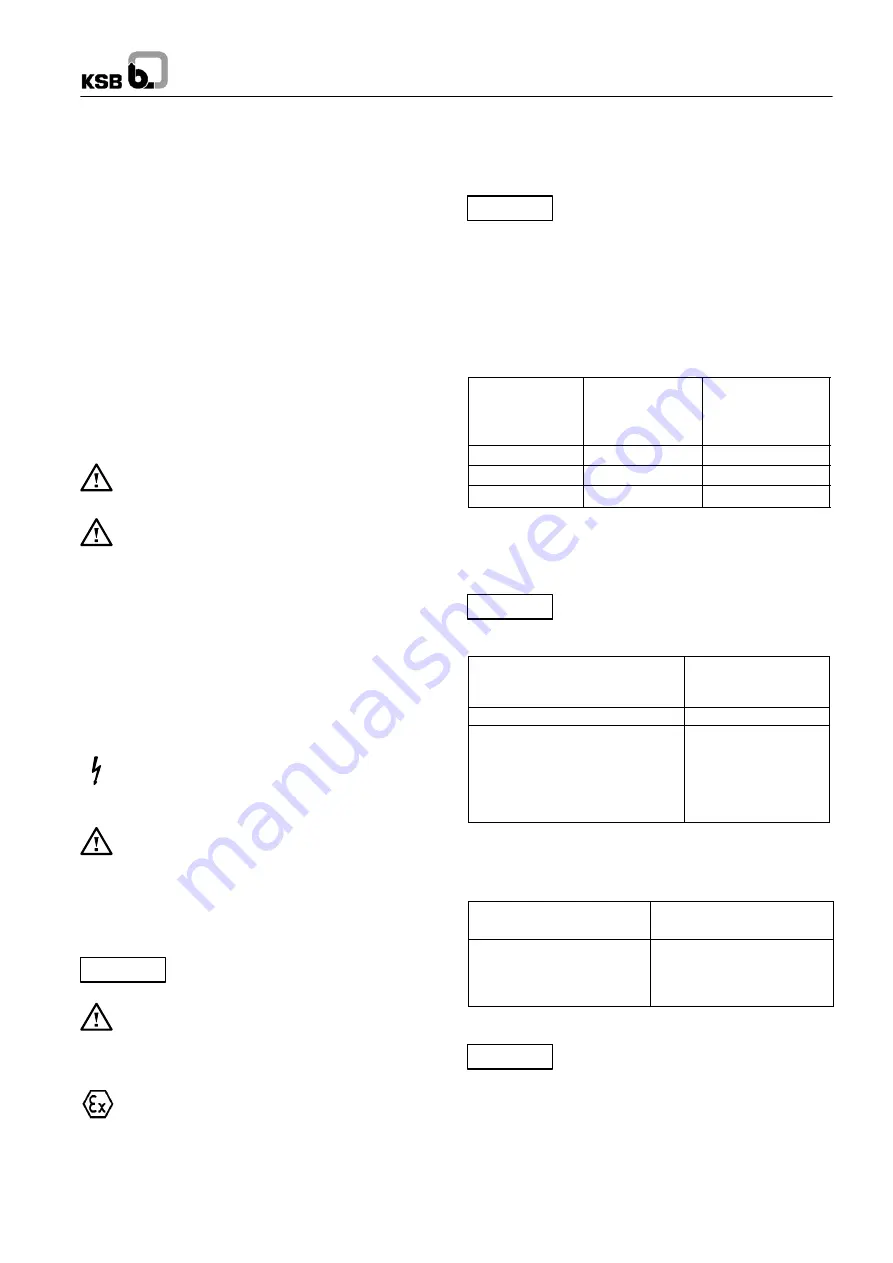
Caution
Caution
Caution
Caution
RPH
13
6.3.2
Measures to be taken for prolonged shutdown
1.The pump remains installed; periodic check of operation
In order to make sure that the pump is always ready for instant
start-up and to prevent the formation of deposits within the
pump and the pump intake area, start up the pump set
regularly once a month or once every 3 months for a short
time (approx. 5 minutes) during prolonged shutdown periods.
Prior to an operation check run ensure that there is sufficient
liquid available for operating the pump.
