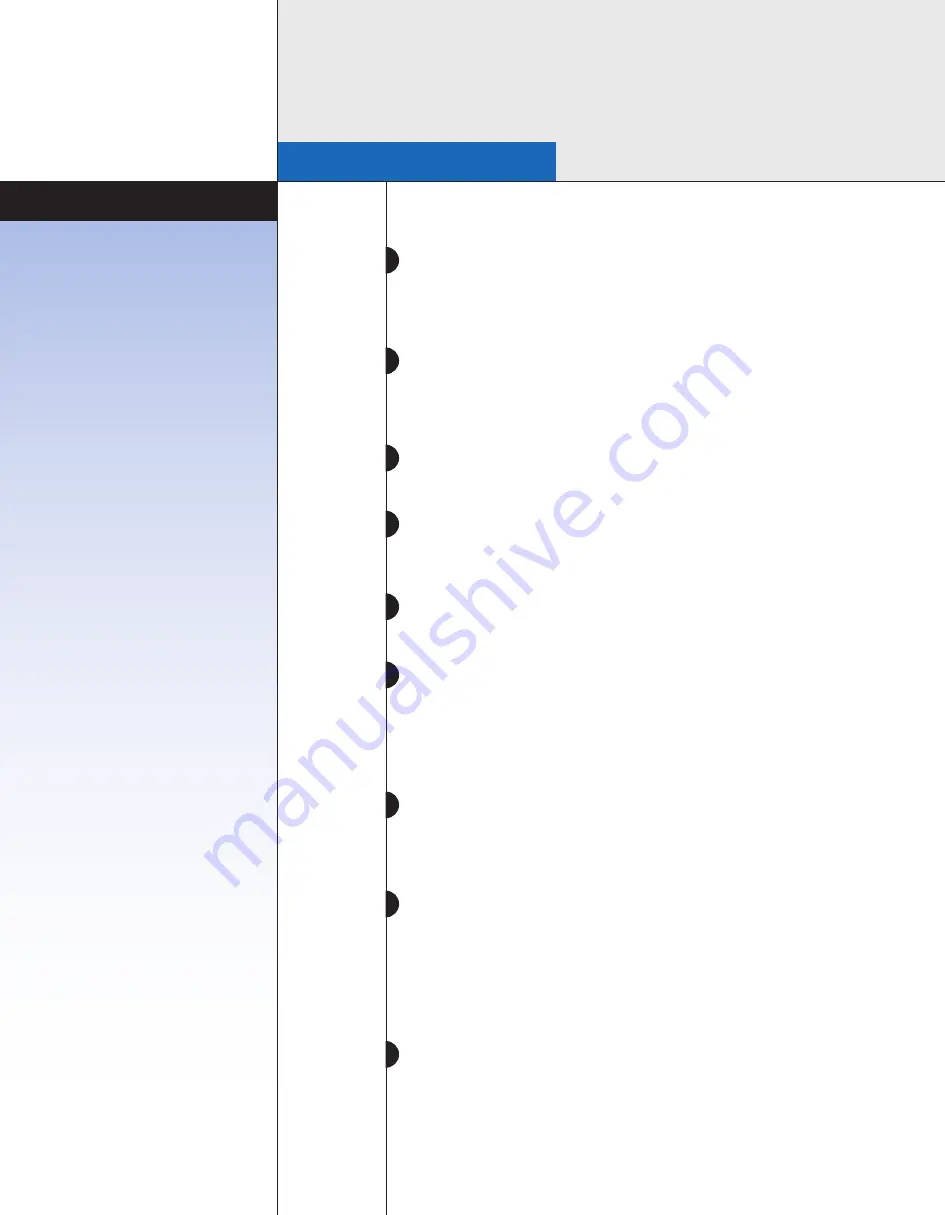
LAKOS JPX Separators are shipped on skids or in
wooden crates. Support legs (when applicable)
are detached for shipping. A large ring, located
on the unit’s side or upper chamber, is provided
for hoisting as necessary.
A suitable foundation is necessary to
accommodate the LAKOS Separator’s weight
including liquid (see data, page 3). Anchor bolts
are recommended in the base of the legs (low
profile) or skirt (vertical profile).
Prior to installation, inspect the
inlet/outlet/purge connections for foreign
objects incurred during shipping/storage.
Inlet/outlet pipe connections to the LAKOS
Separator should be a straight run of at least five
pipe diameters to minimize turbulence and
enhance performance.
Proper purge hardware and/or solids-handling
equipment is required to flush separated solids
from the separator (see details, page 2).
All LAKOS Separators operate within a prescribed
flow range (see data, page 3). Pipe size is not
a factor in model selection. Use appropriate
hardware to match the inlet/outlet size.
Grooved couplings are not included with the
separator. Optional flanged connections are
available upon request.
Inlet pressure to the LAKOS Separator must be
at least equal to or greater than the anticipated
pressure loss through the separator (see pressure
loss chart, page 3) plus 15 psi (1 bar) plus
whatever downstream pressure is required.
Pressure gauges (provided as standard, with
petcock valves) are required at both the inlet
and outlet of the separator in order to monitor
pressure loss and proper system flow (see “Flow
vs. Pressure Loss” chart, page 3). If separator
operates with an open discharge, a valve should
be installed to create a back pressure of at least
5 psi (.3 bar).
Winterizing is important if the LAKOS Separator
is to remain idle in freezing temperatures. Drain
liquid as necessary to avoid expansion of water
to ice and related damages.
Maintenance/Purging
Installation Instructions
1. LAKOS JPX Separators must be
purged regularly to remove the
separated solids from the
temporary collection chamber.
2. All purge hardware should be
installed prior to any elbows or
turns in the purge piping. Avoid
“uphill” purging, which can clog
purge piping and hinder effective
solids evacuation.
3. For best results, purging is
recommended while the LAKOS
Separator is in operation,
utilizing system pressure to
enhance solids evacuation.
4. LAKOS provides a full selection
of rugged, durable automatic
purging and solids-handling systems
to optimize the performance of
your separation system.
CAUTION: Economy-type valves
typically fail prematurely in the
harsh/abrasive environment of
solids purging.
5. Be sure to install a manual
isolation valve (provided with
LAKOS AutoPurge kits) prior to
the automatic valve (available
from LAKOS at additional cost)
in order to facilitate servicing
of the automatic valve without
system shutdown.
6. Internal Access Feature:
To inspect or clear an unusual
blockage in the upper or lower
chamber, interrupt flow to the
LAKOS Separator and relieve
pressure (via the purge valve).
For upper chamber access,remove
the spool from the separator’s
outlet (or, if no spool has been
installed, disconnect and remove
piping on the outlet) to make space
for removing the separator’s upper
section. Disconnect the rigid
coupling or flange and carefully
pull out the separator’s vortex
outlet assembly. Inspect or clean
the inlet chamber as necessary.
Lubricate the coupling’s seal
before re-installing the vortex
assembly. Re-install piping and
gaskets as necessary.
1
2
3
4
5
6
7
8
9
Page 4