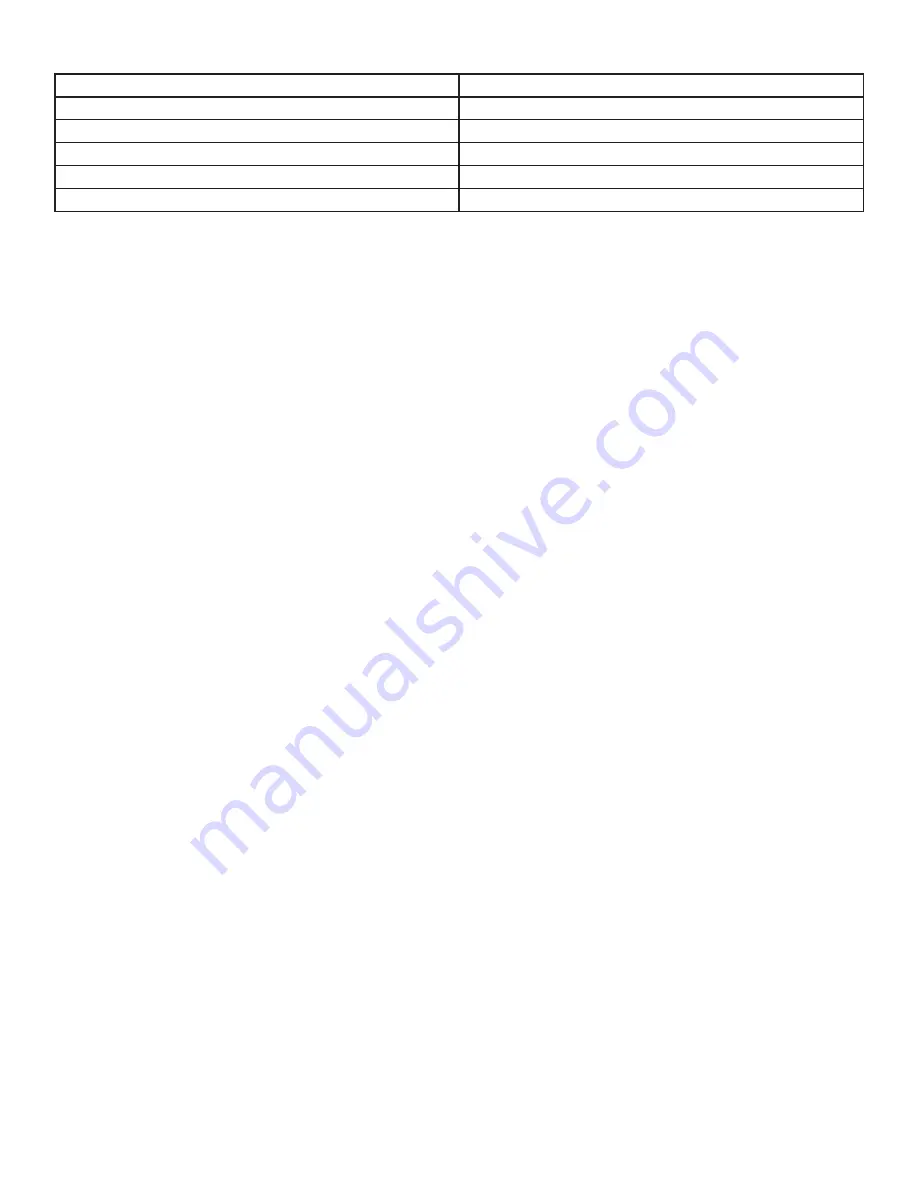
PAGE 2
OPERATING PARAMETERS
Minimum / Maximum Operating Pressures
20 psi (138 kPa) - 125 psi (862 kPa)
Minimum / Maximum Operating Temperatures
40°F (4°C) - 110°F (43°C)
Supply Voltage/ Frequency
120V AC/ 60 Hz Other Options Available
Power Consumption
9.5 W
Output Voltage
12V AC
Output Current
500 mA
GENERAL WARNINGS
The control valve, fittings and/or bypass are designed to accommodate minor plumbing misalignments but are not designed
to support the weight of a system or the plumbing.
