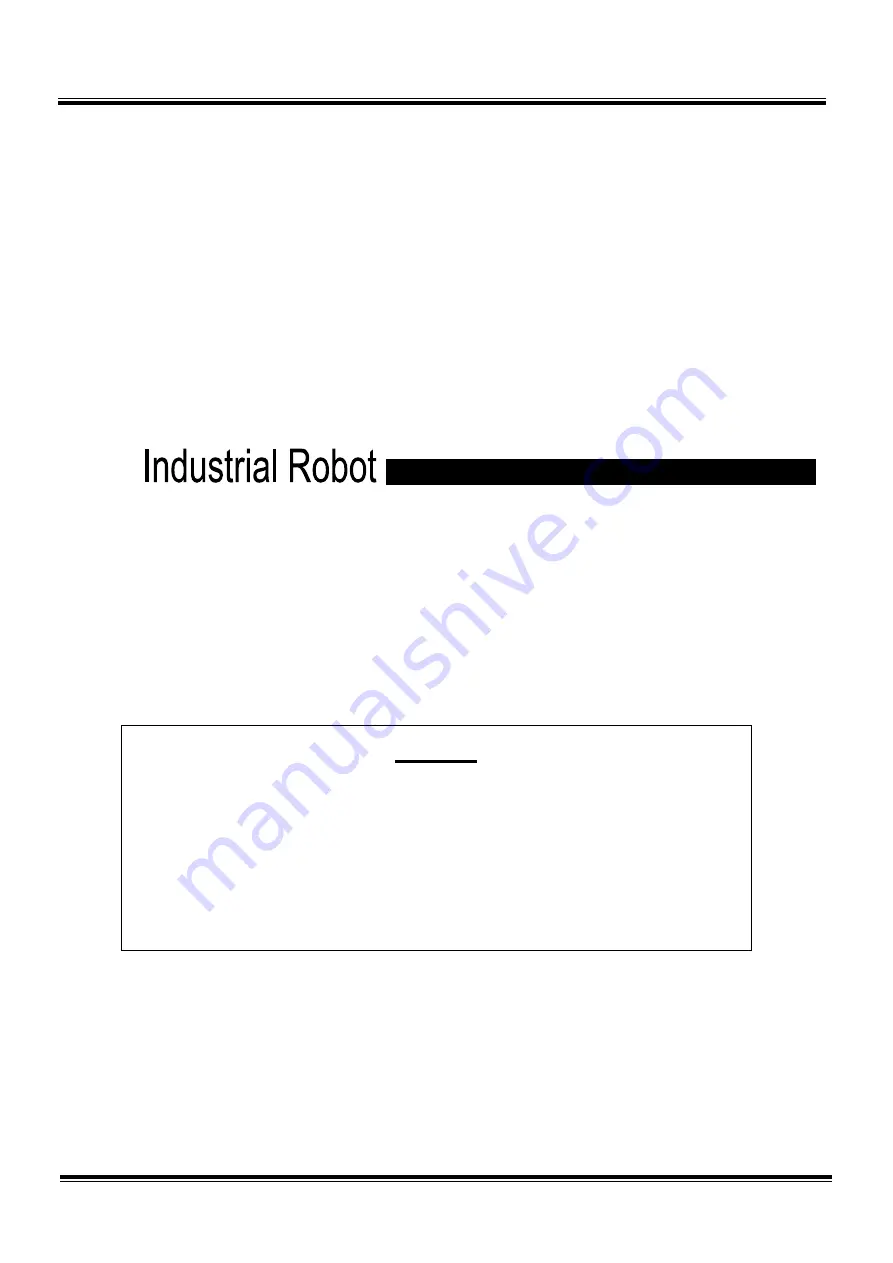
STE80753-2
TH850A
TH1050A
TH1200A/TS3100
INSTRUCTION MANUAL
INDUSTRIAL ROBOT
TRANSPORTATION AND INSTALLATION MANUAL
Notice
1. Make sure that this instruction manual is delivered to the final
user of Toshiba Machine’s industrial robot.
2. Before operating the industrial robot, read through and
completely understand this manual.
3. After reading through this manual, keep it nearby for future
reference.
January, 2009
TOSHIBA MACHINE CO., LTD.