2.The pump is removed from the pipe and stored
Before putting the pump into storage, carry out all checks
specified in sections 7.1 to 7.4. Then apply appropriate
preservatives:
- Spray-coat the inside wall of the pump casing, and in
particular the impeller clearance areas, with a preservative.
Spray the preservative through the suction and discharge
nozzles. It is advisable to close the pump nozzles (e.g. with
plastic caps or similar).
6.4
Returning to service after storage
Before returning the pump to service, carry out all checks and
maintenance work specified in sections 7.1 and 7.2.
In addition, the instructions laid down in the sections on
”Commissioning” (6.1) and ”Operating Limits” (6.2) must
be observed.
Immediately following completion of the work, all
safety-relevant and protective devices must be
re-installed and/or re-activated.
7
Servicing / maintenance
7.1
General instructions
The operator is responsible for ensuring that all maintenance,
inspection and installation work be performed by authorized,
qualified specialist personnel who are thoroughly familiar with
the manual.
A regular maintenance schedule will help avoid expensive
repairs and contribute to trouble-free, reliable operation of the
pump with a minimum of maintenance expenditure and work.
Work on the unit must only be carried out with the
electrical connections disconnected. Make sure
that the pump set cannot be switched on accidentally
(danger to life!).
Pumps handling liquids posing health hazards
must be decontaminated. When draining the fluid
see to it that there is no risk to persons or the environment.
All relevant laws must be adhered to (danger to life)!
7.2
Servicing / inspection
7.2.1
Supervision of operation
The pump must run quietly and free from
vibrations at all times.
The pump must never be allowed to run dry.
Prolonged operation against a closed shut-off valve is
not permitted. When operating the pump set with the
shut-off valve in the discharge line slightly open for a short
period of time, the permissible pressure and temperature limits
must not be exceeded.
A special design is required to comply with temperature
class T6 in the bearing area. In such cases, and if am-
bient temperature exceeds 40
°
C, contact the manufacturer.
Verify correct oil level as described in section 6.1.1.
The shut-off elements and the auxiliary feed lines must not be
closed during operation.
Any stand-by pumps installed shall be started up regularly, e.g.
once a week, to keep them operational. Attention shall be paid
to the correct functioning of the auxiliary connections. The
cooling system must be thoroughly cleaned at least once a year
to ensure proper cooling. Take the pump out of service for this
purpose.
If the flexible coupling elements begin to show
signs of wear, they must be replaced in due
time. Re-align the coupling as described in section 5.3.1.
7.2.2
Lubrication and lubricant change
7.2.2.1 Lubrication
The rolling element bearings are lubricated with mineral oil. The
lubricant change intervals as well as the required quantity and
quality are specified below.
7.2.2.2 Oil change (operating hours)
Temperature
at the bearing
First oil change
after ..... operat-
ing hours
All subsequent oil
changes
after .....
operating hours
up to 70
°
C
300
8500
*)
70
°
C - 80
°
C
300
4200
*)
80
°
C - 90
°
C
300
2000
*)
*) at least once a year
Procedure:
Remove screwed plug below the bearing bracket and drain off
the oil. After drainage of the bearing bracket, screw in the plug
again and fill with fresh oil as described in section 6.1.1.
Please observe the local laws applicable to the
disposal of such substances.
7.2.2.3 Oil quality
Designation
Lubricating oil CLP46
DIN 51517
or HD 20W/20 SAE
Symbol to DIN 51502
V
Kinematic viscosity at 40
°
C
Flash point (to Cleveland)
Solidification point (pour point)
Application temperature *)
46
±
4 mm
2
/s
+ 175
°
C
-15
°
C
higher than permiss-
ible bearing tempera-
ture
*) For ambient temperatures below -10
°
C another suitable lubricating oil
type must be used.
Request particulars.
7.2.2.4 Oil quantity
Bearing bracket
Oil quantity in bearing
bracket in litres
B 02
B 03
B 05
B 06
0.9
1.8
2.5
5.7
7.3
Drainage / disposal
If the pump was used for handling liquids
posing health hazards, see to it that there is no
risk to persons or the environment when draining the fluid. All
relevant laws must be heeded. If required, wear safety clothing
and a protective mask!
If the fluids handled by the pumps leave residues which might
lead to corrosion when coming into contact with atmospheric
humidity, or which might ignite when coming into contact with
oxygen, then the unit must be flushed through, neutralized, and
then for drying purposes anhydrous gas must be blown through
the pump.