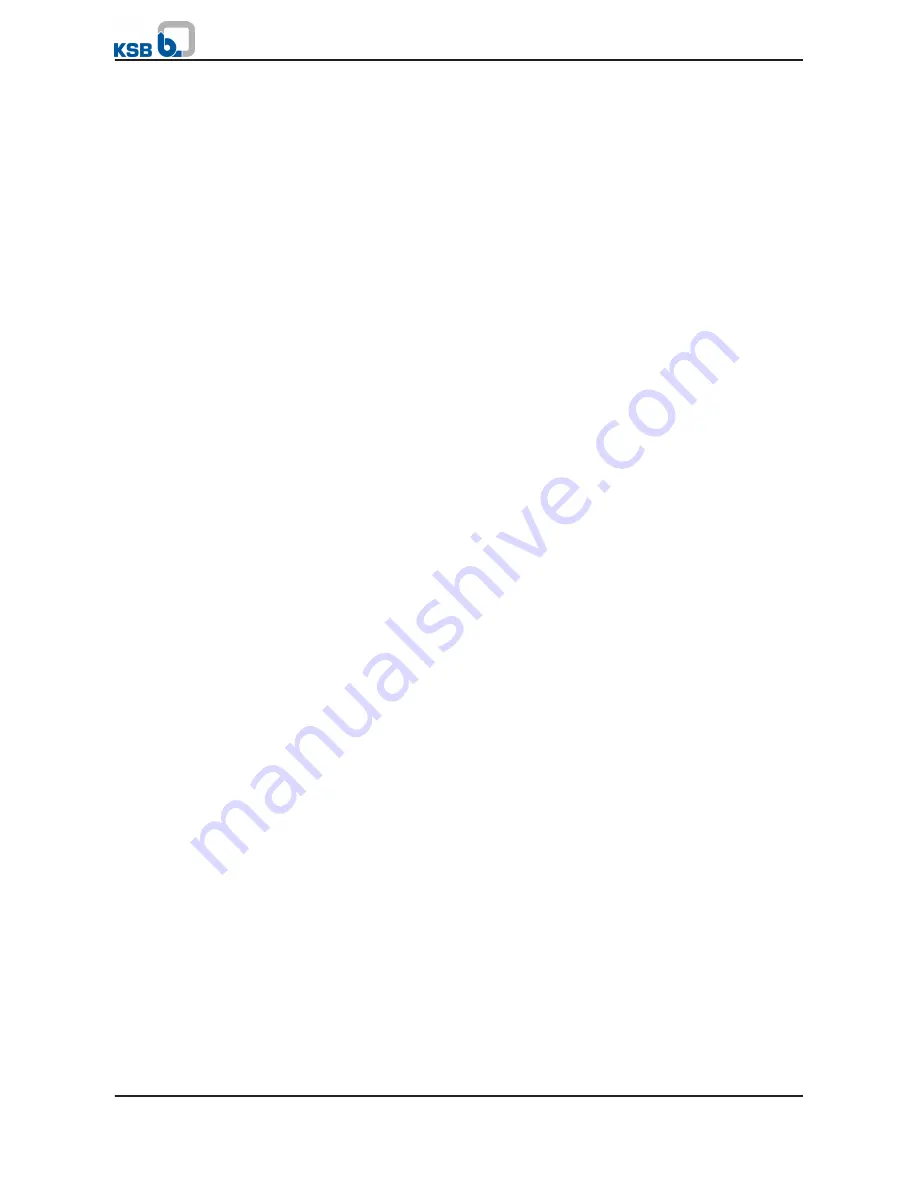
Index
A
Abrasive fluids 45
Applications 8
Auxiliary connections 36
B
Bearing temperature 49
Bearings 19
C
Certificate of decontamination 91
Commissioning/start-up 40
D
Design 19
Dismantling 54
Disposal 16
E
Event of damage
Ordering spare parts 67
Explosion protection 10, 23, 32, 33, 34, 37, 38, 40, 41,
42, 43, 45, 47, 48, 50, 52
F
Faults
Causes and remedies 69
Filter 32, 52
Frequency of starts 45
G
Gland packing 42
I
Impeller type 19
Installation at site 23
Intended use 8
M
Maintenance 48
Mechanical seal 42
Misuse 9
N
Noise characteristics 20, 21
O
Operating limits 43
Order number 6
Other applicable documents 6
P
Partly completed machinery 6
Piping 31
Preservation 14
Priming and venting 40
Pump casing 19
R
Reassembly 61
Return to supplier 15
Returning to service 46
Running noises 48
S
Safety 8
Safety awareness 9
Scope of supply 22
Shaft seal 19
Spare part
Ordering spare parts 67
Spare parts stock 67
Start-up 41
Storage 14
T
Temperature limits 11
Index
92 of 94
Omega / Omega V
Содержание Omega
Страница 93: ......