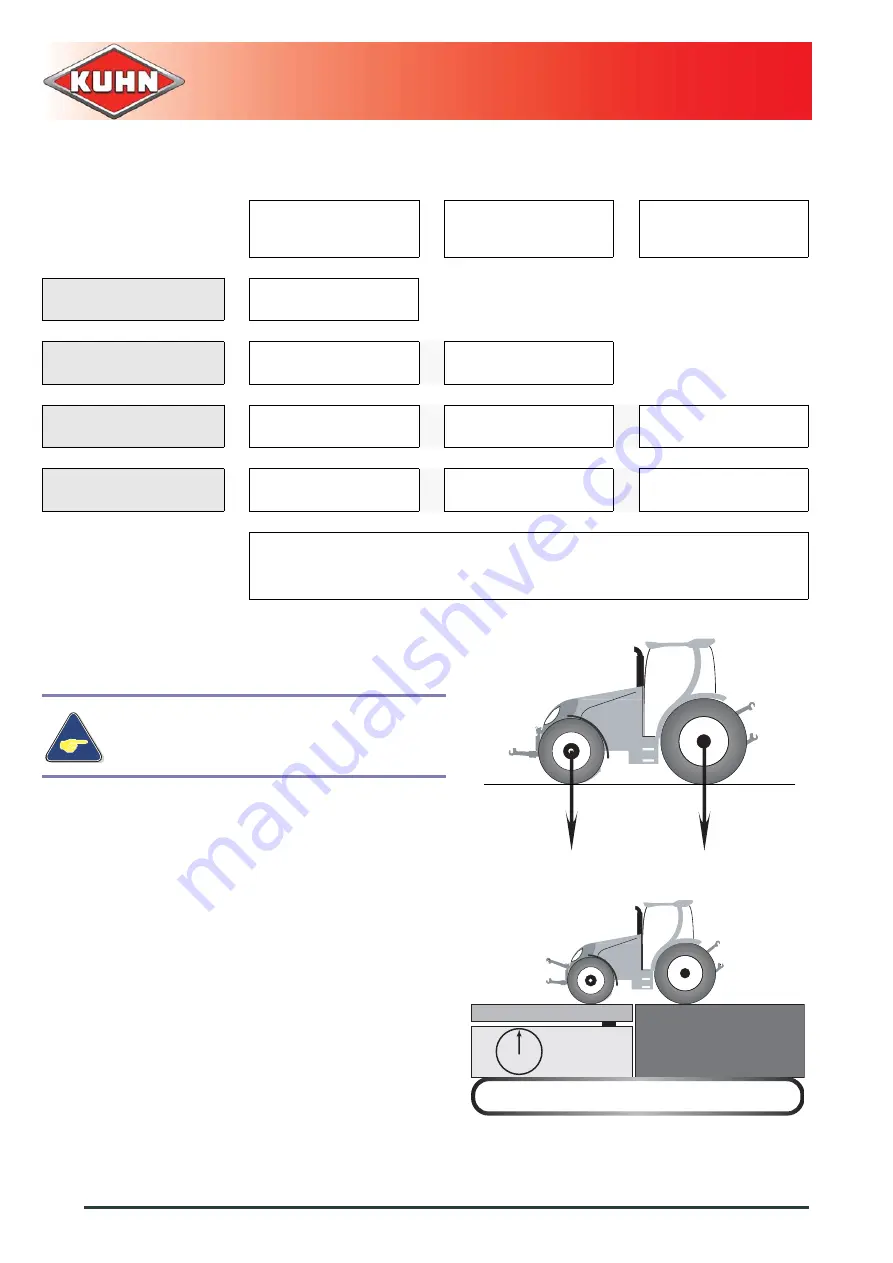
EL92-180/205/230
82
12. - Appendix
KN007CGB_F
Power tiller
Table
Actual value obtained
by calculation
Value authorized
according to
operator's manual
Double value of the
authorized capacity
per tyre (2 tyres)
Minimum front/rear
ballasting
kg
Total weight
kg
<
kg
Load on front axle
kg
<
kg
<
kg
Load on rear axle
kg
<
kg
<
kg
The minimum ballasting must be made by fitting a tool or an additional mass to the
tractor.
The values obtained must be below or equal the authorized values.
Determining the machine weight (M2) and
the position of its centre of gravity (d)
- If the data required to calculate the total
weight, axle loads and minimum ballasting
are not supplied, use the following method.
Tractor only:
T1: Load on front axle.
• Tractor only.
T1
T2
T1 = _____kg
T1 =
________
kg
Содержание EL92-180
Страница 2: ......
Страница 66: ...EL92 180 205 230 66 9 Optional equipment KN007CGB_F Power tiller 9 9 Clamp Rotors ...