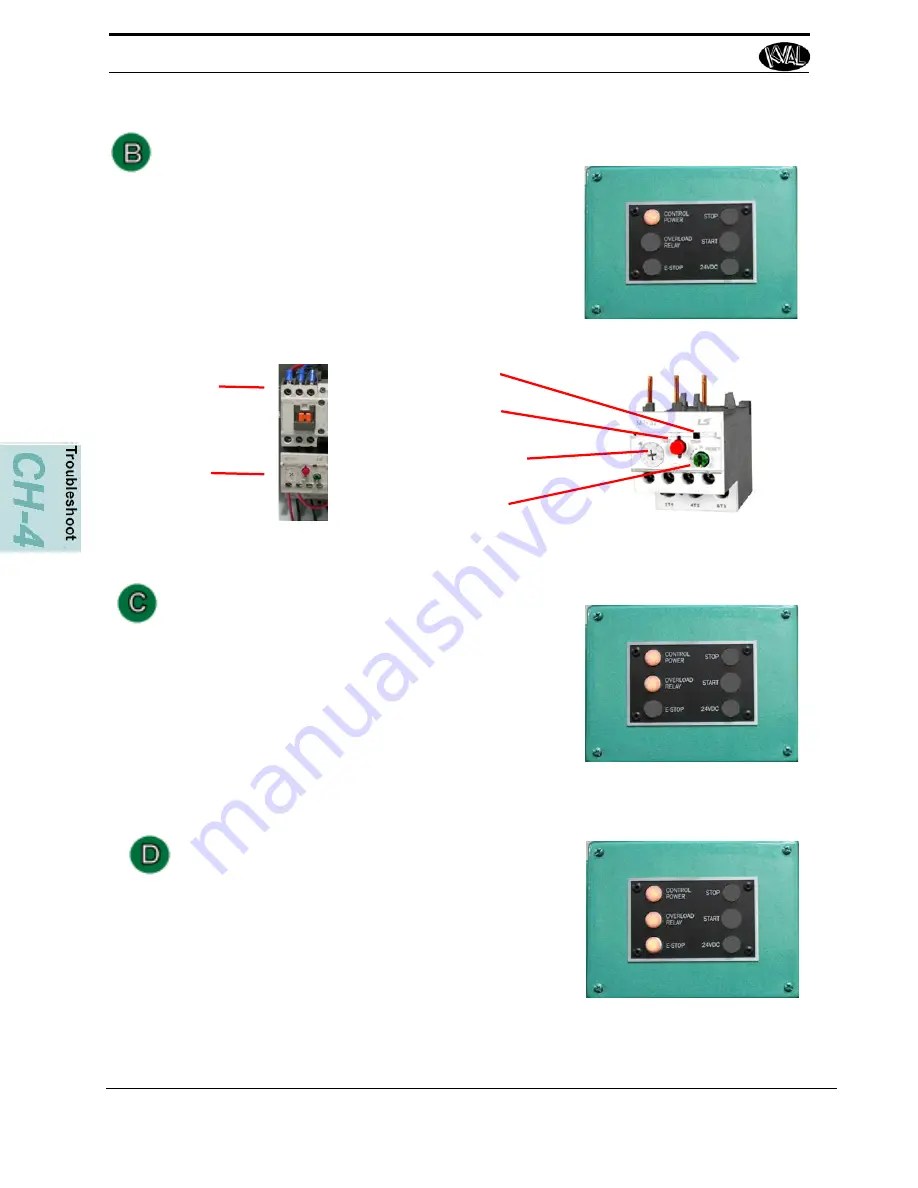
Troubleshooting with the Status Light Panel
4-8
KVAL Acro-HD Operation/Service Manual
1.
Check Motor Overload Circuits
2.
With power on, check the trip indicator LED on the
overload. If indicator is orange, press the Reset
Button to reset the overload circuit. Retest the
Machine.
Overload Relay Light OFF
Contactors
Overload
Relays
Reset Button. Fac-
tory set on the ''H''
Setting.
Test or Stop
Trip Indicator
Factory Set Current
Rating Adjust
E-Stop Light OFF
Check if any E-Stop buttons are pulled out.
NOTE:
Location and quantity of E-Stop buttons varies
depending on customer need. Typical locations for E-
Stop buttons are near the Rear Access Gate and near
the Tool Changer Access Gate
Stop Light OFF
Check for 120 VAC between #2 and #4 If there is
voltage, press the Start button. If no voltage, check
the Stop button to make sure it is all the way out and
not stuck in, then check the contact to make sure it is
closed. If still no voltage, check the wiring.
Содержание Acro-HD
Страница 4: ...KVAL Acro HD Operation Service Manual ...
Страница 20: ...Getting Help from KVAL 1 14 KVAL Acro HD Operation Service Manual Page Intentionally Left Blank ...
Страница 22: ...Safety Sign Off Sheet 1 16 KVAL Acro HD Operation Service Manual ...
Страница 40: ...Powering Up and Powering Down the Acro HD 2 18 KVAL Acro HD Operation Service Manual ...
Страница 48: ...Description of Air Input System 3 8 KVAL Acro HD Operation Service Manual ...
Страница 58: ...Troubleshooting with the Status Light Panel 4 10 KVAL Acro HD Operation Service Manual ...
Страница 61: ......
Страница 62: ......
Страница 63: ......