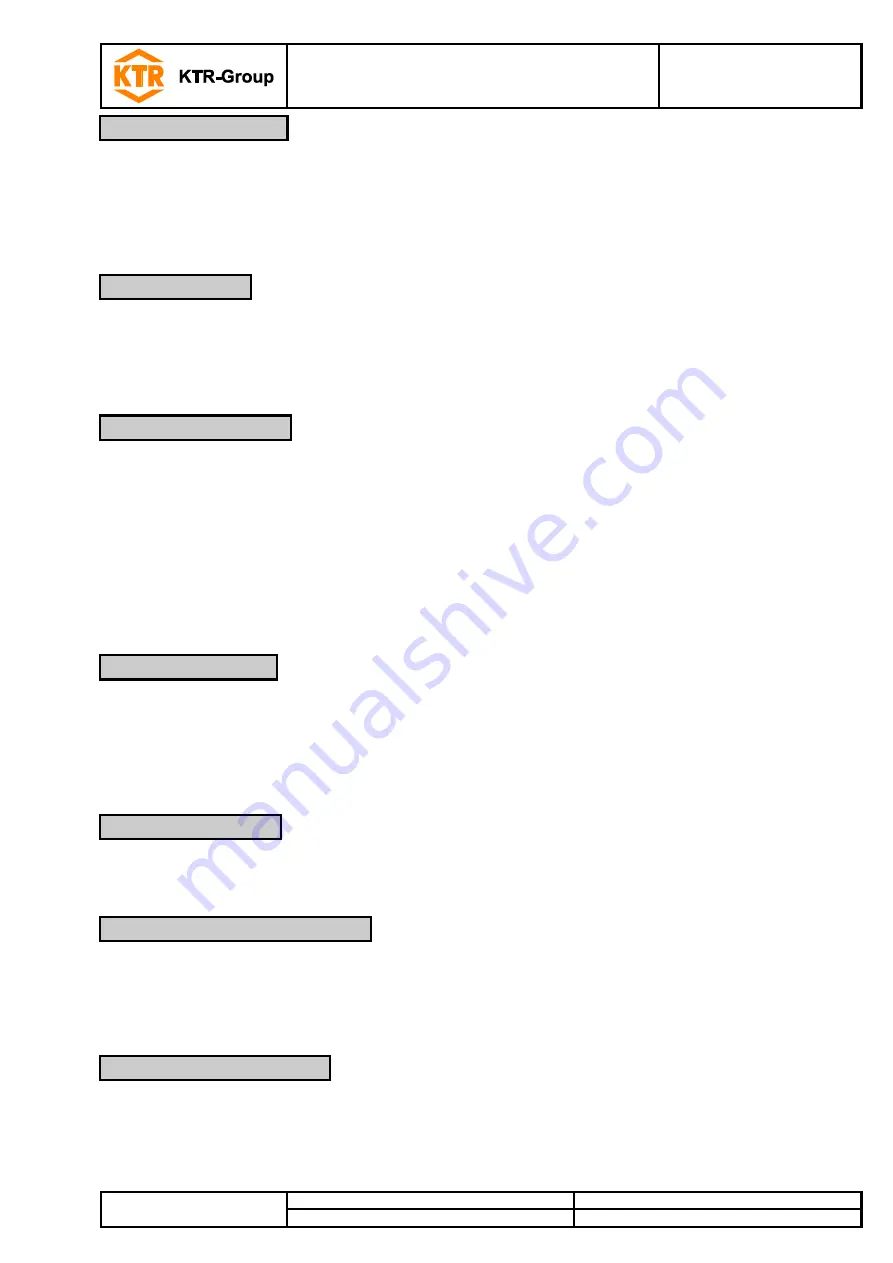
KTR-STOP® TB Thruster
acc. to DIN 15430
Operating/Assembly instructions
KTR-N
Sheet:
Edition:
44414 EN
10 of 17
4
Please observe protection
note ISO 16016.
Drawn:
2020-11-02 Shg/Mro
Replacing:
KTR-N dated 2020-04-08
Verified:
2020-11-02 Shg
Replaced by:
Electrohydraulic thrusters are driven by a three-phase motor (component 2). All units are protected
according to IP 66 (DIN EN 60529 (VDE 0470-1)). The motor winding is insulated for use in the
tropics, insulation
class F.
All types have a terminal box (component 3) with a six-pole terminal board (nine-pole as a special
type), lead connection M4, protective conductor terminal M5 and a waterproof cable gland M25x1.5
on the right. The motors are connected via star connection (Y).
The standard voltage is for example:
•
400 V, 50 Hz, 3~
•
460 V, 60 Hz, 3~
•
500 V, 50 Hz, 3~
•
690 V, 50 Hz, 3~.
Different voltage and frequencies are available on request.
The units are suitable for continuous operation S1 (100 %) and intermittent duty S3 (60 % ED) with
up to 2000 switches per hour. Deviations of the operating voltage by a maximum of ±5 % do not
have any effect on the performance of the units.
A supplement will be charged for all thrusters with special equipment:
The service life of the units can be extended by installing a globe or lowering valve The valves are
installed over the terminal box in the hydraulic space and must be set externally. The positioning
times can be extended twentyfold at the minimun, setting is made continuously- see chapter 10.
A parallel connection of three capacitors allows to reduce the standard lowering time. The
arrangement of capacitors reduces the deceleration time when turning off the motor so that the oil
pressure decreased particularly fast. In this case the thruster must be controlled by a separate
contactor.
6
Electrical version
6.1 Connections
6.2 Operating voltage
6.3 Operation mode
7
Special versions
7.1 Globe and/or lowering valve
7.2 Rapid lowering control