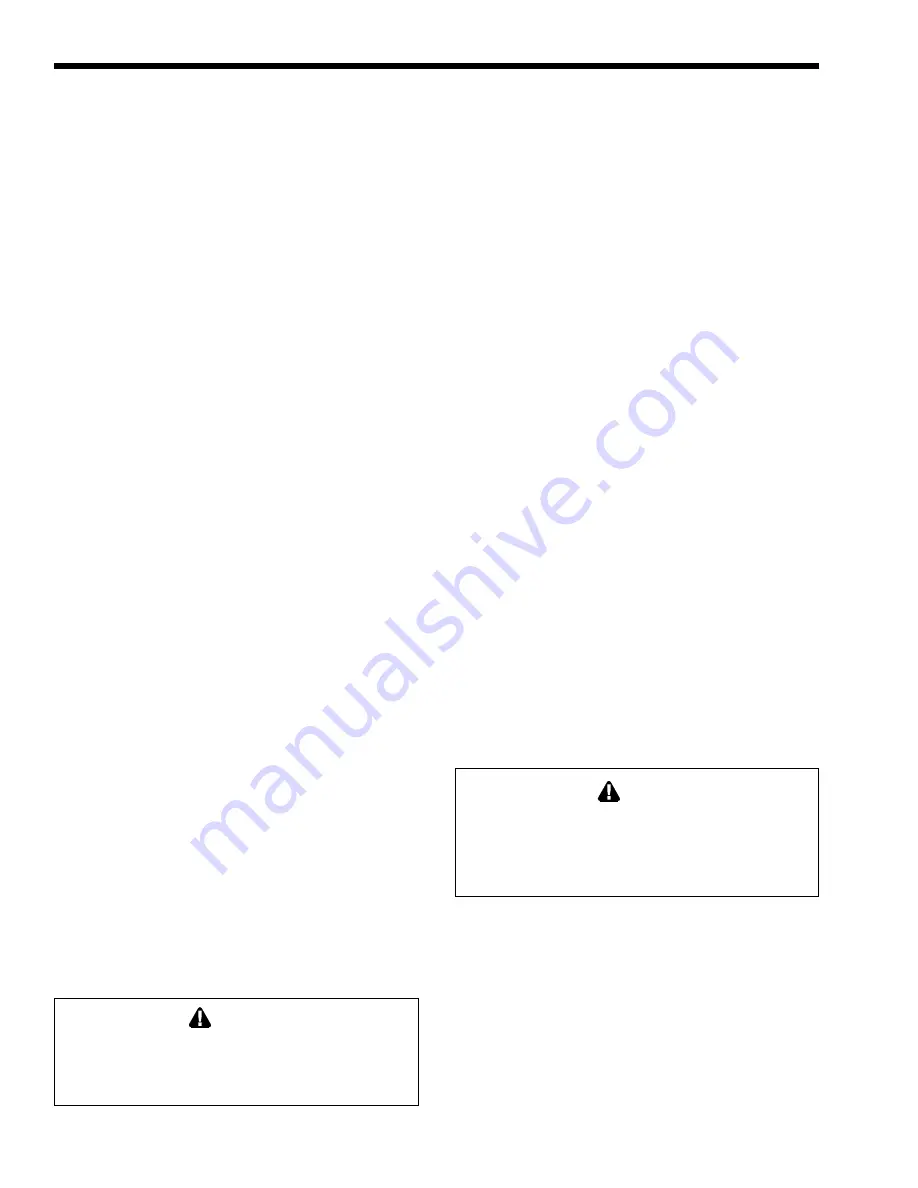
Page 22
LAARS HEATING SYSTEMS
3.
If a strainer is used in a pressure reducing valve
or in the piping, clean it every 6 months in
accordance with the manufacturer's instructions.
4.
At startup and every 6 months after, look at the
main burner flame for proper performance. The
burner should not require maintenance in normal
operation. If any malfunction indicates that the
burner needs service (e.g., a flame that is yellow,
or entire burner surface glowing red), call a
professional service technician. Flame
characteristics may be inspected during the first
30 seconds after ignition. Characteristics of a
good flame are:
a.
Blue flame color
b.
Dark-colored burner surface with
occasional glowing fibers on surface.
NOTE: After 30 seconds of operation the
combustion chamber will heat up and
prevent reliable flame observation.
5.
Inspect the venting system for blockage, leakage,
and corrosion at least once a year.
6.
Keep the heater area clear of combustible
material, gasoline, and other flammable liquids
and vapors.
7.
Be sure all combustion air and ventilation
openings are not blocked.
8.
After installation and first startup, check the heat
exchanger for black carbon soot buildup after the
following periods of operation: 24 hours, 7 days,
30 days, 90 days, and once every 6 months
thereafter.
4B. Heat Exchanger
Black carbon soot buildup on the external
surfaces of the heat exchanger is caused by one or
more of the following: incomplete combustion,
combustion air problems, venting problems and heater
short cycling. As soon as any buildup is seen, correct
the cause of the buildup. Scale can build up on the
inner surface of the heat exchanger tubes and
restrict the water flow. Inspect the heat exchanger in
accordance with Section 4B-1.
If the heat exchanger needs cleaning see
Section 4B-2.
4B-1. Inspection of the Heat Exchanger
WARNING
Improper installation or maintenance can cause
nausea or asphyxiation from carbon monoxide in
flue gases which could result in severe injury,
property damage, or death.
4B-1a. External Heat Exchanger
Inspection
1.
Disconnect electrical supply to the heater.
2.
Turn off the gas supply by closing the manual
gas valve on the heater.
3.
On indoor models, remove the vent pipe, top
jacket section, flue collector.
4.
On outdoor models, remove outdoor vent
terminal, top jacket section, flue collector.
5.
After removing the flue collector, inspect the
finned copper tubing using a flashlight.
6.
If there is a buildup of black carbon soot or other
debris on the heat exchanger tubes which may
restrict flue gas passage, refer to section 4B-2a.
7.
If there is no buildup of black carbon soot or
other debris which may restrict flue gas passage
through the heat exchanger, reassemble the
heater.
4B-1b. Internal Heat Exchanger
Inspection
1.
Remove the inlet/outlet header of the heat
exchanger.
2.
Remove the return cover of the heat exchanger.
3.
Inspect the internal surface of the copper tubes
for signs of scale buildup and erosion.
4.
If buildup exists clean per 4B-2b.
4B-2a. Cleaning the Heat Exchanger -
External
NOTE: The heat exchangers are heavy and may
require two people to remove to avoid personal injury.
Caution
Black carbon soot buildup on a dirty heat exchanger
can be ignited by a random spark or flame. To
prevent this from happening, dampen the soot
deposits with a wet brush or fine water spray before
servicing the heat exchanger.
1.
Disconnect the 120 Vac electrical supply to the
heater.
2.
Turn off the gas supply by closing the manual
gas valve on the heater.
3.
Disconnect and remove the wires and conduit
from the low water cutoff.
4.
Remove the top jacket section, venting and the
flue collector as mentioned in Section 4B-1
“Inspection of the Heat Exchanger”.
5.
Isolate the heat exchanger from water supply.
6.
Drain the heat exchanger.
Содержание Mighty Max VW Series
Страница 25: ...Mighty Max Volume Water Heater Page 25 Figure 19 Troubleshooting Chart...
Страница 27: ...Mighty Max Volume Water Heater Page 27 Front View Right Side View...
Страница 28: ...Page 28 LAARS HEATING SYSTEMS Front View Rear View Right Side View Left Side View...
Страница 31: ...Mighty Max Volume Water Heater Page 31...