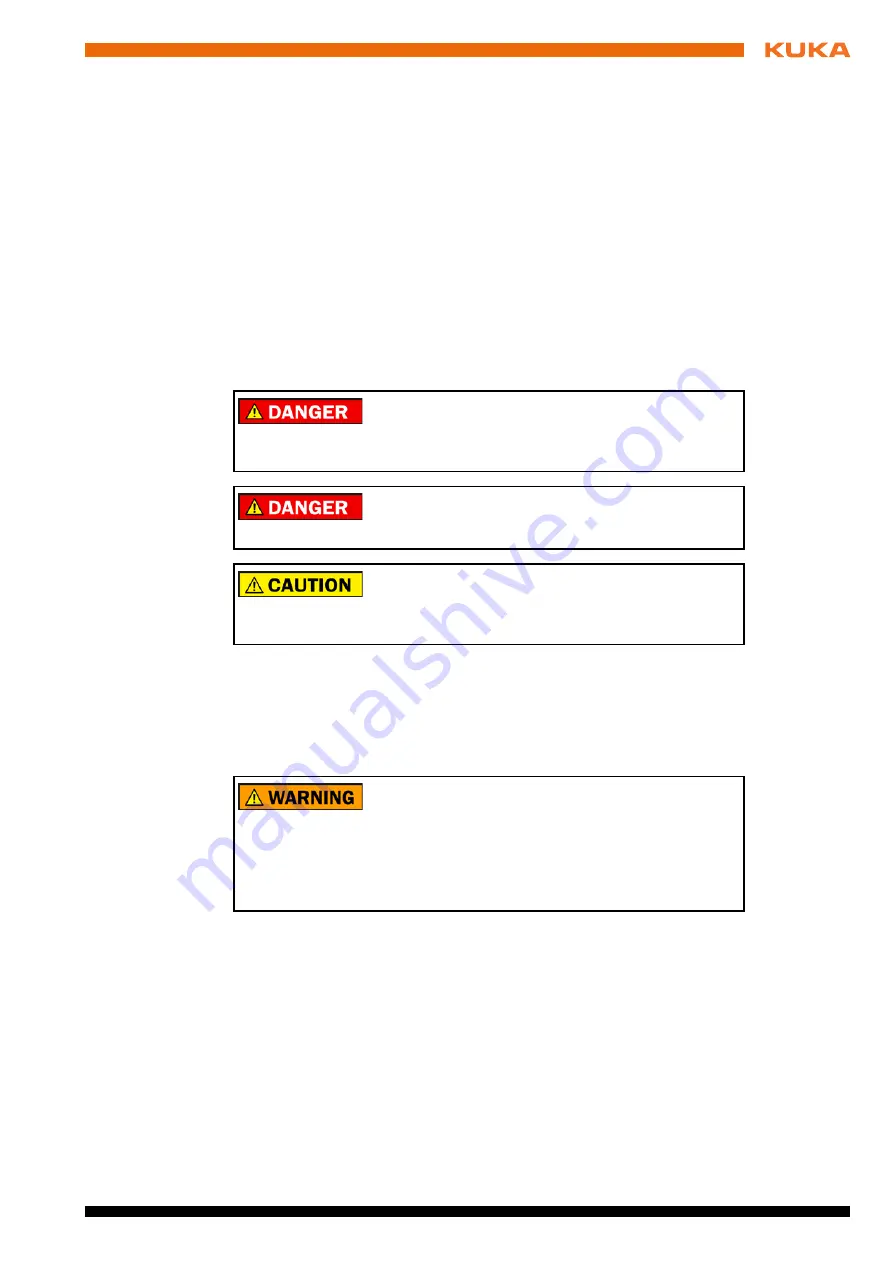
Issued: 22.04.2016 Version: Spez KR 20-3 V2
5 Safety
5.5
Safety measures
5.5.1
General safety measures
The industrial robot may only be used in perfect technical condition in accor-
dance with its intended use and only by safety-conscious persons. Operator
errors can result in personal injury and damage to property.
