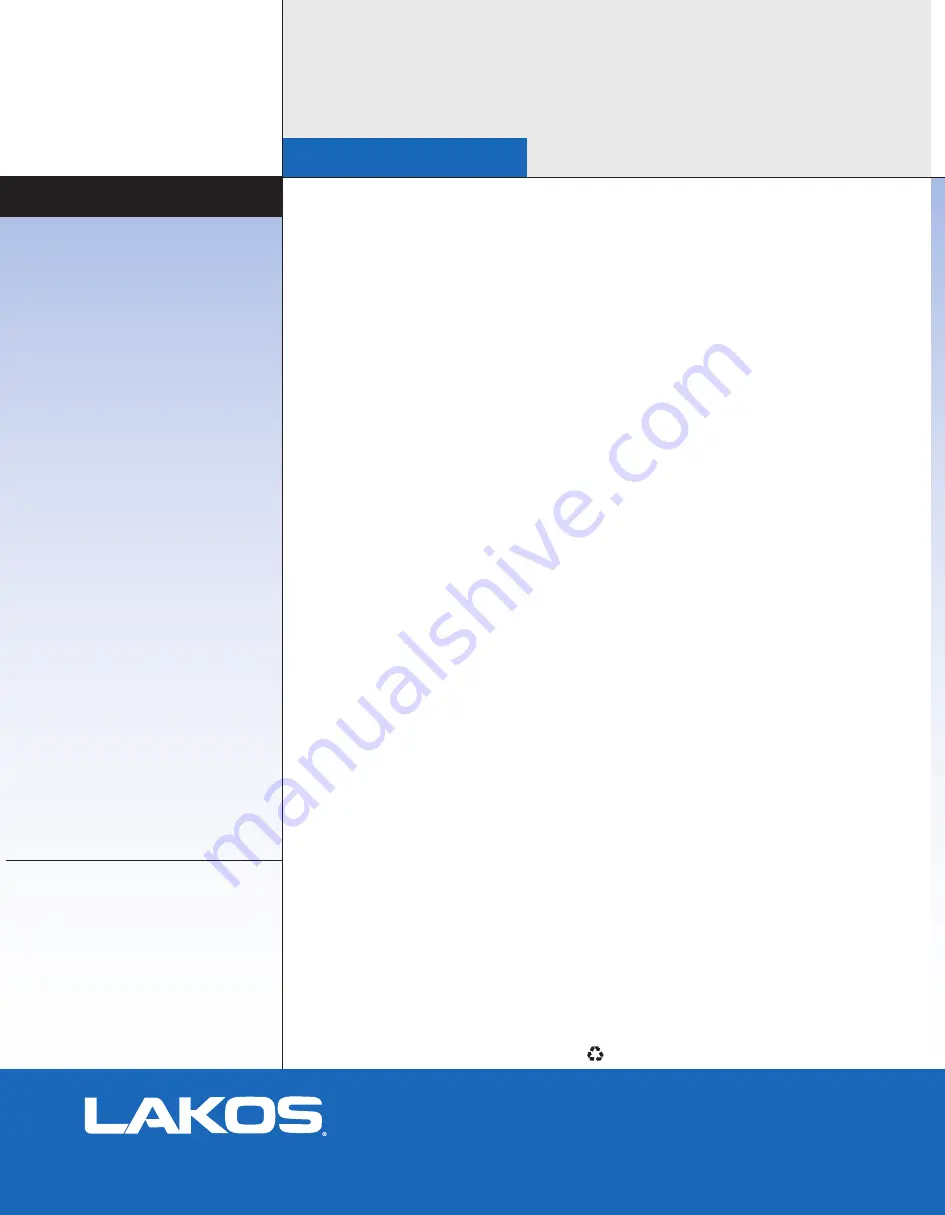
Sample Specifications
All products manufactured and marketed by
this corporation are warranted to be free of
defects in material or workmanship for a
period of at least one year from date of
delivery. Extended warranty coverage
applies as follows:
All LAKOS Separators: Five year warranty
All other components: 12 months from date
of installation; if installed 6 months or more
after ship date, warranty shall be a
maximum of 18 months from ship date.
If a fault develops, notify us, giving a
complete description of the alleged
malfunction. Include the model number(s),
date of delivery and operating conditions of
subject product(s). We will subsequently
review this information and, at our option,
supply you with either servicing data or
shipping instruction and returned materials
authorization. Upon prepaid receipt of subject
product(s) at the instructed destination, we
will then either repair or replace such
product(s), at our option, and if determined to
be a warranted defect, we will perform such
necessary product repairs or replace such
product(s) at our expense.
