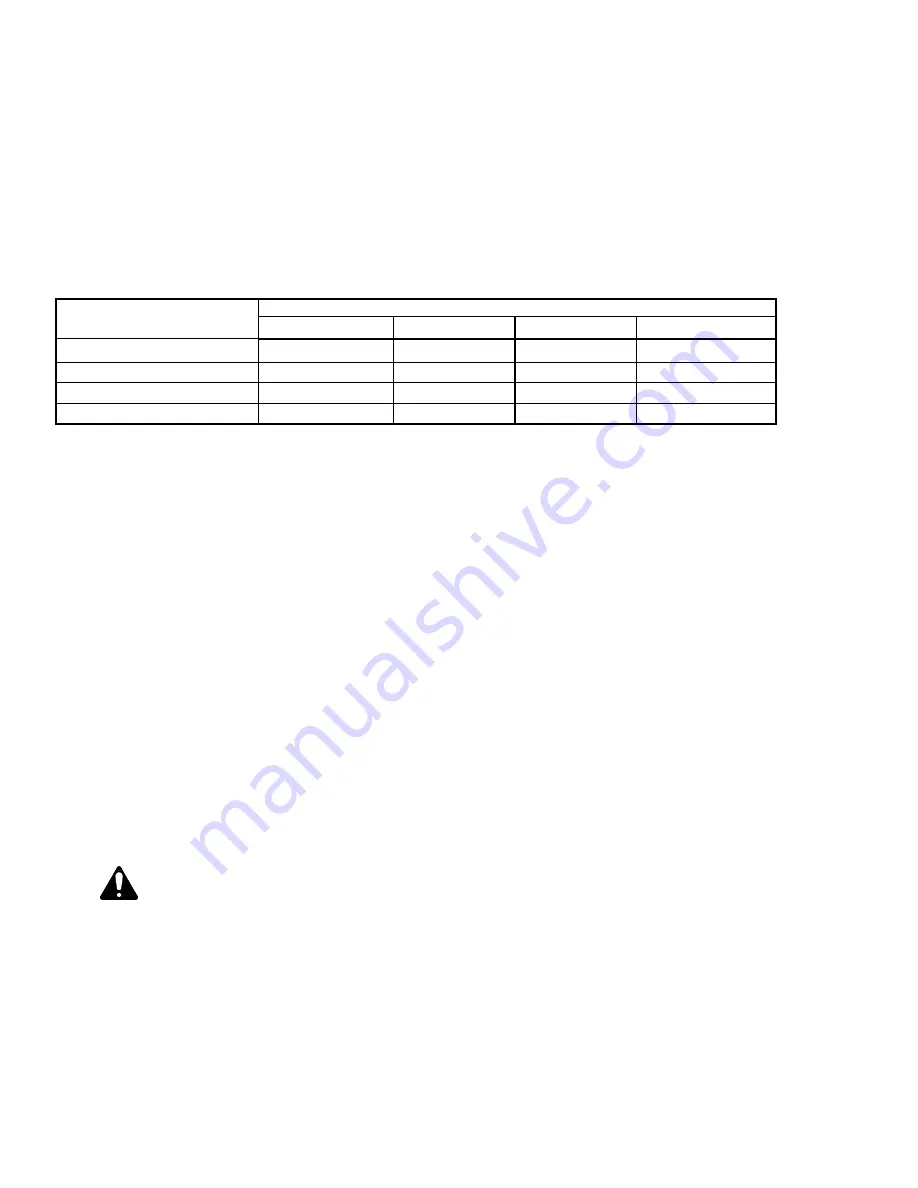
Attention
:
* At the beginning of the tungsten electrode argon arc welding flux before welding argon (Ar) to blow
air can be more conducive to welding pipe net
。
* High frequency arc ignition arc pulse to work long hours and cannot, should check the gas path of tungsten
electrode and welding wire for adverse factors Don't let the high frequency arc pulse to work long hours without arc
ignition
!
* In the tungsten electrode argon arc welding, when at the end of the welding, let go of the welding torch button
should be completed when stagnant air end rear can remove the welding torch
, or welding joint get good protection
。
Welding Criterion Parameter
(For Reference Only)
Name
Welding current A
3
~
20
15
~
80
70
~
160
100
~
200
Tungsten electrode diameter mm
Φ 0.5
Φ 1.0
Φ 1.6
Φ 2.0
Gas-flow L/min
4
~
5
5
~
7
6
~
8
8
~
12
Nozzle specifications mm
Φ 4
、
Φ 6
、
Φ 8
Φ 6
、
Φ 8
、
Φ 10
Φ 8
、
Φ 10
Φ 10
、
Φ 12
Filler wire diameter mm
≤ Φ 1.0
≤ Φ 1.6
Φ 1.0
~
Φ 2.4
Φ1.6
~
Φ 3.0
Maintenance and Service
The most distinctive difference of 410-PROTIG20 Welder with the traditional welder is that it mostly
adopt modern electric apparatus with high level technology. It is among the list of high-tech products,
as a result higher technical requirement is asked for the maintenance personnel. However there are very
few spare parts for that type machine, so maintenance is not required very often except the routine
cleaning. Only the qualified people are allowed to be in charge of the repair job. It is strongly
recommended that customers contact our company for the technical back-up or service when they feel
unable to work out the technical hitch or problems.
The maintenance job mainly includes:
* Dust Removal
The professional maintenance personnel should use dry compressed air (air compression machine)
to move the dust inside the machine regularly. Make sure there is no abnormal condition happening in
the tightened places such as the loose and connecting wire. Eliminate the problem as soon as it
occurs. In the case when the dust is easily to accumulate, it should be cleaned in time. Usually the
machine should be cleaned once a year if the dust accumulation problem is not very serious, while it
needs cleaning once or even twice every quarter if the dust accumulation problem is serious.
* Make sure that the connection of welding cable socket is in sound condition.
Regular check should be taken on the connection condition of the welding cable socket. The
operator should check it at least once a month for the fixed machine, while the operator should check
every time before using for the moveable machine.
ATTENTION
:
* The welder main loop voltage is always higher, so the safety precaution should be taken
before
repairing to avoid accidental shock. Under no circumstance can anyone except the
professionally trained personnel open the case of the machine.
* Switch off the power source each time when removing dust.
* Never tamper with inside cable or damage the component parts while removing dust.