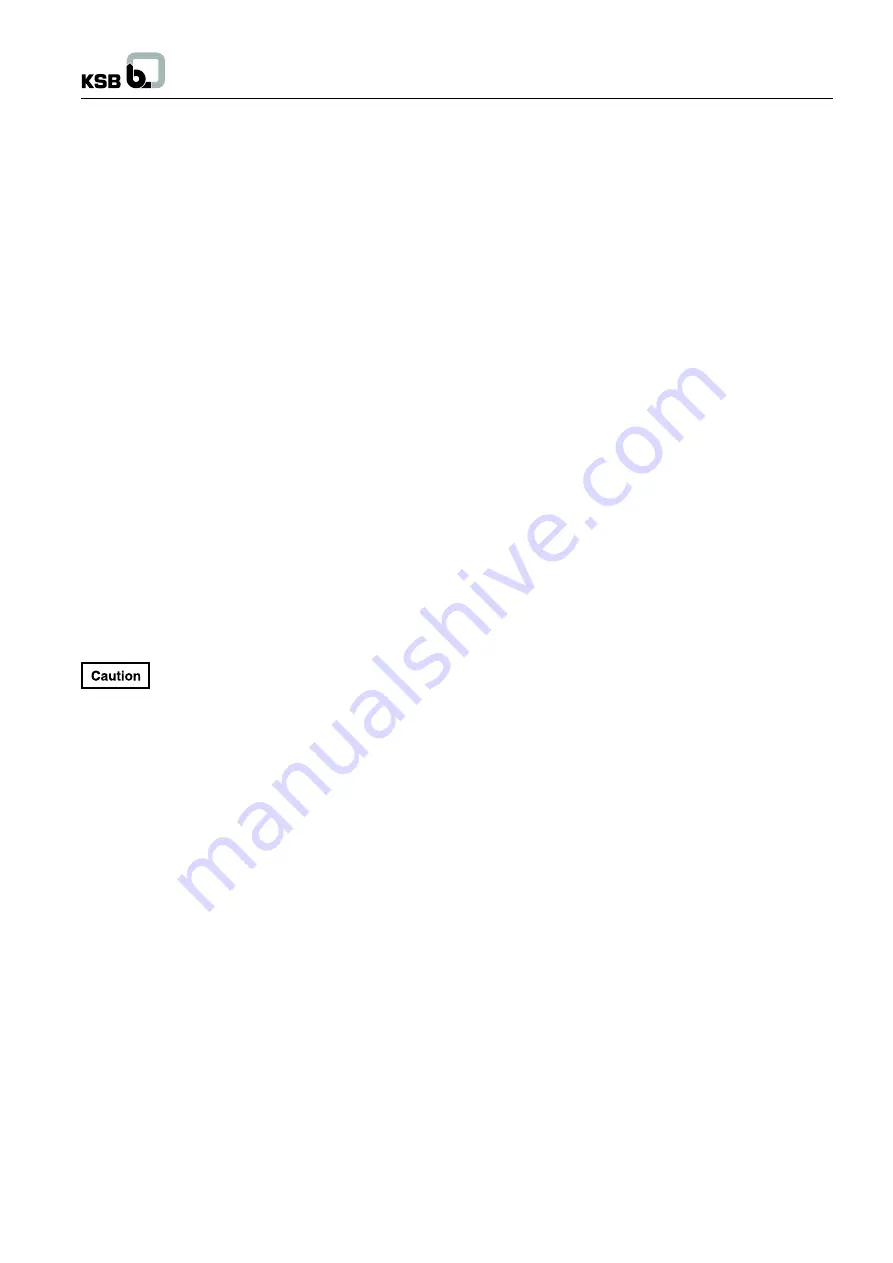
moviBOOST VPt / CL
2
Work on the machine / unit must be carried out only during
standstill. The shutdown procedure described in the manual for
taking the unit out of service must be adhered to without fail.
Pumps or pump units handling fluids injurious to health must be
decontaminated.
Immediately following completion of the work, all safety-relevant
and protective devices must be re-installed and / or re-activated.
Please observe all instructions set out in the chapter on
“Commissioning / start-up” before returning the unit to service.