This limited warranty does not cover any
products, damages or injuries resulting from
misuse, neglect, normal expected wear,
chemically-caused corrosion, improper
installation or operation contrary to factory
recommendation. Nor does it cover
equipment that has been modified, tampered
with or altered without authorization.
No other extended liabilities are stated or
implied and this warranty in no event covers
incidental or consequential damages,
injuries or costs resulting from any such
defective product(s).
Limited Warranty
1365 North Clovis Avenue
Fresno, California 93727 USA
Telephone: (559) 255-1601
FAX: (559) 255-8093
Toll Free: (800) 344-7205
(USA, Mexico & Canada)
Internet: www.lakos.com
E-mail: [email protected]
Printed on recycled paper
LS-632G (Rev. 02/06)
Liquid • Solids Separation Systems
Separator Type & Performance
The removal of specific unwanted solids from a pumped/pressurized
fluid flow system shall be accomplished with a centrifugal-action
vortex separator. Solids removal efficiency is principally predicated
on the difference in specific gravity between the liquid and the
solids. Fluid viscosity must be 100 SSU or less.
In a single pass through the separator, given solids with a specific
gravity of 2.6 and water at 1.0, performance is predictably 98% of
74 microns and larger. Additionally, particles finer in size, heavier
by specific gravity and some lighter by specific gravity will also be
removed, resulting in an appreciable aggregate removal of particles
(up to 75%) as fine as 5 microns.
In a recirculating system, 98% performance is predictable to as fine
as 40 microns (given solids with a specific gravity of 2.6), with
correspondingly higher aggregate performance percentages (up to
90%) of solids as fine as 5 microns.
Performance Requirement
Separator performance must be supported by published
independent test results from a recognized and identified test
agency. Standard test protocol of upstream injection, downstream
capture and separator purge recovery is allowed with 50-200 mesh
particles to enable effective, repeatable results. Single-pass test
performance must not be less than 95% removal. Model tested must
be of the same flow-design series as specified unit.
Separator Design & Function
A tangential inlet and mutually tangential internal accelerating
slots shall be employed to promote the proper velocity necessary
for the removal of the separable solids. The internal accelerating
slots shall be spiral-cut (Swirlex) for optimum flow transfer, laminar
action and particle influence into the separation barrel. The
separator's internal vortex shall allow this process to occur without
wear to the accelerating slots.
Separated particle matter shall spiral downward along the
perimeter of the inner separation barrel, in a manner that does not
promote wear of the separation barrel, and into the solids
collection chamber, located below the vortex deflector stool.
To insure maximum particle removal characteristics, the separator
shall incorporate a vortex-induced pressure relief line (Vortube),
drawing specific pressure and fluid from the separator's solids
collection chamber via the outlet flow's vortex/venturi effect, thereby
efficiently encouraging solids into the collection chamber without
requiring a continuous underflow or excessive system fluid loss.
System fluid shall exit the separator by following the center vortex
in the separation barrel and spiral upward to the separator outlet.
Purging
(as a specified option)
Evacuation of separated solids shall be accomplished automatically,
employing a dedicated solid-state controller in a NEMA 4 housing.
Available for worldwide single-phase voltages of 24VAC to 250VAC.
Programming options to include a purge frequency range of every
60 seconds to every 23 hours, 59 minutes. Purge duration options
range from 2 seconds to 59 minutes, 59 seconds. Non-volatile
memory. Meets CSA requirements. This controller shall
automatically operate one of the following techniques:
Motorized Ball Valve
- A full-port, electrically-actuated valve shall
be programmed at appropriate intervals and duration in order to
efficiently and regularly purge solids from the separator's collection
chamber. Valve body shall be bronze (optional stainless steel also
available). Valve ball shall be stainless steel with teflon seat.