It is important to be prepared for possible movements of the industrial robot
even after the robot controller has been switched off and locked out. Incorrect
installation (e.g. overload) or mechanical defects (e.g. brake defect) can cause
the manipulator or external axes to sag. If work is to be carried out on a
switched-off industrial robot, the manipulator and external axes must first be
moved into a position in which they are unable to move on their own, whether
the payload is mounted or not. If this is not possible, the manipulator and ex-
ternal axes must be secured by appropriate means.
KCP/smartPAD
The user must ensure that the industrial robot is only operated with the KCP/
smartPAD by authorized persons.
If more than one KCP/smartPAD is used in the overall system, it must be en-
sured that each device is unambiguously assigned to the corresponding in-
dustrial robot. They must not be interchanged.
External
keyboard,
external mouse
An external keyboard and/or external mouse may only be used if the following
conditions are met:
Start-up or maintenance work is being carried out.
The drives are switched off.
There are no persons in the danger zone.
The KCP/smartPAD must not be used as long as an external keyboard and/or
external mouse are connected to the control cabinet.
The external keyboard and/or external mouse must be removed from the con-
trol cabinet as soon as the start-up or maintenance work is completed or the
KCP/smartPAD is connected.
In the absence of operational safety functions and safe-
guards, the industrial robot can cause personal injury or
material damage. If safety functions or safeguards are dismantled or deacti-
vated, the industrial robot may not be operated.
Standing underneath the robot arm can cause death or
injuries. For this reason, standing underneath the robot
arm is prohibited!
The motors reach temperatures during operation which
can cause burns to the skin. Contact must be avoided.
Appropriate safety precautions must be taken, e.g. protective gloves must be
worn.
The operator must ensure that decoupled KCPs/smart-
PADs are immediately removed from the system and
stored out of sight and reach of personnel working on the industrial robot.
This serves to prevent operational and non-operational EMERGENCY STOP
devices from becoming interchanged.
Failure to observe this precaution may result in death, severe injuries or con-
siderable damage to property.
Содержание KR 20-3
Страница 6: ...6 81 Issued 22 04 2016 Version Spez KR 20 3 V2 KR 20 3...
Страница 8: ...8 81 Issued 22 04 2016 Version Spez KR 20 3 V2 KR 20 3...
Страница 12: ...12 81 Issued 22 04 2016 Version Spez KR 20 3 V2 KR 20 3...
Страница 33: ...33 81 Issued 22 04 2016 Version Spez KR 20 3 V2 4 Technical data Fig 4 20 Stopping times for STOP 1 axis 1...
Страница 35: ...35 81 Issued 22 04 2016 Version Spez KR 20 3 V2 4 Technical data Fig 4 22 Stopping times for STOP 1 axis 2...
Страница 38: ...38 81 Issued 22 04 2016 Version Spez KR 20 3 V2 KR 20 3 Fig 4 26 Stopping times for STOP 1 axis 1...
Страница 40: ...40 81 Issued 22 04 2016 Version Spez KR 20 3 V2 KR 20 3 Fig 4 28 Stopping times for STOP 1 axis 2...
Страница 42: ...42 81 Issued 22 04 2016 Version Spez KR 20 3 V2 KR 20 3...
Страница 62: ...62 81 Issued 22 04 2016 Version Spez KR 20 3 V2 KR 20 3...
Страница 68: ...68 81 Issued 22 04 2016 Version Spez KR 20 3 V2 KR 20 3...
Страница 70: ...70 81 Issued 22 04 2016 Version Spez KR 20 3 V2 KR 20 3...
Страница 78: ...78 81 Issued 22 04 2016 Version Spez KR 20 3 V2 KR 20 3...
Страница 81: ...81 81 Issued 22 04 2016 Version Spez KR 20 3 V2 KR 20 3...