2.7
Unauthorised modification and manufacture
of spare parts
Modifications or alterations of the equipment supplied are only
permitted after consultation with the manufacturer. Original spare
parts and accessories authorised by the manufacturer ensure
safety. The use of other parts can invalidate any liability of the
manufacturer for resulting damage.
2.8
Unauthorised modes of operation
The warranty relating to the operating reliability and safety of the
unit supplied is only valid if the equipment is used in accordance
with its designated use (see section 4). The limits stated in the
data sheet must not be exceeded under any circumstances.
3
Transport and interim storage
The package unit is packaged on pallets or in wooden crates
and wrapped in plastic foil for shipping and interim storage. All
connecting points are capped. It is imperative that the shipping /
handling instructions shown on the package be followed.
The unit must be protected against frost.
If upon unpackaging the unit you should discover that the package
has been damaged by dropping or some other form of mechanical
impact, please carefully inspect the unit itself for possible damage
and inform the freight forwarder / KSB’s customer service, even
if you have not been able to detect any such damage.
Once the unit has been removed from the package, it must be
stored in accordance with the location and installation instructions
(see Installation and location).
4
Description
4.1
General description
The fully electronic pressure boosting package units are supplied
ready for connection.
The equipment circuitry allows both direct and indirect connection
to the water supply system.
The equipment must be operated and maintained as to ensure
uninterrupted reliability of water supply, without causing
disturbances in the public water supply or other consumer
supply systems.
Any applicable
Water utility or fire protection regulations
must
be complied with.
Furthermore, local conditions must be taken into account (for
example excessive or very unsteady supply pressure requiring
the installation of a pressure reducer).
4.2
Configuration and function
4.2.1 Configuration
Between 2 and 6 vertical high-pressure pumps (for description
and function, please refer to the pump’s Operating Instruction)
are arranged on a baseplate.
Each pump is seated on its own anti-vibration mounts.
The pumps are arranged in line are coupled by mild steel pipes.
On the system side, a swing check valve and a shut-off butterfly
valve are fitted downstream of each pump.
On the suction side, a ball valve or a shut-off butterfly valve are
fitted upstream of each pump as a service valve.
The shut-off elements permit dismantling of individual pumps
without having to drain the pipework. The discharge side non-
return valve ensures that the unit remains filled with water and
prevents backflow through the pumps.
Both headers feature additional connections for draining, venting
and installation of various dry running protection devices.
The accumulator is fitted with an isolating valve. It compensates
discharge-side peak pressures and together with the minimum
operating period, limits the pumps’ switching frequency.
moviBOOST VPt / CL units are started up as a function of
pressure. To this effect, a pressure transmitter is fitted in the
discharge-side piping.
Depending on the number and power of the pumps, the
completely wired control cabinet is either supplied mounted on
the baseplate or as a free-standing cabinet.
Only supplementary and special equipment is supplied fitted on
the unit.
Accessories such as expansion joints, tanks, accumulators,
pressure reducers etc. are supplied with the unit but are not
mounted.
The unit is driven by surface-cooled three-phase squirrel-cage
motors, 50 Hz, air-cooled, 2-pole, KSB standard motor with main
dimensions to IEC. Other motor makes after consultation with
KSB.
up to 2.2 kW 220-240 V/380-420 V,
from 3 kW 380-420 V/660-725 V
enclosure IP 55, thermal class F, up to 4 kW design V18,
from 5.5 kW design V1
4.2.2 Function
moviBOOST VPt / CL is started as a function of pressure and
stopped as a function of demand.
Automatic mode
Two to six pumps are controlled and monitored by a micro-
processor control unit.
Each pump is connected to a frequency inverter and controlled
by the control unit in order to ensure a constant system discharge
pressure of +0.4 bar.
As the demand increases or decreases, the peak load pumps
will be switched on and off automatically. As soon as the demand
increases after one pump has been switched off, another pump
which has not been in operation before is switched on.
After the last (PI-controlled) pump has been switched off and the
demand increases again, the next pump in line is switched on
and connected to the frequency inverter.
Содержание moviBOOST CL
Страница 24: ...moviBOOST VPt CL NOTES ...