Do not use Vaseline, oils, other hydrocarbon lubrications or spray silicone anywhere. A silicone lubricant may be used on
black o-rings but is not necessary.
Avoid any type of lubricants, including silicone, on red or clear lip seals.
The nuts and caps are designed to be unscrewed or tightened by hand or with the special plastic wrench (P/N V3193). If
necessary, pliers can be used to unscrew the nut or cap. Do not use a pipe wrench to tighten or loosen nuts or caps. Do not
place screwdriver in slots on caps and/or tap with hammer.
Do not use pipe dope or any other sealant on threads. Teflon tape must be used on the threads of the 1” NPT elbow or the
1/4” NPT connection and on the threads for the drain line connection. Teflon tape is not necessary on the nut connection or
caps because of o-ring seals.
After completing any valve maintenance involving the drive assembly and pistons, press and hold
NEXT
and
REGEN
button for three seconds or unplug power source jack from printed circuit board (black wire) and plug back in. This resets
the electronics and establishes the service piston position. The display should flash all wording , then flash software version
(e.g. 220.1) and then reset the valve to the service position.
All plumbing should be done in accordance with local plumbing codes. The pipe size of the drain line should be a minimum
of 1/2”. Backwash flow rates in excess of 7 gpm or length in excess of 20’ require 3/4” drain line.
Solder joints near the drain must be done prior to connecting the drain line flow control fitting. Leave at least 6” between the
drain line control fitting and solder joints when soldering pipes that are connected on the drain line control fitting.
Failure to
do this could cause interior damage to the drain line flow control fitting.
When assembling the installation fitting package(P/N V3007) to the inlet and outlet (see Page 11), connect the fitting to the
plumbing system first and then attach the nut, split ring and o-ring. Heat from soldering or solvent cements may damage the
nut, split ring or o-ring. Solder joints should be cool and solvent cements should be set before installing the nut, split ring and
o-ring.
Avoid getting primer and solvent cement on any part of the o-rings, split rings, bypass valve or control valve.
Plug into an electrical outlet.
NOTE:
All electrical connections must be connected according to local codes. (Be certain the
outlet is uninterrupted.) Install grounding strap on metal pipes.
INSTALLATION
Place softener in desired location close to water supply inlet, after pressure tank, and near a source for waste water, (utility
sink, floor drain or sewer line). A 115/120V, 60 Hz uninterrupted outlet is required. Keep softener far enough away from walls
and other obstructions to allow enough room for servicing the unit. All sillcocks and similar fixtures that will use untreated
water must have their pipes connected to the hard water side of the softener. A bypass valve (optional accessory) should
be installed so that water will be available if it should be necessary to shut off the pressure in order to service the softener.
The cabinet tank or mineral tank must be reasonably level and solidly in place. Prior to beginning work to the system, make
sure that water pressure is shut off at the incoming water supply and that several water spigots are open to provide sufficient
venting for drainage of that system.
Arrows are molded into the control valve to show the direction of the flow.
OPTIONAL BYPASS VALVE:
The bypass valve easily connects to the control valve body using nuts that only require hand
tightening. Install with red knobs in the upward position. Press end of bypass valve with o-rings into valve. Hand tighten nuts.
Place into
BYPASS OPERATION (figure 1 page 3).
Avoid getting primer and solvent cement on any part of the o-rings or split rings, bypass valve or control valve.
DO NOT
use
pipe dope or any other sealant on threads. Teflon tape is not necessary on the caps because of o-ring seals. Do not use
Vaseline or other unacceptable lubricants on o-rings. A silicone lubricant may be used on black o-rings.
DRAIN LINE:
The 3/4” drain line elbow accommodates 5/8” poly tube or 3/4” NPT drain line connections. The nut and poly
tube insert for the 3/4” drain line elbow is designed for use with flexible poly tube only. The drain line elbow can be rotated
so the outlet can be oriented toward the nearest drain.