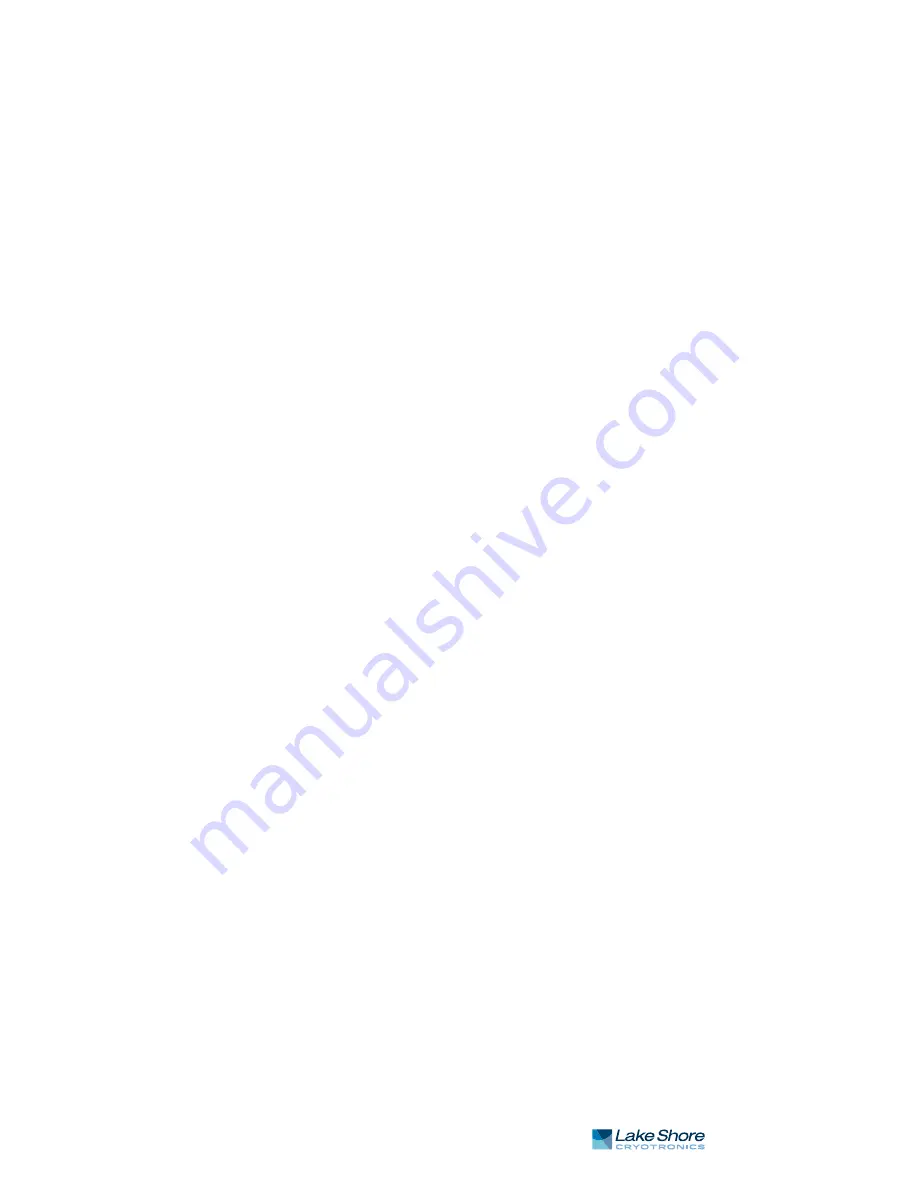
4.5.1 Heater Outputs
65
|
www.lakeshore.com
4.5.1.5.1 Control Input
For closed loop control (Closed Loop PID, Zone, Warm Up Supply) a control loop must
be created. A control loop consists of a control output for controlling the temperature,
and an input for feedback into the control algorithm. Use the Control Input parame-
ter to assign the control input sensor to the desired output.
In the Monitor Out mode the Control Input parameter is used to determine the source
of the output voltage. In the Open Loop mode, the Control Input parameter can be set
simply for convenience in order to easily access the associated output’s Manual Out-
put and Heater Range parameters using the Direct Operation keys. Refer to section
4.2.1.1 for details on Direct Operation keys.
Menu Navigation:
Output Setup
Q
Output
(1, 2, 3, or 4)
Q
Control Input
Q
(None, Input A, Input B,
Input C, Input D)
Default:
Output 1
Q
Control Input
Q
(Input A)
Output 2
Q
Control Input
Q
(Input B)
Output
(3, 4)
Q
Off
Interface Command:
HTRSET
4.5.1.5.2 Proportional (P)
The proportional parameter (also called gain) is the P part of the PID control equation.
It has a range of 0 to 1000 with a resolution of 0.1. The default value is 50. Enter a
value greater than 0 for P when using closed loop control.
To set P, first configure the front panel display to show the desired control loop infor-
mation, then use the
P
key on the front panel. A quick way to access the setting if the
control loop information is not already being displayed, is to press
A
,
B
,
C
, or
D
on the
front panel to temporarily display the control loop information while the new setting
is entered. Refer to section 4.3 for details on configuring the front panel display.
Menu Navigation:
P
Q
(0 to 1000)
Default: 50
Interface Command:
PID
4.5.1.5.3 Integral (I)
The integral parameter (also called reset) is the I part of the PID control equation. It
has a range of 0 to 1000 with a resolution of 0.1. The default value is 20. Setting I to 0
turns the reset function off. The I setting is related to seconds by:
I
setting
=1000/I
seconds
For example, a reset number setting of 20 corresponds to a time constant of 50 s. A
system will normally take several time constants to settle into the setpoint. The 50 s
time constant, if correct for the system being controlled, would result in a system that
stabilizes at a new setpoint in between 5 min and 10 min.
To set I, first configure the front panel display to show the desired control loop infor-
mation, then use the
I
key on the front panel. A quick way to access the setting if the
control loop information is not already being displayed is to press
A
,
B
,
C
, or
D
on the
front panel to temporarily display the control loop information while the new setting
is entered. Refer to section 4.3 for details on configuring the front panel display.
Menu Navigation:
I
Q
(0 to 1000)
Default: 20
Interface Command:
PID
Содержание 336
Страница 4: ...Model 336 Temperature Controller...
Страница 6: ...Model 336 Temperature Controller...
Страница 26: ...14 cHAPTER 1 Introduction Model 336 Temperature Controller...
Страница 54: ...42 cHAPTER 3 Installation Model 336 Temperature Controller...
Страница 84: ...72 cHAPTER 4 Operation Model 336 Temperature Controller...
Страница 104: ...92 cHAPTER 5 Advanced Operation Model 336 Temperature Controller...
Страница 164: ...152 cHAPTER 7 Options and Accessories Model 336 Temperature Controller...
Страница 178: ...166 cHAPTER 8 Service Model 336 Temperature Controller...