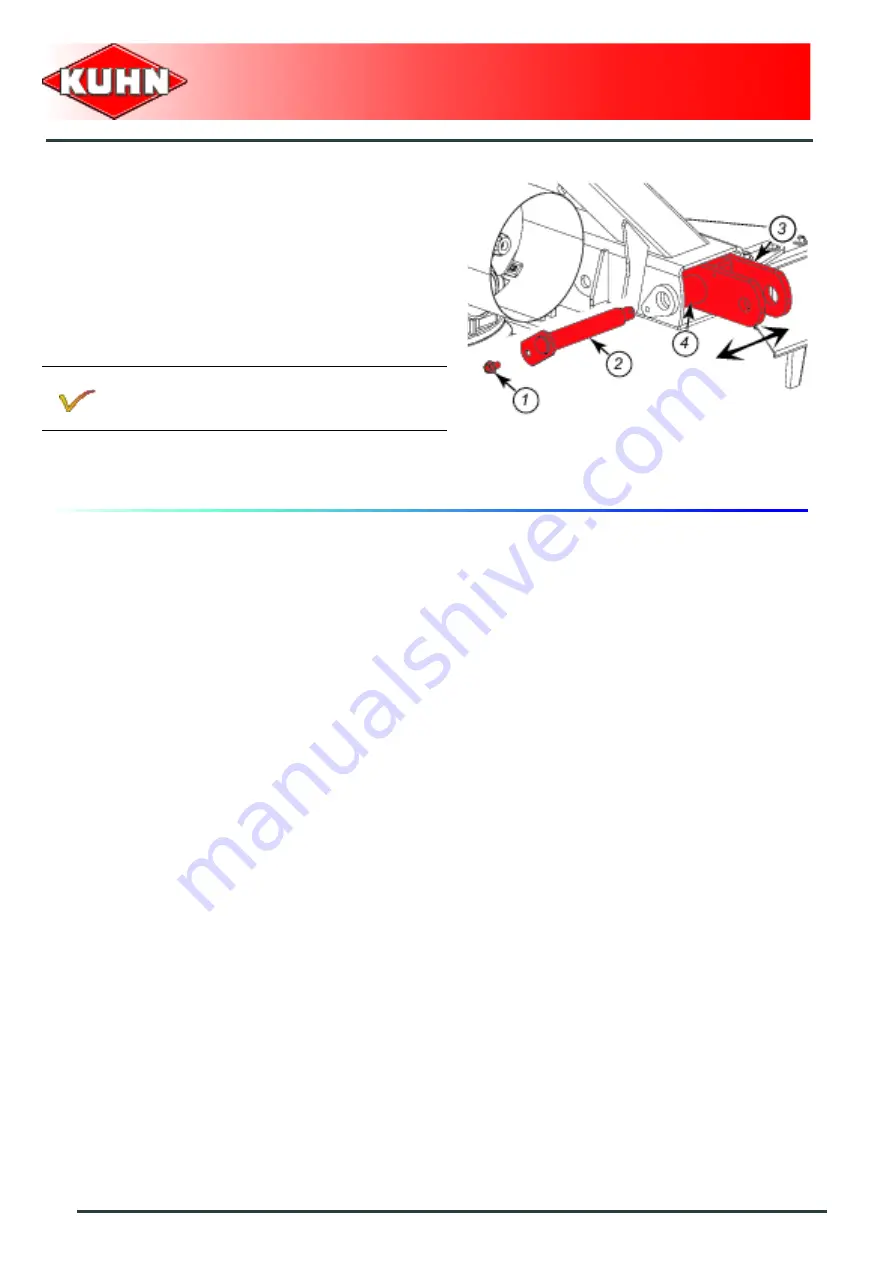
Power harrows
30
HRB353D - 403D
Putting into service
Adjustment
- Remove screw (1).
- Remove pin (2).
- Position yoke (3) and spacer (4) in the required
position.
- Insert pin (2).
- Reinstall screw (1).
Torque screw (1) to 6 daN m (44 lbf ft).
- Proceed the same way on the other side.
Check that the 2 lower links have been adjusted
identically.
Содержание HRB353D
Страница 1: ...KN103DGB B OPERATOR S MANUAL Power harrows HRB353D 403D KN103DGB B English 11 2009 ...
Страница 2: ......
Страница 19: ...Safety Power harrows HRB353D 403D 17 HRB403D ...
Страница 88: ...Power harrows 86 HRB353D 403D Limited warranty Limited warranty ...
Страница 89: ...Limited warranty Power harrows HRB353D 403D 87 ...
Страница 90: ......
Страница 91: ......
Страница 92: ......