Valve size: ______
Pneumatic Pinch Valve
- Compressed air shall be provided to
actuate this full-port valve at appropriate intervals and duration in
order to efficiently and regularly purge solids from the separator's
collection chamber. System shall include a pressure regulator for
proper modulation of air pressure. Valve liner is natural gum rubber
(other liner materials available). Valve size: ______
Pneumatic Ball Valve
- A fail-safe valve shall be programmed at
appropriate intervals and duration in order to efficiently and
regularly purge solids from the separator's collection chamber. A
spring-control shall provide that this full-port valve closes in the
event that compressed air or electricity is interrupted. Valve body
shall be bronze (optional stainless steel also available). Valve ball
shall be stainless steel with teflon seat. Valve size: _______
Purge Liquid Concentrator
- A dual pneumatic pinch valve package
shall be employed in order to effectively minimize the fluid loss
when purging. The controller shall provide proper sequential valve
actuation at appropriate intervals and duration in order to
efficiently and regularly evacuate solids from the separator's
collection chamber. Liners for the pinch valves shall be natural gum
rubber (optional, at extra cost: neoprene, butyl, buna N and
hypalon also may be specified). System shall also include a pressure
regulator to modulate air pressure to the valves, a full-size sightglass for
inspection of solids accumulation during operation and a manual isolation
valve for servicing requirements. Valve size: ______
Solids Handling
(as a specified option)
An appropriate solids collection device shall be provided with the
separator, suitable for capturing solids and returning all excess purged
liquid to system use. Size and type of collection device shall be
determined according to the application requirements, selected from the
following options (or custom, as specified):
Solids Collection Drum
- In conjunction with the appropriate automatic
purge valve, this package shall be employed to capture and concentrate
separated solids (up to 90% solids by volume) from the separator directly
into a standard 55-gallon drum, returning excess purged liquid to system
use via an integral decant line on the drum shroud. Solids collection
capacity: 12,700 cubic inches (200 liters). Package includes two shrouds,
two shroud clamps, two drum carts for transporting the drums and a
manual liquid evacuation pump. Recommended option: A Purge Diffuser
shall be installed on the discharge of the automatic purge valve in order
to reduce the velocity of the purge flow and enhance the settling of
solids within the drum.
Solids Collection Hopper
- In conjunction with the appropriate
automatic purge valve, a one cubic yard (764 liter) hopper shall be
employed to capture and concentrate separated solids (up to 90% by
volume) from the separator, returning excess purged liquid to system use
via an integral decant line installed directly on the hopper. The hopper
shall feature a manually-actuated tilting mechanism for dumping
accumulated solids as necessary. Recommended option: A Purge Diffuser
shall be installed on the discharge of the automatic purge valve in order
to reduce the velocity of the purge flow and enhance the settling of
solids within the hopper.
Systemization
(as a specified option)
The separator and its accessories shall be packaged as a complete
system, with all componentry from a single source. In addition to the
equipment already specified, the system shall also include an
appropriate support frame for positioning the separator accurately and
effectively for solids purging/handling. Connection spool shall be provided.
If the specified purging technique is a pneumatic pinch valve: A spare pinch
valve liner shall also be included.
Separator Details
A. Inlet & outlet shall be grooved couplings, size: __________
B. Purge outlet shall be threaded with screw-on flange,
size: __________
C. The separator shall operate within a flow
range of:__________
D. Pressure loss shall be between 3-12 psi (.2 - .8 bar),
remaining constant, varying only when the flow
rate changes.
E. Included shall be pressure gauges with petcock valves
for both the inlet and outlet of the separator.
Separator Construction
The separator shall feature the following access capabilities
for either inspection or the removal of unusual solids/debris:
• An upper-chamber full-size grooved coupling (flange for JPX-2650
and larger), allowing complete access to the inlet chamber,
acceleration slots and internal separation barrel
• A hand-hole port at the collection chamber, with Neoprene gasket
(low flow rate models to feature full-size coupling at collection chamber)
• An inspection port, located at the lowest point of the upper chamber
The separator shall be of unishell construction with A-36, A-53B or
equivalent quality carbon steel, minimum thickness of .25 inches 6mm).
Maximum operating pressure shall be 150 psi (10.3 bar), unless
specified otherwise.
Paint coating shall be oil-based enamel, spray-on, royal blue.
As a specified option only: The separator shall be constructed in
accordance with the standards of the American Society of Mechanical
Engineers (ASME), Section VIII, Division 1 for pressure vessels.
Certification shall be confirmed with the registered "U-stamp" on the
body of the separator. Weld-on flanges also available.
Separator Source & Identification
The separator shall be manufactured by LAKOS Filtration Systems,
a division of Claude Laval Corporation in Fresno, California USA.
Specific model designation is: __________________